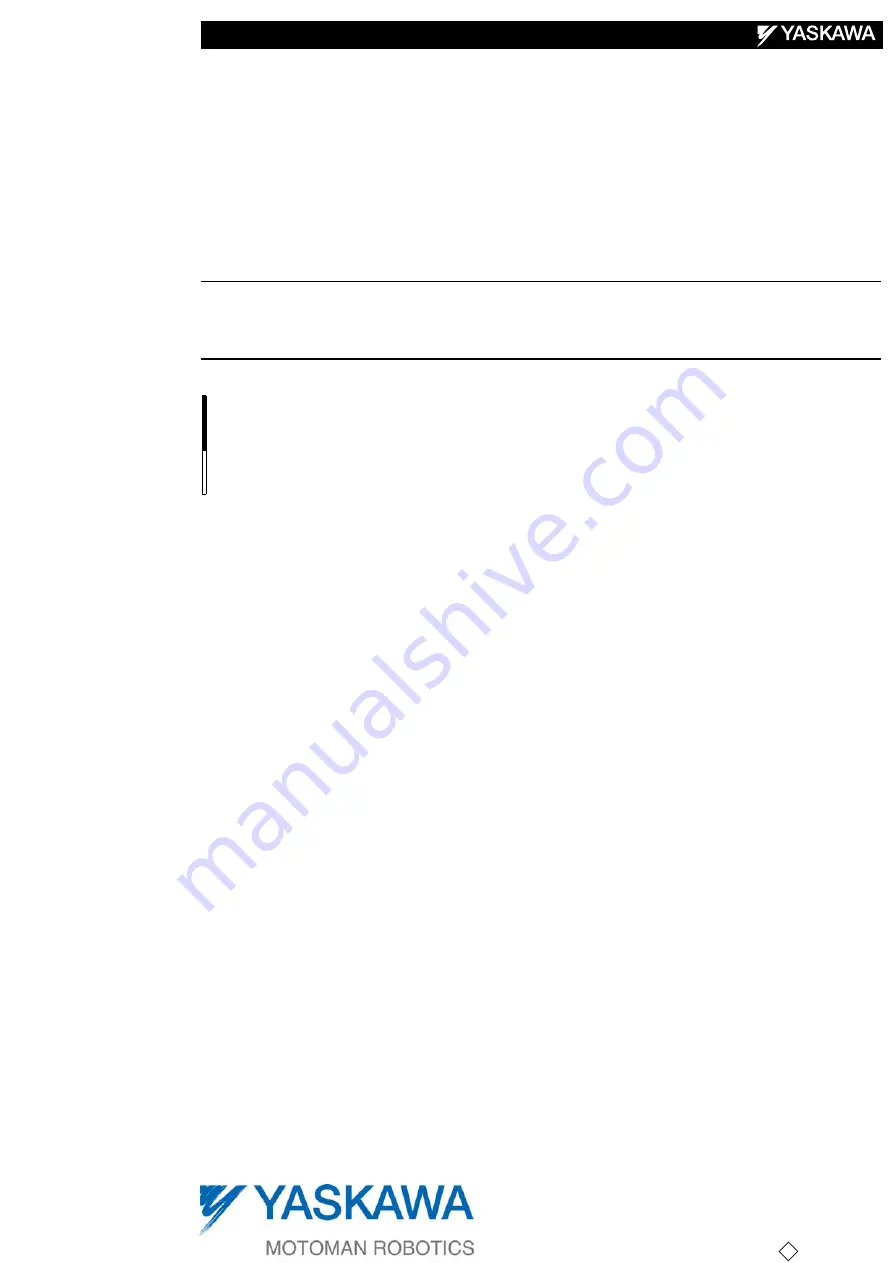
MANUAL NO.
1
150880-1CD
Part Number:
150880-1CD
Revision:
1
MOTOADMIN
DX100, NX100, AND XRC MANUAL
Upon receipt of the product and prior to installation, initial operation, or maintenance read these
instructions thoroughly and retain for future reference.
MOTOMAN INSTRUCTIONS
DX100, NX100, or XRC INSTRUCTIONS
DX100, NX100, or XRC OPERATOR’S MANUAL
DX100, NX100, or XRC MAINTENANCE MANUAL
The DX100, NX100, or XRC operator’s manual above corresponds to specific usage.
Be sure to use the appropriate manual.
1/55
Summary of Contents for MOTOMAN DX100
Page 14: ...MotoAdmin 14 55...