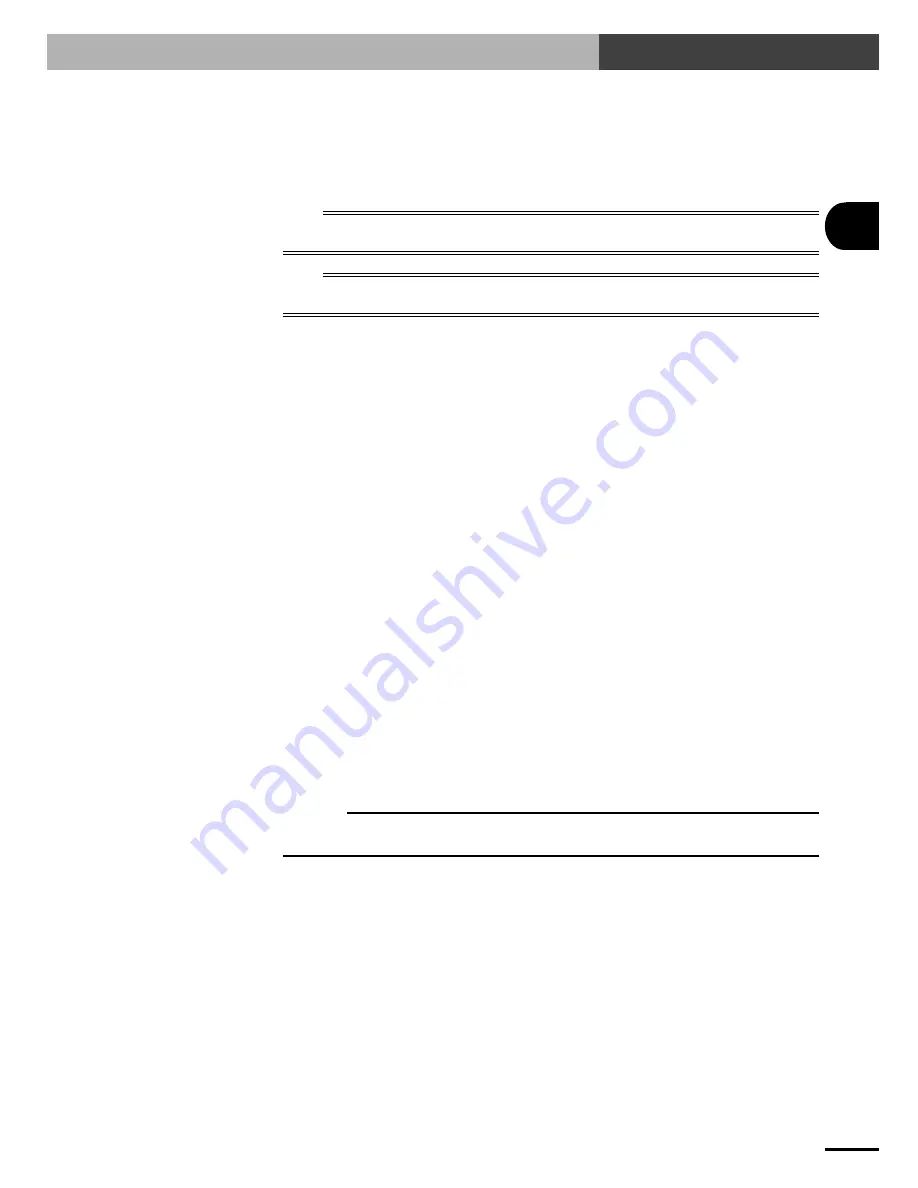
3-
7
3
I/O INTERF
ACE
3-2 Input Signal Description
3-2-3 SERVICE mode input (SVCE)
When the SERVICE mode function is enabled, DI7 functions as the SERVICE mode input (SVCE).
The SERVICE mode input is used to notify the SRCP controller whether the current state is a "SERV-
ICE mode state". This input should be turned off (contact open) in "SERVICE mode state".
Refer to "10-4 SERVICE mode function" for details on the SERVICE mode function.
n
NOTE
Operation stops immediately if the SERVICE mode input status is changed during robot operation while the
SERVICE mode function is enabled.
n
NOTE
Even with the SERVICE mode function enabled, the SERVICE mode input status can be checked in the program as
DI7.
3-2-4 Interlock (LOCK)
This input is used to temporarily stop robot movement.
The robot immediately stops when this input is turned off (contact open) during execution of a dedi-
cated I/O command or during program operation or return-to-origin operation from the TPB (or PC).
(This also interrupts the robot program operation.)
As long as this input is off (contact open), no dedicated I/O commands can be executed, and also no
programs and return-to-origin operation can be performed from the TPB (or PC). The only excep-
tions to this are the reset command and servo recovery command that can be executed regardless of
whether the LOCK signal is on or off. Leave this LOCK signal turned on (contact closed) during
normal operation.
Once this LOCK signal is turned off (contact open), the robot remains stopped even after this input is
turned back on (contact closed), until another command (AUTO-R, ORG-S, etc.) is input.
Changing the PRM34 (System mode selection parameter) setting enables or disables the interlock
function. (See "5-2 Parameter Description".)
3-2-5 Emergency stop inputs 1, 2 (EMG1, EMG2)
Use these inputs to trigger robot emergency stop from an external safety device (for example, safety
enclosure, manual safety switch, etc.). Servo power turns off at the same time when the contact
between EMG1 and EMG2 is open (turned off). Use a relay contact with a current capacity of at least
50mA.
To resume operation, close (turn on) the contact between EMG1 and EMG2, check that the READY
signal is turned on, and then input the servo recovery command (SERVO). The servo will turn on to
enable robot operation.
The TPB or PC can also be used to reset emergency stop when the SRCP controller is connected to
the TPB or PC.
c
CAUTION
Emergency stop inputs 1 and 2 (EMG1 and EMG2) are provided on the EXT. CN connector, and not on the I/O.
CN connector. Do not use the different inputs.
Summary of Contents for SRCP
Page 1: ...User s Manual ENGLISH E YAMAHA SINGLE AXIS ROBOT CONTROLLER E84 Ver 2 04 SRCP ...
Page 2: ......
Page 8: ...vi MEMO ...
Page 18: ...1 10 MEMO ...
Page 28: ...2 10 MEMO ...
Page 132: ...8 34 MEMO ...
Page 146: ...9 14 MEMO ...
Page 176: ...10 30 MEMO ...
Page 218: ...12 10 MEMO ...
Page 235: ...15 1 15 SPECIFICATIONS Chapter 15 SPECIFICATIONS ...
Page 240: ...MEMO 15 6 ...
Page 241: ...16 1 16 APPENDIX Chapter 16 APPENDIX ...
Page 245: ...MEMO ...