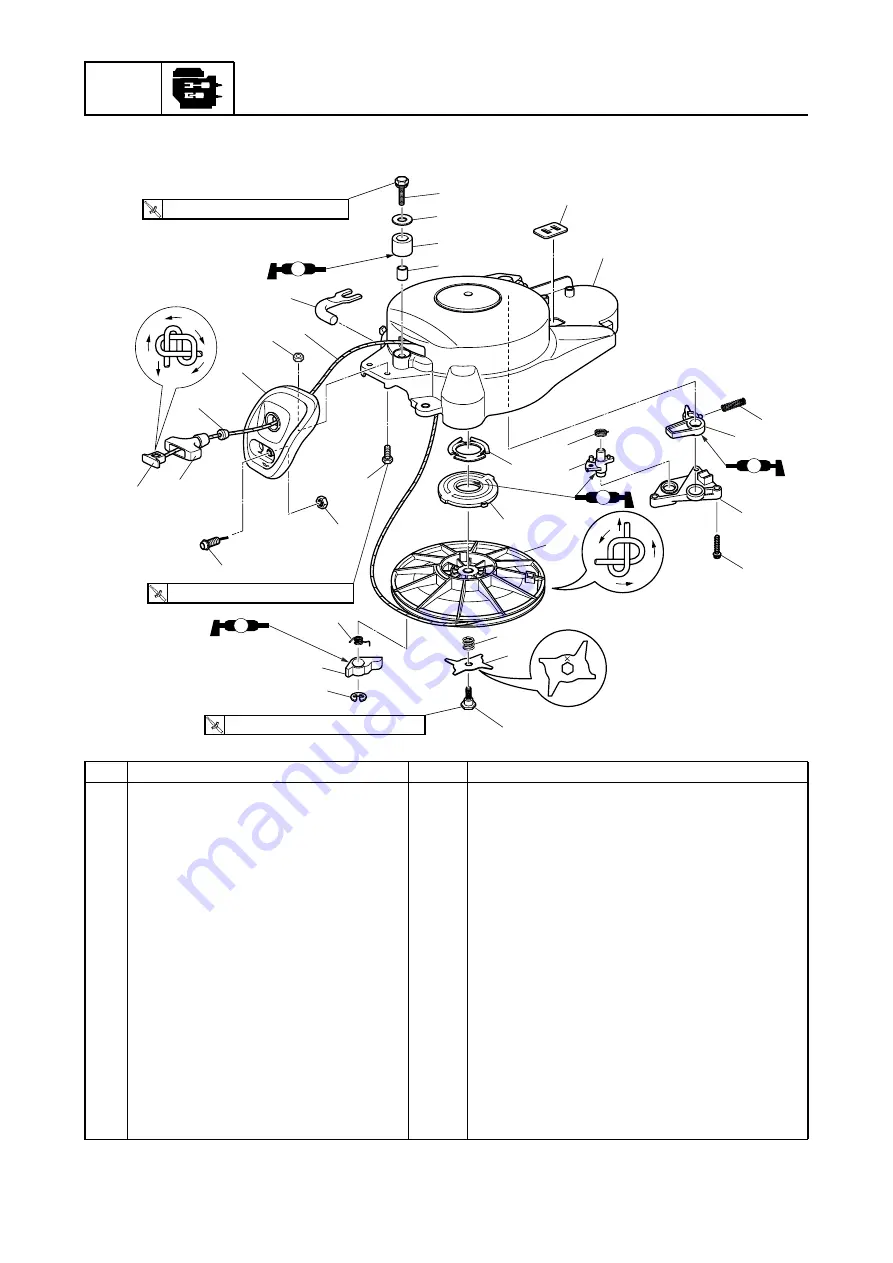
POWR
Power unit
5-11
6D55F11
5
No.
Part name
Q’ty
Remarks
1
Bolt
1
M6
×
30 mm
2
Washer
1
3
Roller
1
4
Collar
1
5
Manual starter case
1
6
Guide
1
7
Starter rope
1
8
Nut
2
9
Starter rope guide
1
10
Damper
1
11
Manual starter handle
1
12
Cover
1
13
Oil pressure warning indicator
1
14
Bolt
2
M6
×
20 mm
15
Spring
2
16
Drive pawl
2
17
Circlip
2
S6D55020
A
A
1
2
3
4
5
7
10
9
12
11
14
13
13
15
16
17
18
19
20
21
22
23
25
24
29
28
27
26
T
R
.
.
8 N
•
m (0.8 kgf
•
m, 5.9 ft
•
Ib)
8
6
30
T
R
.
.
15 N
•
m (1.5 kgf
•
m, 11.1 ft
•
Ib)
T
R
.
.
3 N
•
m (0.3 kgf
•
m, 2.2 ft
•
Ib)
A
A
Summary of Contents for F2.5C
Page 1: ...F25C SERVICE MANUAL 6D5 28197 5F 11 290539 ...
Page 4: ......
Page 16: ...GEN INFO General information 1 11 6D55F11 MEMO ...
Page 27: ...6D55F11 2 10 1 2 3 4 5 6 7 8 9 Clamp bracket Maintenance specification ...
Page 112: ...POWR Power unit 5 51 6D55F11 MEMO ...
Page 136: ...LOWR Lower unit 6 23 6D55F11 Shimming 6 S6D56370 T3 A3 B3 42 5 T1 T2 24 0 24 0 B2 A1 A2 B1 ...
Page 173: ...6D55F11 TRBL SHTG 1 2 3 4 5 6 7 8 9 Troubleshooting Power unit 9 1 ...
Page 183: ......
Page 184: ...YAMAHA MOTOR CO LTD Printed in Japan Nov 2003 0 4 1 CR E Printed on recycled paper ...