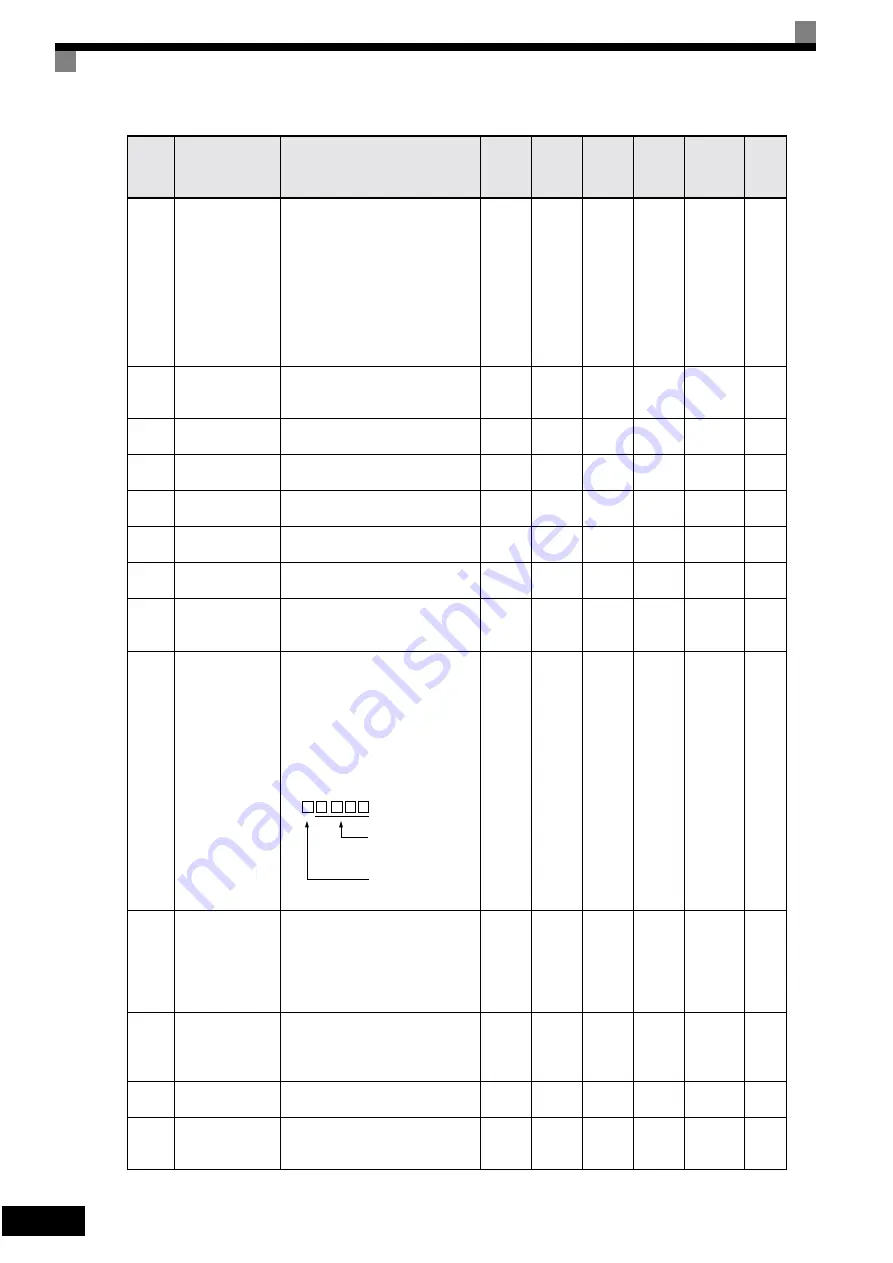
5
-16
b5-12
Selection of PI
feedback signal
loss detection
0: No detection of PI feedback
loss.
1: Detection of PI feedback loss.
Operation continues during
detection, the fault contact is not
operated.
2: Detection of PI feedback loss.
The motor coasts to stop at
detection, and the fault contact
operates.
0 to 2
0
No
A
1B0H
6-111
b5-13
PI feedback loss
detection level
Sets the PI feedback loss detection
level as percentage using the maxi-
mum output frequency as 100%.
0 to 100
0%
No
A
1B1H
6-84
b5-14
PI feedback loss
detection time
Sets the PI feedback loss detection
time.
0.0 to
25.5
1.0 s
No
A
1B2H
6-84
b5-15
Sleep function
operation level
Sets the sleep function start level as
a frequency.
0.0 to
200.0
0.0 Hz
No
A
1B3H
6-84
b5-16
Sleep operation
delay time
Sets the delay time until the sleep
function starts.
0.0 to
25.5
0.0 s
No
A
1B4H
6-84
b5-17
Accel/decel time
for PI reference
Sets the accel/decel time for the PI
Softstarter (SFS).
0.0 to
25.5
0.0 s
No
A
1B5H
6-84
b5-18
PI Setpoint Selec-
tion
0: Disabled
1: Enabled
0 to 1
0
No
A
1DCH
6-84
b5-19 PI Setpoint
PI-target value
0.00 to
100.00
%
0
Yes
A
1DDH
6-84
b5-20
PI Setpoint Scal-
ing
Sets the unit for b5-19, U1-38 and
U1-24
0: 0.01 Hz
1: 0.01% (the maximum output
frequency E1-04 is taken as
100%.
2 – 39: rpm, set value is equal to
motor poles
40 – 39999: User desired display
0 to
39999
0
No
A
1E2H
6-84
b5-21
Sleep Function
Selection
Sets the operation method of the PI
sleep function
0: Output frequency before Soft-
starter (SFS)
1: Frequency reference/PI target
2: Snooze
0 to 2
0
No
A
1E3H
6-85
b5-22 Snooze Level
Sets the frequency level at which
the snooze operation starts as per-
centage of the max. output fre-
quency.
0 to
100%
0
Yes
A
1E4H
6-85
b5-23
Snooze Delay
Time
Sets a delay timer for the snooze
function
0 to
3600 s
0 s
No
A
1E5H
6-85
b5-24 Wake-Up Level
Sets the feedback level at which the
inverter wakes up from snooze
operation.
0 to 100
%
0
No
A
1E6H
6-85
Con-
stant
Number
Name
Description
Setting
Range
Factory
Setting
Change
during
Opera-
tion
Access
Level
MEMO-
BUS
Register
Page
Sets the display value
for 100 %.
Sets the number of
decimal digits.
Artisan Technology Group - Quality Instrumentation ... Guaranteed | (888) 88-SOURCE | www.artisantg.com