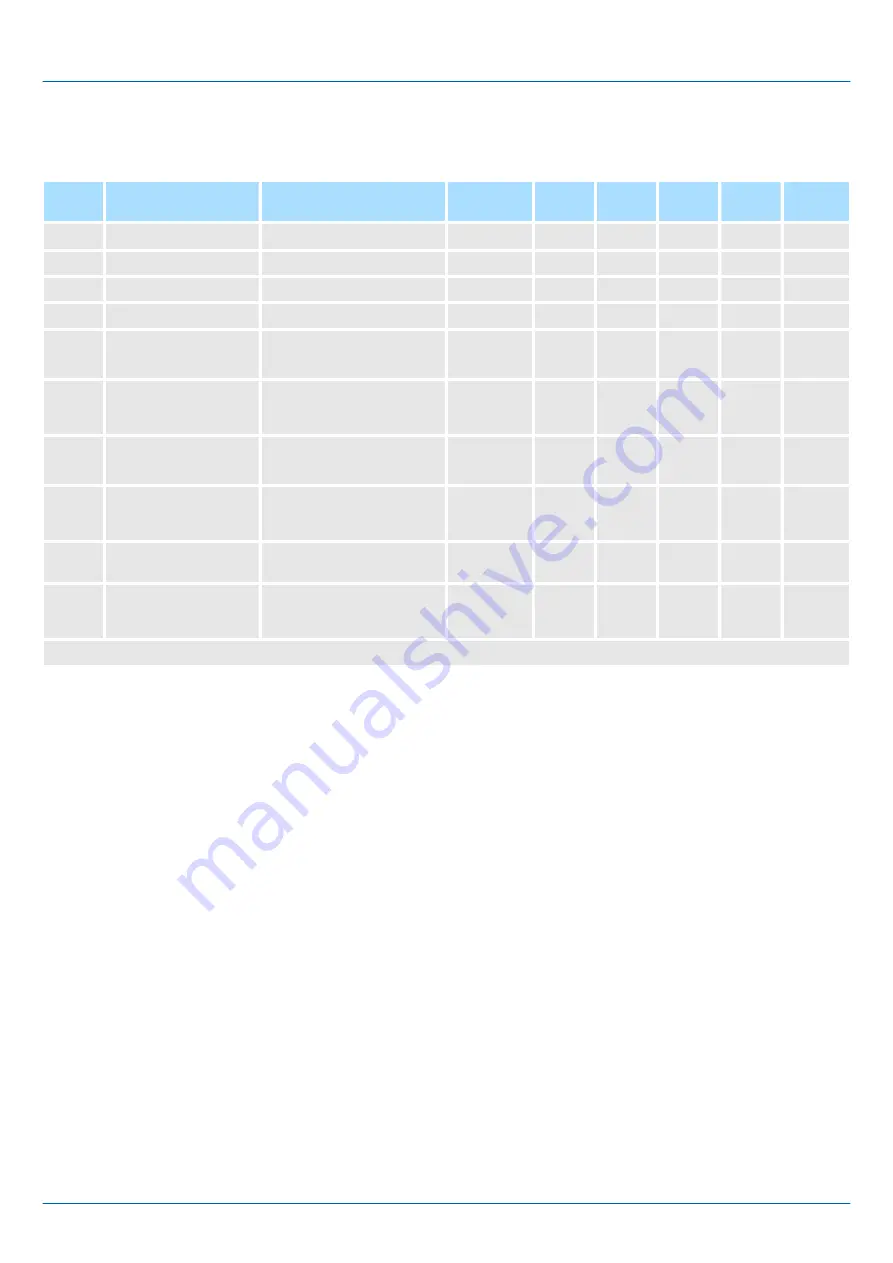
2.5.2 FSoE communication parameters
Sub-
index
Name
Description / range of
values
Type
Bit
Offset
Access Default
Transfer
1
0
SubIndex 000
USINT
8
0
ro
9
1
Version
Supported FSoE version
STRING (2)
16
16
ro
-
No
2
Safety Address
Safety address
UINT
16
32
ro
0
No
3
FSoE connection ID
Safety connection ID
UINT
16
48
ro
-
No
4
Watchdog Time
Safety watchdog time in ms
20 - 65534
UINT
16
64
ro
150
Yes
5
Unique Device ID
Unique device ID
ARRAY
[0..5] OF
BYTE
48
80
ro
-
No
6
Connection Type
0: Master connection
1: Slave connection
UINT
16
128
ro
1
No
7
ComParameterLength
Length of communication
parameters in the parameter
set
UINT
16
144
ro
2
Yes
8
ApplParameterLength
Length of application param-
eters in the parameter set
UINT
16
160
ro
16
Yes
9
SRA CRC
CRC checksum of the corre-
sponding application param-
eter set
UDINT
32
176
ro
-
No
1) Parameters that are marked with
‘Yes’
are transferred via the FSoE mechanism once when the FSoE master system is started.
n
The
watchdog time
parameter determines the monitoring time for the communication
between the safety PLC and the System SLIO safety module.
n
Within the monitoring time, at least one valid telegram must be exchanged between
the safety PLC and the System SLIO safety module. In this case, the I/O data of the
EtherCAT telegrams are correspondingly copied into the I/O areas of the safety PLC.
n
In the safety PLC, the I/O data of the EtherCAT telegrams are correspondingly copied
into the I/O areas of the safety PLC.
n
If this condition is not fulfilled, a safe state is initiated by the safety PLC or by the
System SLIO safety module.
n
The monitoring time must be selected so that telegram runtimes are tolerated, but a
break in the connection is detected quickly enough.
n
The monitoring time can be specified in steps of 1ms. The possible range of values
(20 - 65534 ms) is specified by the device description file.
n
Information on the calculation can be found below.
Record set 0x9001
Watchdog time
(FSoE_WD_Time)
VIPA System SLIO
Product description
SDI 4xDC 24V - FSoE Parameter record set > FSoE communication parameters
HB300 | SM-S | 02x-1SD10 | en | 20-02
39