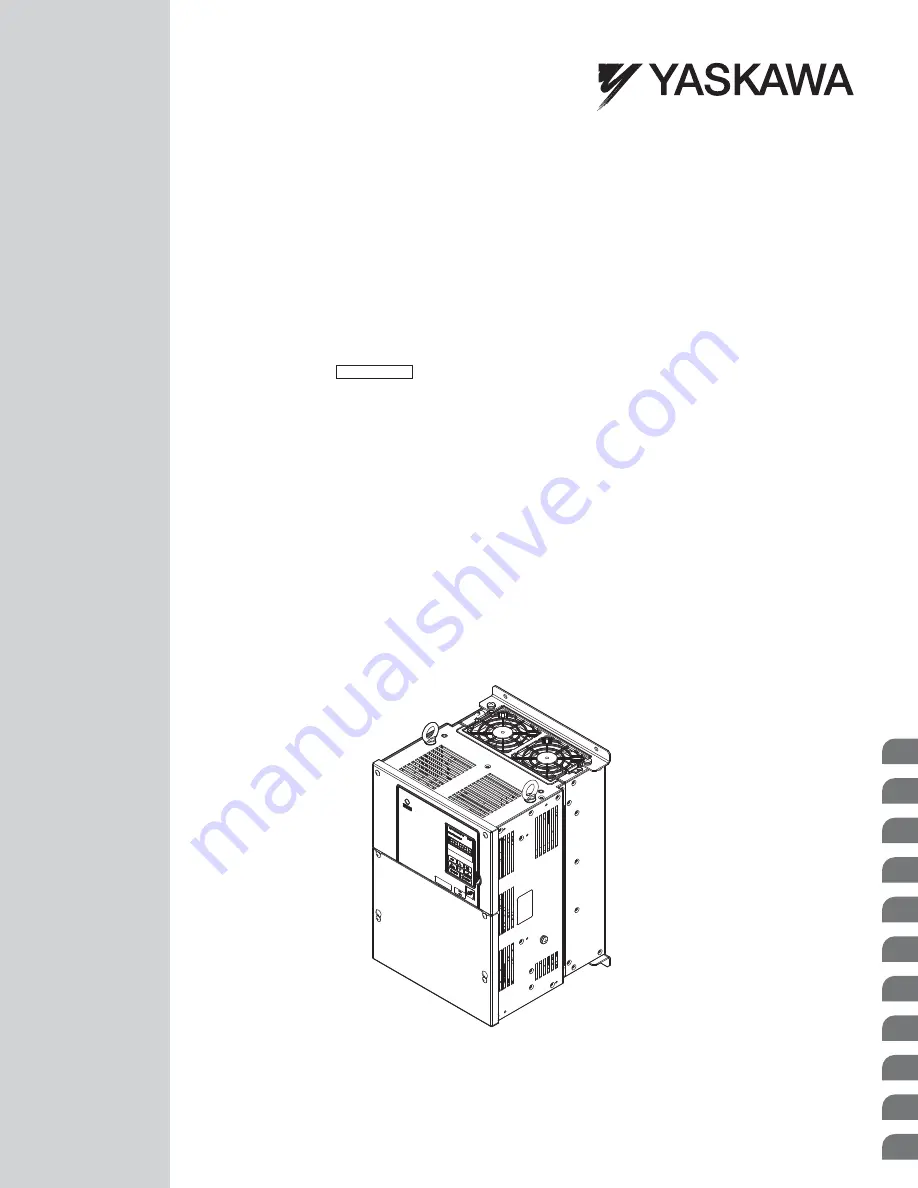
YASKAWA D1000 Series
Power Regenerative Converter
Instruction Manual
MANUAL NO. TOEP C710656 07A
Models: 200 V Class, Three-Phase Input: 5 to 130 kW
400 V Class, Three-Phase Input: 5 to 630 kW
To properly use the product, read this manual thoroughly and retain
for easy reference, inspection, and maintenance. Ensure the end user
receives this manual.
Type: CIMR-DU
Standards Compliance
E
A
B
C
D
A
B
C
D
1
2
3
4
5
6
7
1
2
3
4
5
6
7
Receiving
Mechanical Installation
Electrical Installation
Start-Up Programming &
Operation
Troubleshooting
Periodic Inspection &
Maintenance
Standard Configuration Devices,
Peripheral Devices, and Options
Specifications
Parameter List
MEMOBUS/Modbus
Communications