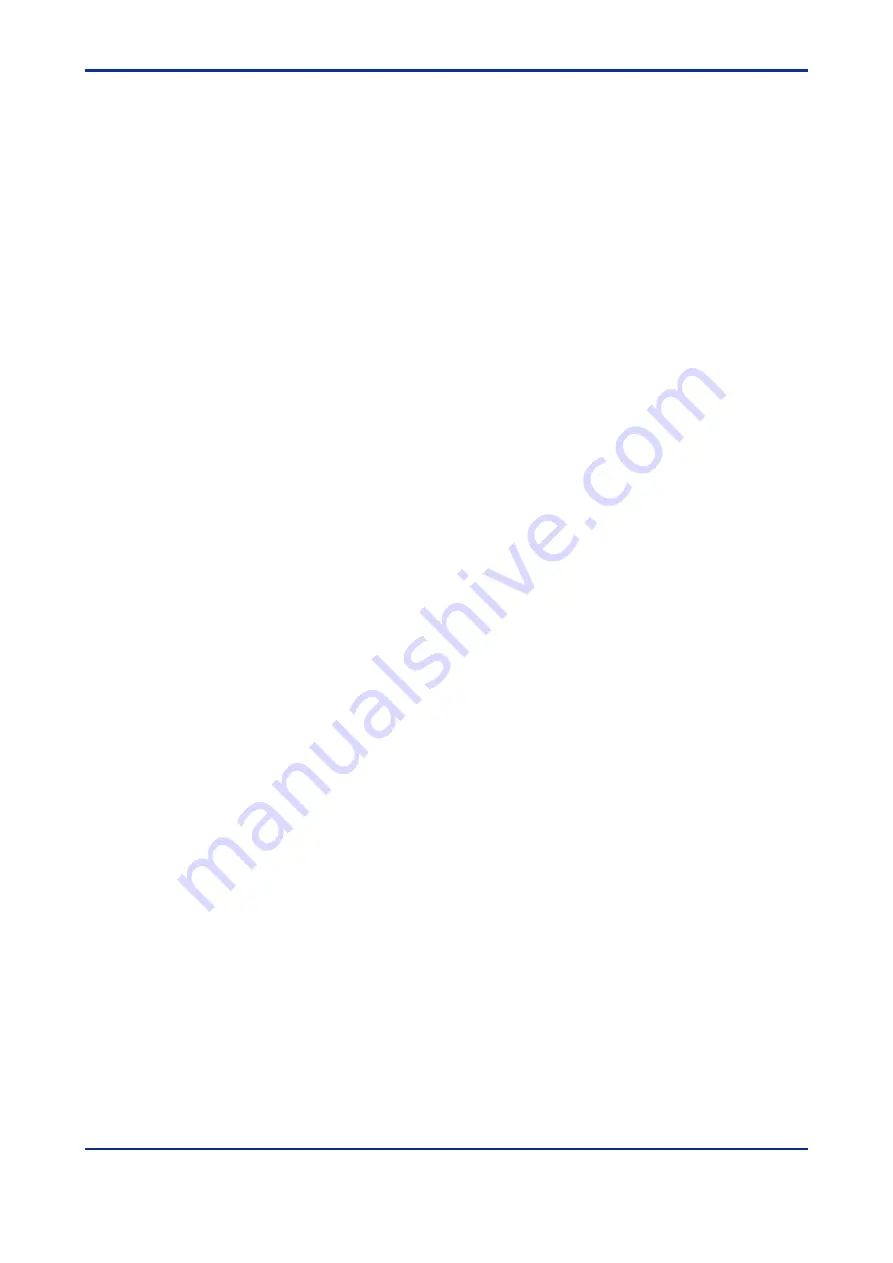
<Toc>
<4. Troubleshooting and Maintenance>
4-3
IM 05D01D02-41E
●
Power Failures of 20 ms or longer
•
The alarm function of the controller continues to work normally. (Alarms with the
stand-by feature temporarily return to their stand-by state, however.)
•
Setup parameters that have already been configured to retain their settings.
•
Auto-tuning is cancelled.
•
After recovery from a power failure, control action resumes in the same mode as the
one before the occurrence of the power failure. The control output begins with the
preset output value.
■
Troubleshooting when the Controller Fails to Operate Correctly
If your control tasks are not successful, check the preset parameters and controller wiring
before concluding the controller to be defective. The following show some examples of
troubleshooting you should refer to in order to avoid the possibility of other problems.
●
The Controller does not Show the Correct Process Variable (PV).
•
The UT350/UT320 controllers have a universal input.
The type of PV input can be set/changed using the parameter “IN”. At this point, the
controller must be wired correctly according to the selected type of PV input. Check
the wiring first if the controller fails to show the correct PV. To do this, refer to “2. Initial
Settings.”
With the parameters “RH”, “RL”, “SDP”, “SH” and “SL”, it is possible to scale the input
signal and change its number of decimal places. Also check that these parameters are
configured correctly.
●
The Controller does not Provide any Control Output or the Control Output
does not Change at all.
•
The UT350/UT320 controllers have a universal output.
The type of control output can be set/changed using the parameter “OT”.
At this point, the controller must be wired correctly according to the selected type of
control output. Check the wiring first if the controller provides no control output. To do
this, refer to “1.5 Terminal Wiring Diagrams.”
With the parameters “OH” and “OL”, it is possible to set/change the high and low limits
of control output. The control output may not change at all, however, because of
restrictions on these parameters. Also check the restrictions on these parameters.
•
The control output can only be changed when the controller is in the MAN mode.
If the MAN lamp is off (i.e., the controller is in the AUTO mode), you cannot change the
control output using key operation.
●
The control output does not change soon after the target setpoint SP has
been changed.
•
If this happens, check the setpoint of the parameter “C.MD”. In cases where fixed-
point control is selected as the PID control mode (C.MD = 1), tracking based on the I-
term works to prevent the control output from changing suddenly even if the target
setpoint SP is varied.
The control output therefore may appear to be working incorrectly at first; however it
gradually adapts itself to the new target setpoint. Be especially careful when the
controller is in the fixed-point control mode; the control output may fail to change and
therefore result in a loss of control if you change the target setpoint SP too frequently.
1st Edition : May 31,2000-00
Summary of Contents for UT350
Page 2: ...Blank Page...
Page 46: ...Blank Page...
Page 56: ...Blank Page...
Page 82: ...Blank Page...