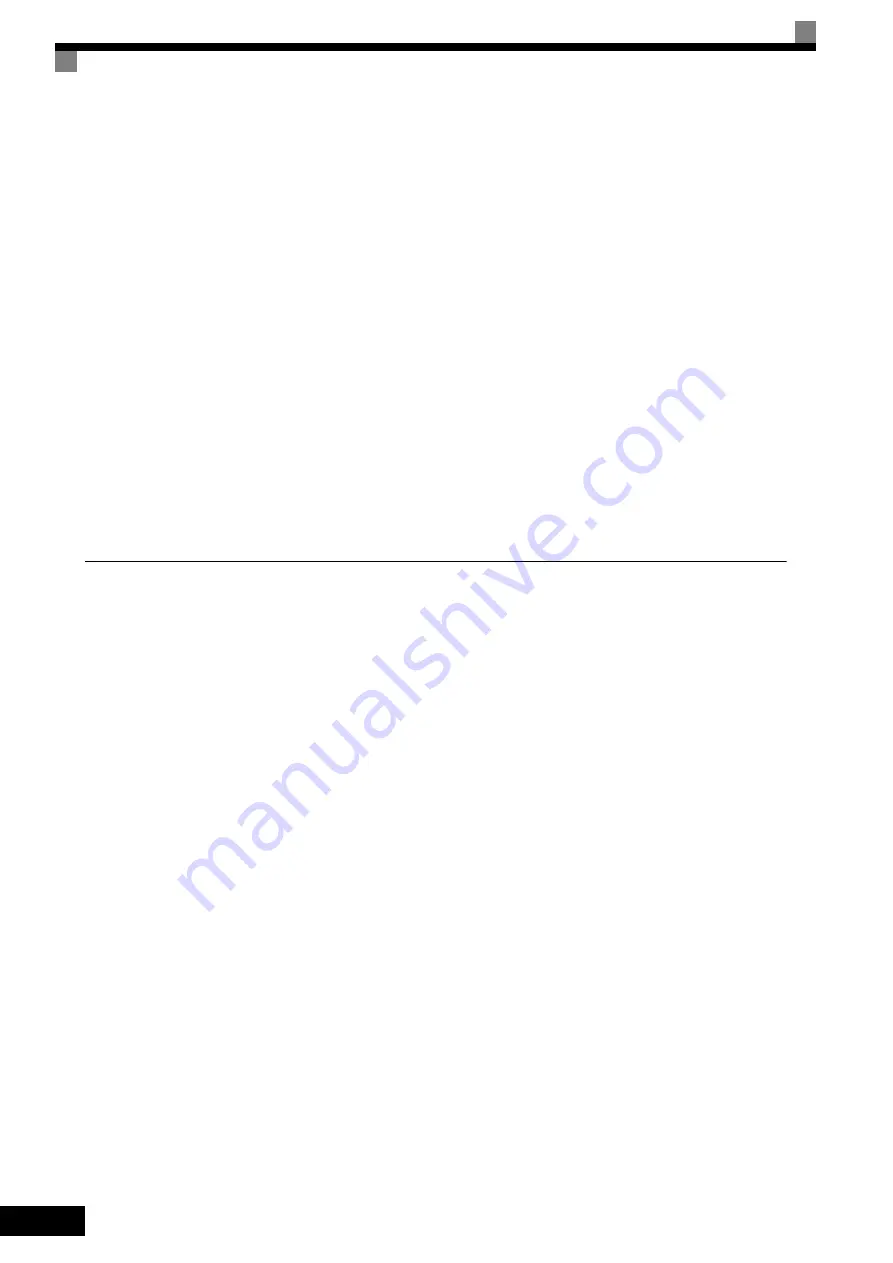
7
-30
The torque limit has been reached.
When a torque limit has been set in constants L7-01 to L7-04, no torque will be output beyond that limit. This
can cause the deceleration time to be too long. Check to be sure that the value set for the torque limit is suit-
able.
If H3-09 (Multi-function Analog Input Terminal A2 Function Selection) or H3-05 (Multi-function Analog
Input Terminal A3 Function Selection) is set to 10, 11, 12 or 15 (positive and negative torque limit), check to
be sure that the analog input value is suitable.
If the Vertical-axis Load Drops When Brake is Applied
The sequence is incorrect. The Inverter goes into DC injection braking status for 0.5 seconds after deceleration
is completed. (This is the factory-set default.)
To ensure that the brake holds, set frequency detection 2 (H2-01 = 5) for the multi-function contact output ter-
minals (M1 and Mw) so that the contacts will turn OFF when the output frequency is greater than L4-01 (3.0
to 5.0 Hz). (The contacts will turn ON below L4-01.)
There is hysteresis in frequency detection 2 (i.e., a frequency detection width, L4-02 = 2.0 Hz). Change the
setting to approximately 0.5 Hz if there are drops during stop. Do not use the multi-function contact output run
signal (H2-01 = 0) for the brake ON/OFF signal.
If the Motor Overheats
Take the following steps if the motor overheats.
The load is too big.
If the motor load is too heavy and the motor is used with the effective torque exceeding the motor's rated
torque, the motor will overheat. Some motor rating are given for short period performance and are not contin-
uous ratings. Reduce the load amount by either lightening the load or lengthening the acceleration/decelera-
tion time. Also consider increasing the motor capacity.
The ambient temperature is too high.
The motor rating is determined within a particular ambient operating temperature range. The motor will burn
out if it is run continuously at the rated torque in an environment in which the maximum ambient operating
temperature is exceeded. Lower the motor's ambient temperature to within the acceptable ambient operating
temperature range.
The withstand voltage between the motor phases is insufficient.
When the motor is connected to the Inverter output, a surge is generated between the Inverter switching and
the motor coil. Normally the maximum surge voltage is three times the Inverter's input power supply voltage
(i.e., 1,200 V for 400 V Class). Be sure to use a motor with a withstand voltage between the motor phases that
is greater than the maximum surge voltage. In particular, when using a 400 V Class Inverter, use a special
motor for Inverters.
Autotuning has not been performed for vector control
Vector control will not perform if autotuning has not been performed. Perform autotuning, or set the motor
constants through calculations. Alternatively, change the Control Method Selection (A1-02) to V/f control (0
or 1).