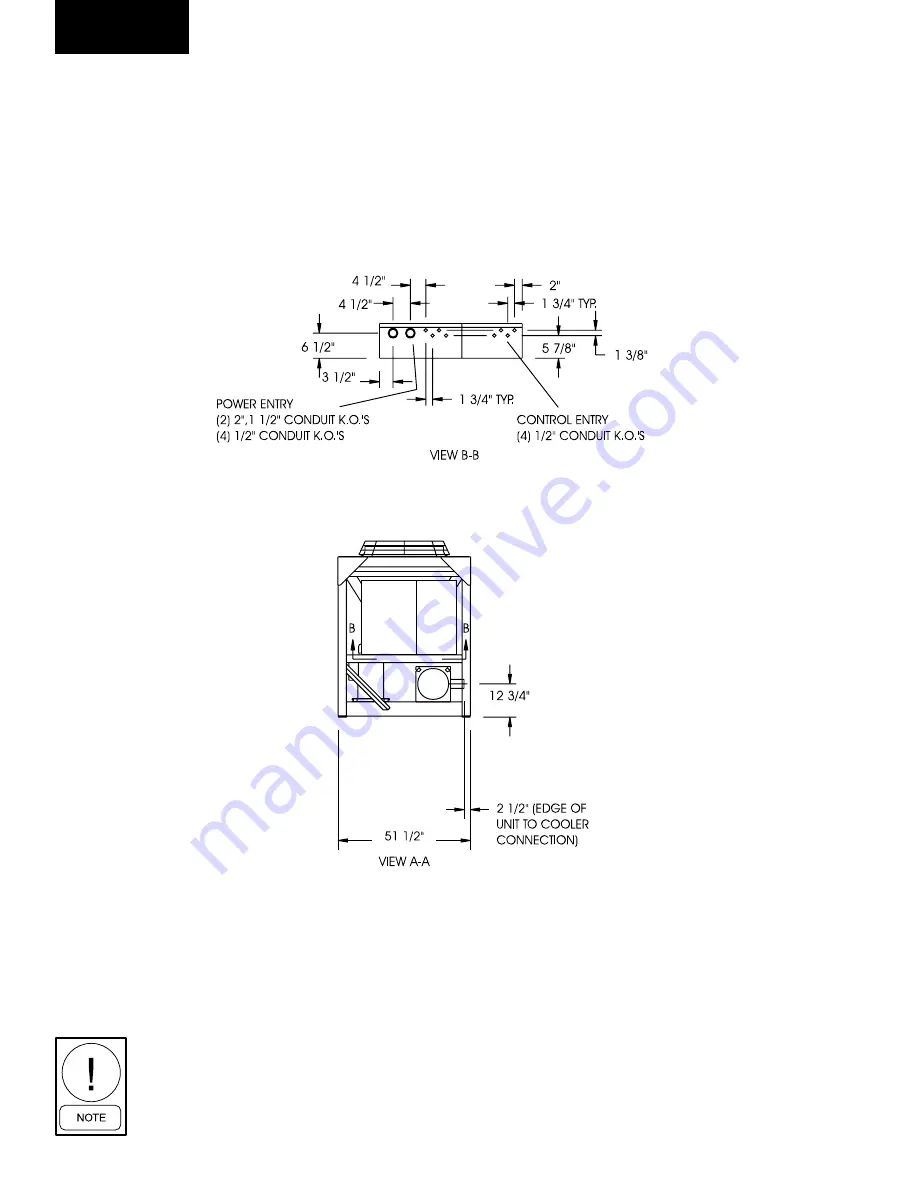
YORK INTERNATIONAL
32
DIMENSIONS (ENGLISH)
YCAL0043SC - YCAL0057SC
Placement on a level surface of free of obstructions (including snow, for winter operation) or air circulation ensures rated
performance, reliable operation, and ease of maintenance. Site restrictions may compromise minimum clearances indicated
below, resulting in unpredictable airflow patterns and possible diminished performance. YORK’s unit controls will optimize
operation without nuisance high-pressure safety cutouts; however, the system designer must consider potential perfor-
mance degradation. Access to the unit control center assumes the unit is no higher than on spring isolators. Recommended
minimum clearances: Side to wall – 6'; rear to wall – 6'; control panel to end wall – 4'0; top – no obstructions allowed;
distance between adjacent units – 10'. No more than one adjacent wall may be higher than the unit.
LD04401
Installation
Summary of Contents for MILLENNIUM YCAL0043SC
Page 106: ...YORK INTERNATIONAL 106 ELEMENTARY DIAGRAM YCAL0043SC YCAL0087SC FIG 11 ELEMENTARY DIAGRAM ...
Page 109: ...YORK INTERNATIONAL 109 FORM 150 62 NM2 This page intentionally left blank ...
Page 110: ...YORK INTERNATIONAL 110 ELEMENTARY DIAGRAM YCAL0107SC FIG 13 ELEMENTARY DIAGRAM ...
Page 112: ...YORK INTERNATIONAL 112 FIG 14 ELEMENTARY DIAGRAM ELEMENTARY DIAGRAM YCAL0107SC LD03534 ...
Page 113: ...YORK INTERNATIONAL 113 FORM 150 62 NM2 This page intentionally left blank ...
Page 114: ...YORK INTERNATIONAL 114 ELEMENTARY DIAGRAM YCAL0117SC YCAL0173SC FIG 15 ELEMENTARY DIAGRAM ...
Page 116: ...YORK INTERNATIONAL 116 ELEMENTARY DIAGRAM YCAL0117SC YCAL0173SC FIG 16 ELEMENTARY DIAGRAM ...
Page 118: ...YORK INTERNATIONAL 118 ELEMENTARY DIAGRAM YCAL0197SC YCAL0253SC FIG 17 ELEMENTARY DIAGRAM ...
Page 120: ...YORK INTERNATIONAL 120 ELEMENTARY DIAGRAM YCAL0197SC YCAL0253SC FIG 18 ELEMENTARY DIAGRAM ...
Page 129: ...YORK INTERNATIONAL 129 FORM 150 62 NM2 This page intentionally left blank ...
Page 130: ...YORK INTERNATIONAL 130 This page intentionally left blank ...
Page 131: ...YORK INTERNATIONAL 131 FORM 150 62 NM2 This page intentionally left blank ...