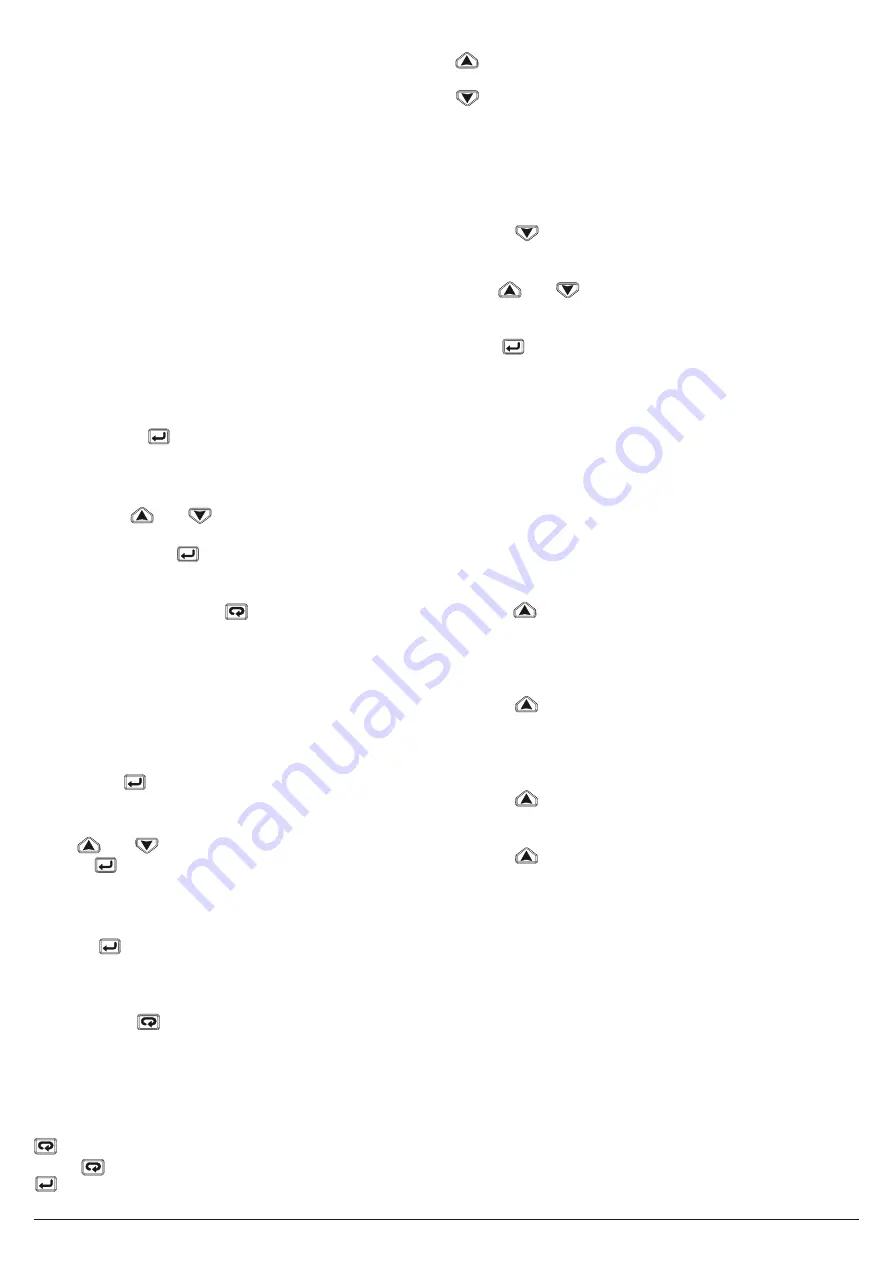
Yokogawa Electric Corporation - TC10 - ENGINEERING MANUAL - PAG. 23
modification procedure is closed.
When you desire to remove the time out (e.g.
for the first configuration of an instrument) you
can use a password equal to 1000 plus the
programmed password
(e.g. 1000 + 20 [default] = 1020).
It is always possible to manually End the
parameter configuration procedure (see below).
3.
During parameter modification the instrument
continues to perform the control.
In certain conditions (
e.g. when a parameter
change can produces a heavy bump to the
process)
it is advisable to temporarily stop the
controller from controlling during the programming
procedure (its control output will be Off).
A
password equal to 2000 + the programmed value
(e.g. 2000 + 20 = 2020) will switch the control out
off during configuration. The control will restart
automatically when the parameter modification
procedure will be manually ended.
4.
Push
button.
5.
The instrument will show on the upper display the
acronym of the first parameter promoted to this
level and on the lower display its value.
6.
By
and
buttons assign to this parameter
the desired value.
7.
Press the
button in order to memorize the
new value and go to the next parameter.
8.
When you want to come back to the “standard
display” push the
button for more than 3 s.
7.3 HOW TO SEE BUT NOT MODIFY THE “LIMITED
ACCESS PARAMETERS”
Sometime it is necessary to give to the operator the possibility
to see the value assigned to the parameter promoted in the
Limited Access level but it is important that all changes are
made by authorized personnel only.
In this cases, proceed as follows:
1.
Press the
button for more than 3 seconds;
2.
The upper display will show
PASS
while the lower display
will show
0
;
3.
By
and
button set the value
-181
;
4.
Push
button;
5.
The upper display will show the acronym of the first
parameter promoted to the level 2 and lower display will
show its value;
6.
Using
button it is possible to see the value assigned
to all parameter present in level 2 but it will not be
possible to modify it;
7.
It is possible to come back to the “standard display” by
pushing the
button for more than 3 seconds or by
pushing no pushbutton for more than 10 seconds.
7.4 AUTOMATIC MODE
7.4.1 Keyboard function when the instrument
is in Auto mode
Performs the action programmed by [121] uSrb
(
button function during RUN TIME) parameter.
Allows to entrer the parameter modification procedures.
Allows to start the “Direct set point modification” fun-
ction (see below).
Allows to display the “additional informations”
(see below).
7.4.2 Direct set point modification
This function allows to modify rapidly the set point value
selected by [83] A.SP (selection of the active Set point).
The instrument is showing the “standard display”.
1.
Push
button.
The upper display shows the acronym of the selected set
point (e.g. SP2) and the lower display will show its value.
2.
By
and
buttons, assign to this parameter the
desired value.
3.
Do not push any button for more than 10 second or push
the
button.
In both cases the instrument memorize the new value and
come back to the “standard display”.
Note:
If the selected set point has not been promoted to the
Operator level, the instrument allows you to see the
value but not to modify it.
7.4.3 Additional information
This instrument is able to show you some additional
informations that can help you to manage your system.
The additional informations are related to how the instrument
is programmed, hence in many cases, only part of this
information is available.
1.
When the instrument is showing the “standard display”
push
button.
The lower display will show
H
or
c
followed by a number.
This value is the current power output applied to the
process. The
H
show you that the action is a Heating action
while the
c
show you that the action is a Cooling action.
2.
Push
button again. When the wattmeter function
is running the lower display will show
U
followed by the
measured energy.
Note:
The energy calculation will be in accordance with
the [134] Co.tY parameter setting.
3.
Push
button again. When the “Worked time count”
is running the lower display will show
d
for days or
h
for
hours followed by the measured time.
4.
Push
button again. The instrument returns to the
“standard display”.
Note:
The additional information visualization is subject to
a time out. If no button is pressed for more than 5
second the instrument comes automatically back to
the Standard display.
7.4.4 Display management
This instrument allows you to program (see parameter
[125] diS.t the time out of the display.
This function allows to turn OFF the display when no alarm
is present and no action is made on the instrument.
When [125] diS.t is different to OFF (display ever ON) and
no button is pressed for more than the programmed time
out, the display goes OFF and only 4 segments of the less
significant digit are turned ON in sequence in order to show
that the instrument is working correctly.
If an alarm occurs or a button is pressed, the display will
come back to the normal operation.