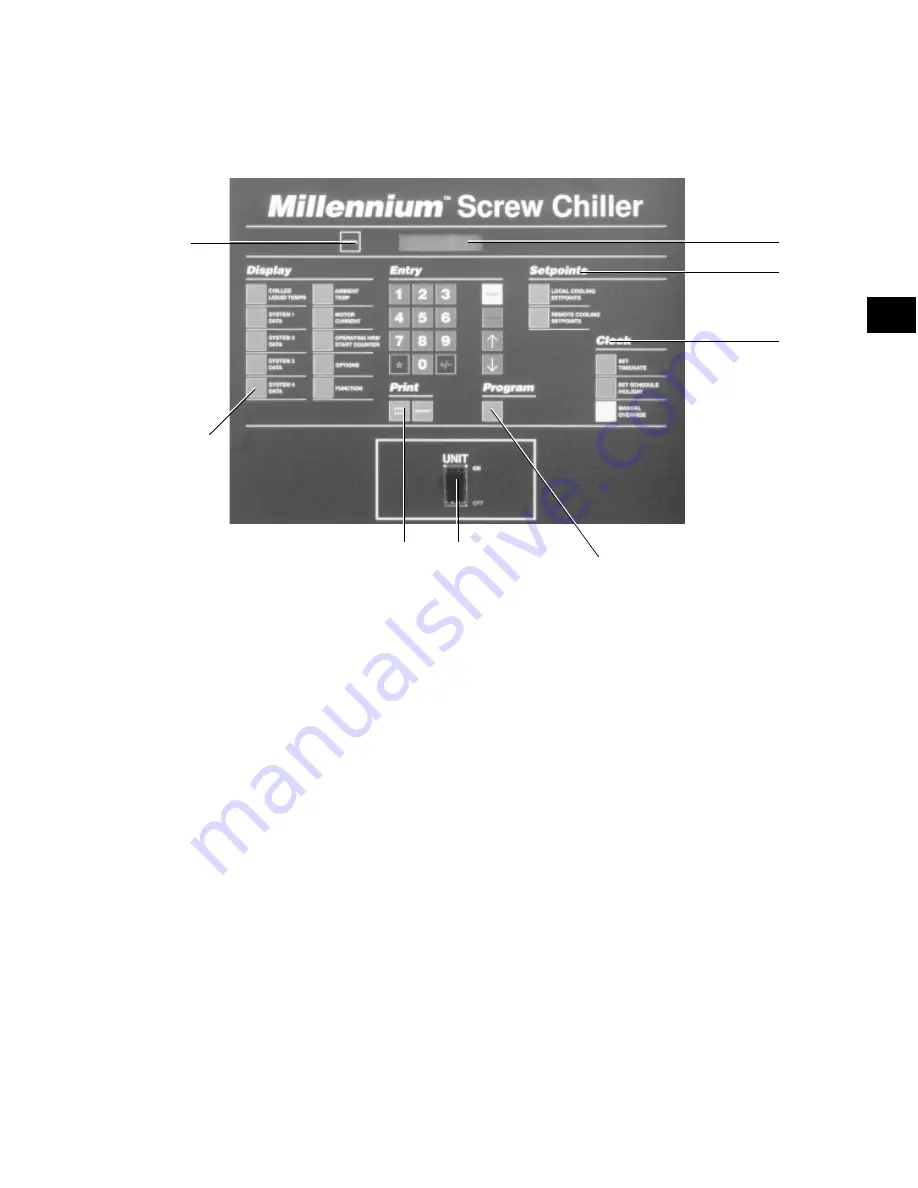
97
YORK INTERNATIONAL
FORM 201.18-NM6
29023A
CHILLER CONTROL PANEL
PROGRAMMING AND DATA ACCESS KEYS
CLOCK
SETPOINTS
PROGRAM &
SETUP KEY
ON / OFF
DISPLAY
INFORMATION KEYS
STATUS
DISPLAY AND STATUS INFORMATION KEYS
Status Key - see Section 2
This key provides a display of the current operational
and/or fault status of the chiller or individual refriger-
ant systems.
Display Keys - see Section 3
Each key provides a real time display of commonly re-
quired information about the chiller and individual sys-
tem operating conditions and settings.
Print Keys - see Section 4
These keys allow control panel display or remote print-
out of both current real-time operating and programmed
data as well as fault history data from recent safety shut-
downs.
ON / OFF ROCKER SWITCH
This switch shuts down the entire chiller when placed
in the OFF position. The switch must be ON for the
chiller to operate.
PROGRAM & SETUP KEYS
Entry Keys - see Section 5
The numeric and associated keys are used for entering
data required for programming the chiller. The ENTER
and
!#
!#
!#
!#
!#
keys are also used for scrolling through infor-
mation available after pressing certain keys.
Setpoints Keys - see Section 6
These keys are used for display and programming of
the local and remote offset chilled liquid temperature
setpoints.
Clock Keys - see Section 7
These keys are used for display and programming of
the clock and operating schedule for the chiller.
Program Key - see Section 8
This key is used for display and programming of the
chiller operational settings and limits.
DISPLAY
8
Summary of Contents for MILLENIUM YCAS Series
Page 47: ...47 YORK INTERNATIONAL FORM 201 18 NM6 7 This page intentionally left blank...
Page 59: ...59 YORK INTERNATIONAL FORM 201 18 NM6 7 This page intentionally left blank...
Page 63: ...63 YORK INTERNATIONAL FORM 201 18 NM6 7 WIRING DIAGRAM WYE DELTA START LD06015...
Page 68: ...68 YORK INTERNATIONAL Technical Data LEGEND 0283 0343 LD06179...
Page 69: ...69 YORK INTERNATIONAL FORM 201 18 NM6 7 LD05957...
Page 70: ...70 YORK INTERNATIONAL Technical Data CONNECTION DIAGRAM SYSTEM WIRING LD06019...
Page 71: ...71 YORK INTERNATIONAL FORM 201 18 NM6 7 COMPRESSOR TERMINAL BOX LD06020...