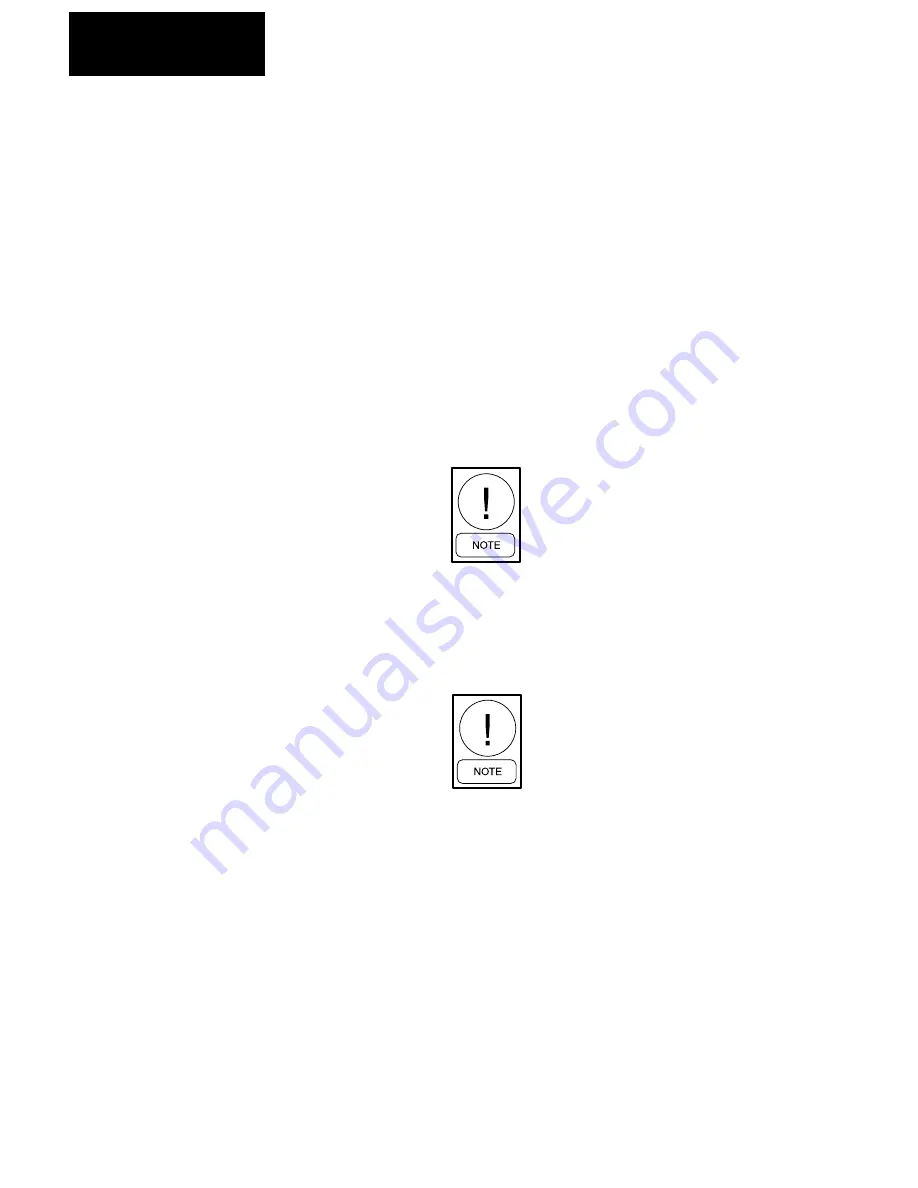
132
YORK INTERNATIONAL
Micro Panel Contents
Compressor Loading
The micro loads and unloads individual compressors
by varying current to the Slide Valve solenoid which
controls oil flow to the slide valve. The slide valve load
solenoid applies oil pressure to the slide valve to over-
come spring pressure from an internal spring, increas-
ing capacity. The internal spring moves the slide valve
in the opposite direction against oil pressure to decrease
capacity.
Whenever chilled liquid leaving temperature is above
the Setpoint, loading current will increase to allow oil
pressure to move the slide valve to increase capacity.
Every 10 seconds, the micro will increment the slide
valve step from 1 to 10 steps according to error (devia-
tion from setpoint) and rate of change of chilled liquid.
The micro will always choose the compressor with the
lowest slide valve position to load on increasing de-
mand, provided the compressor is not pumping down,
has run at least 15 seconds, and is not in a “Limiting”
condition.
Loading Limiting
Load limiting will occur if a system safety threshold is
neared. The anticipatory capability of the micro limits
loading or unloads a system if the micro anticipates a
safety threshold will be exceeded. Under circumstance
where loading is required and one of the systems is near-
ing a threshold, the micro may elect to split the number
of steps that it would normally load a compressor be-
tween more than one compressor. For instance, if sys-
tem 1 were nearing its motor current unload point and
it was scheduled to load, the micro could split a load
signal of 10 steps between system 1 and 2. It could only
load SYS 1 “2” steps while loading SYS 2 “8” Steps.
Under these circumstances, the two systems will not
appear to equalize loading.
Compressor Unloading and Shutdown Sequence
Whenever temperature is below the Setpoint, unload-
ing pulses will be sent to open the unloading port on
the control solenoid to relieve oil pressure on the slide
valve on the compressor with the highest slide valve
step. Opening of the unloading port on the control sole-
noid allows spring pressure to move the slide valve to
decrease capacity. Every 5 seconds, the micro will dec-
rement the compressor with the highest slide valve po-
sition by 1 - 10 steps according to the error (deviation
from Setpoint) and the rate of change of chilled liquid
temperature.
As load drops, the micro will continue to unload the
compressor with the highest slide valve step until all
compressor slide valves are at “0.” At this point, the
last lag compressor will pump down and cycle off, if
chilled liquid temperature drops below “Setpoint - Con-
trol Range/2”. As load continues to decrease and the
lag compressor cycles off, the lead compressor will con-
tinue to unload to a slide valve position of “0” and will
pump down and cycle off if the chilled liquid tempera-
ture drops below “Setpoint – Control Range.”
The
lag compressor may be shut down
before it is fully unloaded to avoid a
Chiller fault on a Low Water Tempera-
ture cut-out under the following
conditions: a) if chilled liquid tem-
perature falls below the low end of the
Control Range (CR) for more than 37
seconds, b) if chilled liquid tempera-
ture drops more than CR/4 below the
low limit of the Control Range.
The lead compressor may be shut down
before it is fully unloaded to avoid a
Chiller Fault on Low Water Tempera-
ture under the following conditions:
a) if chilled liquid temperature drops
2°C below the low limit of the Con-
trol Range (CR), b) if chilled liquid
temperature drops more than CR/2
below the low limit of the Control
Range.
Summary of Contents for MILLENIUM YCAS Series
Page 47: ...47 YORK INTERNATIONAL FORM 201 18 NM6 7 This page intentionally left blank...
Page 59: ...59 YORK INTERNATIONAL FORM 201 18 NM6 7 This page intentionally left blank...
Page 63: ...63 YORK INTERNATIONAL FORM 201 18 NM6 7 WIRING DIAGRAM WYE DELTA START LD06015...
Page 68: ...68 YORK INTERNATIONAL Technical Data LEGEND 0283 0343 LD06179...
Page 69: ...69 YORK INTERNATIONAL FORM 201 18 NM6 7 LD05957...
Page 70: ...70 YORK INTERNATIONAL Technical Data CONNECTION DIAGRAM SYSTEM WIRING LD06019...
Page 71: ...71 YORK INTERNATIONAL FORM 201 18 NM6 7 COMPRESSOR TERMINAL BOX LD06020...