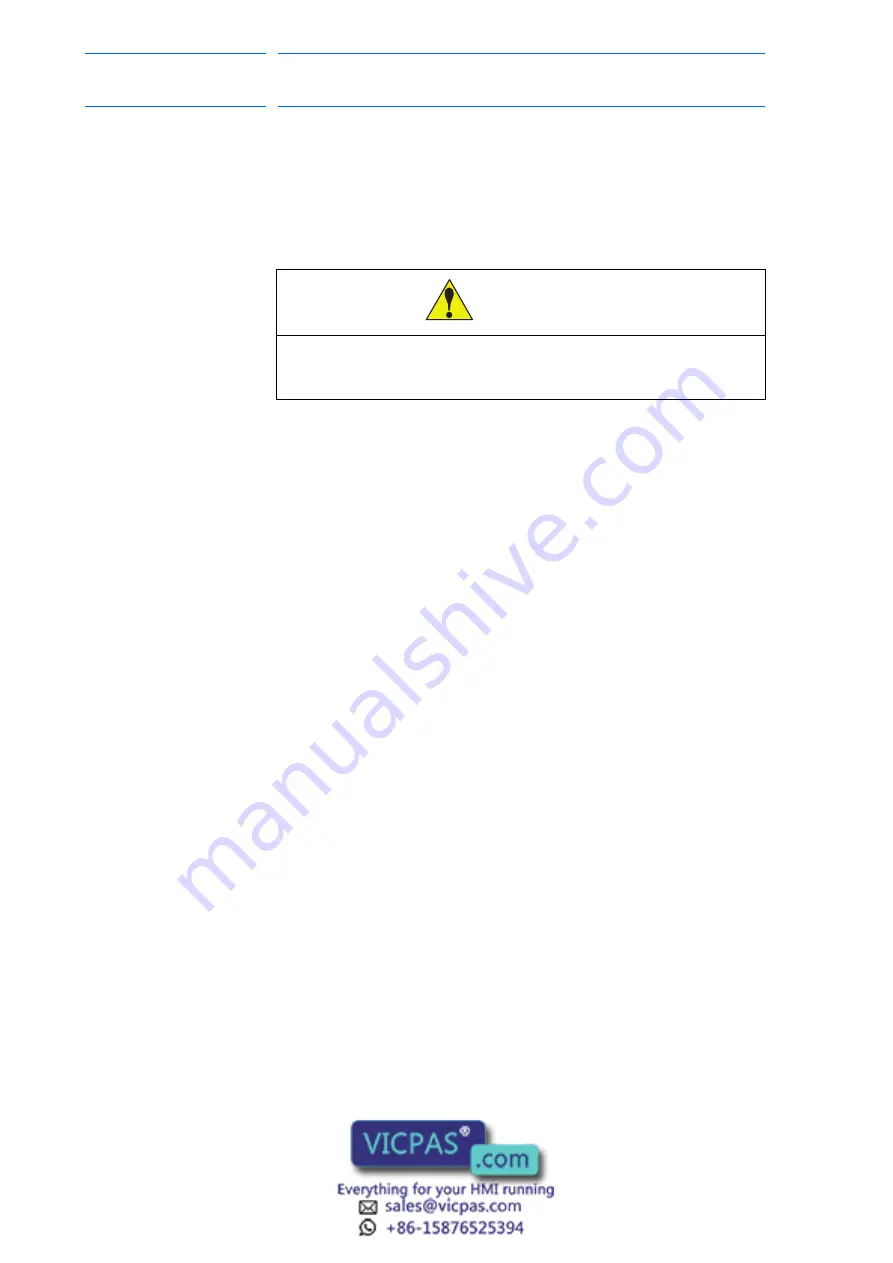
4 Operation
4.4 System Recovery
4-8
175932-1CD
175932-1CD
EcoTrim ET-1024 System
4.4.3 Brake Release
The robot brakes are designed to protect the robot and other system
components from damage in the event of a system or robot failure, a loss
of drive power, or any other occurrence that activates the brakes. It is then
necessary to release the brakes on the robot in order to move it. To
release the brakes, proceed as follows:
1. On the Programming Pendant, select TEACH mode.
2. Select ROBOT on the Programming Pendant touch screen.
3. Select the BRAKE RELEASE option.
4. Select the control group (R1, R2, S1).
5. While pressing in on the pendant’s ENABLE switch, hold down the
minus key for the axis to be released (S-, L-, U-, etc.). The brake for
the selected axis releases.
WARNING
Always support the robot axis to be released
before
you release it.
Without adequate robot axis support, brake release could cause
personal injury or machine damage.
52 of 64