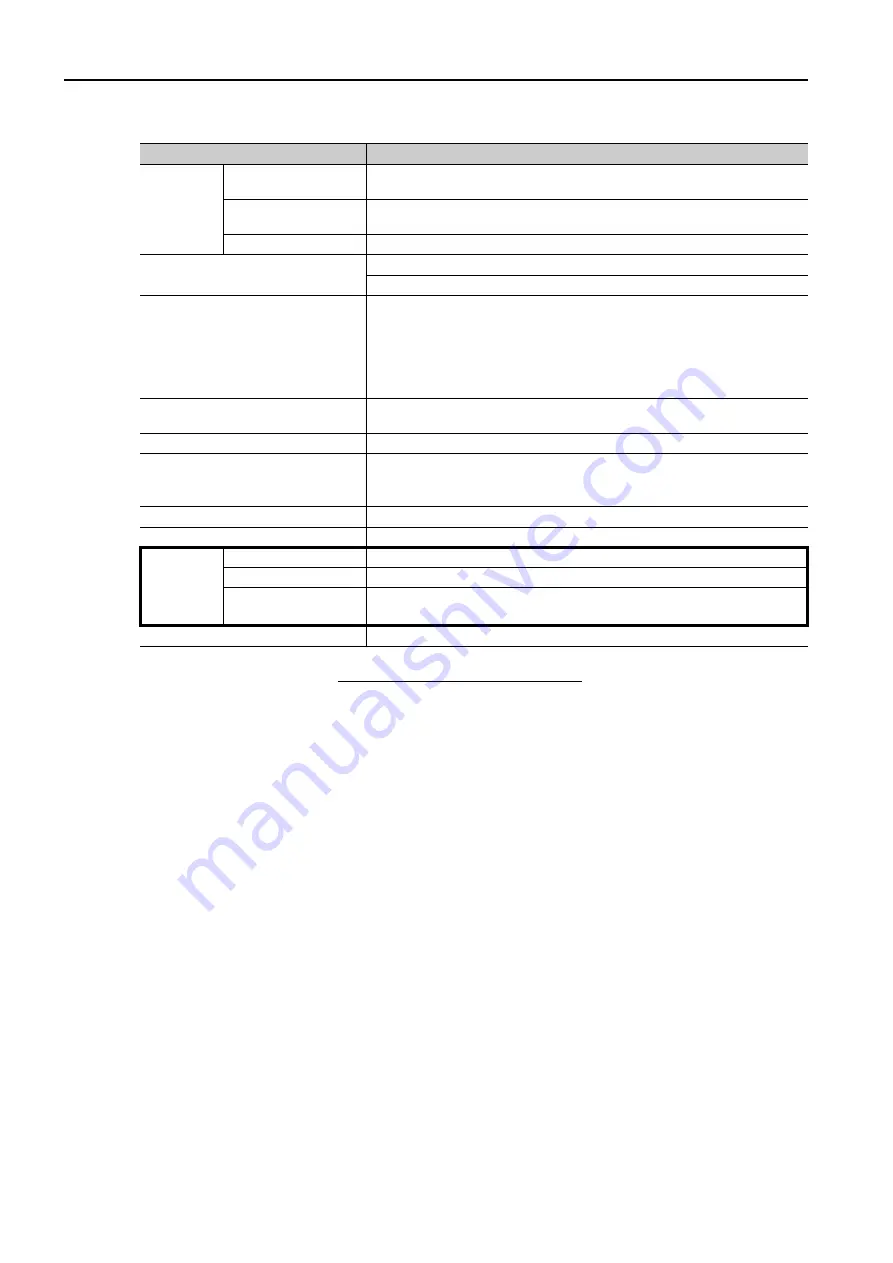
2.1 General Specifications
2.1.1
Σ
-7W
2-4
*1.
The coefficient of speed fluctuation for load fluctuation is defined as follows:
*2.
Always perform risk assessment for the system and confirm that the safety requirements are met.
Reference
Method
Performance
Position, speed, or torque control with MECHATROLINK-III communi-
cations
Reference Input
MECHATROLINK-III commands (sequence, motion, data setting, data
access, monitoring, adjustment, etc.)
Profile
MECHATROLINK-III standard servo profile
MECHATROLINK-III Communica-
tions Setting Switches
Rotary switch (S1 and S2) positions: 16
Number of DIP switch (S3) pins: 4
Analog Monitor (CN5)
Number of points: 2
Output voltage range:
±
10 VDC (effective linearity range:
±
8 V)
Resolution: 16 bits
Accuracy:
±
20 mV (Typ)
Maximum output current:
±
10 mA
Settling time (
±
1%): 1.2 ms (Typ)
Dynamic Brake (DB)
Activated when a servo alarm or overtravel (OT) occurs, or when the
power supply to the main circuit or servo is OFF.
Regenerative Processing
Built-in
Overtravel (OT) Prevention
Stopping with dynamic brake, deceleration to a stop, or coasting to a
stop for the P-OT (Forward Drive Prohibit) or N-OT (Reverse Drive Pro-
hibit) signal
Protective Functions
Overcurrent, overvoltage, low voltage, overload, regeneration error, etc.
Utility Functions
Gain adjustment, alarm history, jogging, origin search, etc.
Safety
Functions
Inputs
/HWBB1 and /HWBB2: Base block signals for Power Modules
Output
EDM1: Monitors the status of built-in safety circuit (fixed output).
Applicable
Standards
*2
ISO13849-1 PLe (Category 3), IEC61508 SIL3
Applicable Option Modules
None
Continued from previous page.
Item
Specification
×
100%
Coefficient of
s
peed fluctuation =
No-load motor
s
peed - Total-load motor
s
peed
Rated motor
s
peed