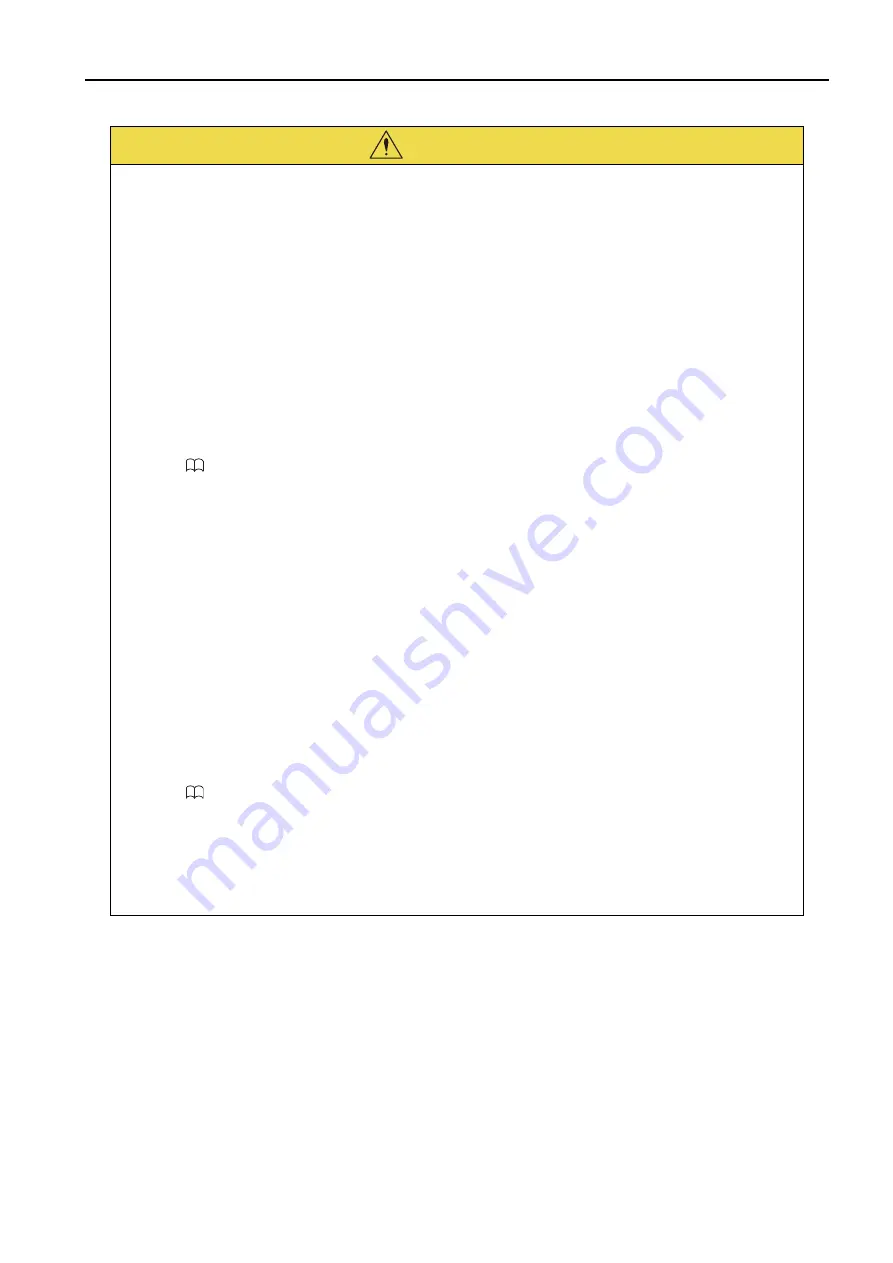
xxi
C
A
UTION
Design the system to ensure safety even when problems, such as broken signal lines, occur.
For example, the P-OT and N-OT signals are set in the default settings to operate on the safe
side if a signal line breaks. Do not change the polarity of this type of signal.
When overtravel occurs, the power supply to the motor is turned OFF and the brake is released.
If you use the Servomotor to drive a vertical load, set the Servomotor to enter a zero-clamped
state after the Servomotor stops. Also, install safety devices (such as an external brake or
counterweight) to prevent the moving parts of the machine from falling.
Always turn OFF the servo before you turn OFF the power supply. If you turn OFF the main cir-
cuit power supply or control power supply during operation before you turn OFF the servo, the
Servomotor will stop as follows:
•
If you turn OFF the main circuit power supply during operation without turning OFF the servo, the
Servomotor will stop abruptly with the dynamic brake.
•
If you turn OFF the control power supply without turning OFF the servo, the stopping method that is
used by the Servomotor depends on the model of the SERVOPACK. For details, refer to the manual
for the SERVOPACK.
•
If you use a SERVOPACK with the Dynamic Brake Hardware Option, the Servomotor stopping meth-
ods will be different from the stopping methods used without the Option or with other Hardware
Options. For details, refer to the following manual.
Σ
-7-Series
Σ
-7S/
Σ
-7W SERVOPACK with Dynamic Brake Hardware Option Specifications Product Manual
(Manual No.: SIEP S800001 73)
Do not use the dynamic brake for any application other than an emergency stop.
There is a risk of failure due to rapid deterioration of elements in the SERVOPACK and the risk of
unexpected operation, machine damage, burning, or injury.
Implement interlock signals and other safety circuits external to the SERVOPACK to ensure
safety in the overall system even if the following conditions occur.
•
SERVOPACK failure or errors caused by external factors
•
Shutdown of operation due to SERVOPACK detection of an error in self-diagnosis and the subse-
quent turning OFF or holding of output signals
•
Holding of the ON or OFF status of outputs from the SERVOPACK due to fusing or burning of output
relays or damage to output transistors
•
Voltage drops from overloads or short-circuits in the 24-V output from the SERVOPACK and the sub-
sequent inability to output signals
•
Unexpected outputs due to errors in the power supply, I/O, or memory that cannot be detected by
the SERVOPACK through self-diagnosis.
There is a risk of injury, device damage, or burning.
Observe the setting methods that are given in the manual for the following parameters.
•
Parameters for absolute position detection when the axis type is set to a finite-length axis
•
Parameters for simple absolute infinite-length position control when the axis type is set to an infinite-
length axis
Σ
-7-Series
Σ
-7C SERVOPACK Motion Control User’s Manual (Manual No.: SIEP S800002 03)
If any other methods are used, offset in the current position when the power supply is turned OFF
and ON again may result in device damage.
OL
48 (Zero Point Position Offset in Machine Coordinate System) is always valid when the
axis type is set to a finite-length axis. Do not change the setting of OL
48 while the
SERVOPACK is operating.
There is a risk of machine damage or an accident.