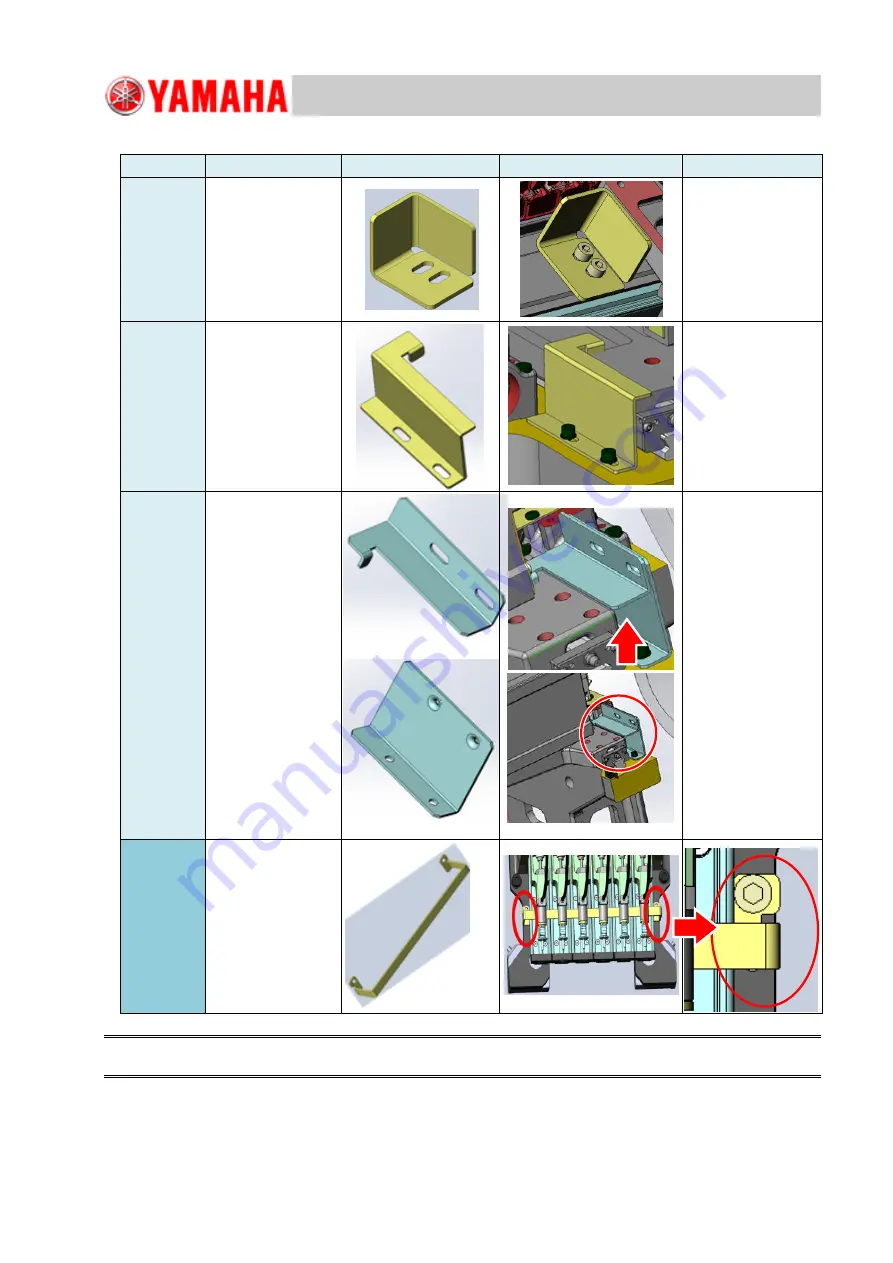
For Service Engineer
Service Information
SI1604009E-002= S20, S10, M20, M10 and D10 installation procedures
10/34
Checklist for the shipping brackets of S20 and S10 for MT6 HEDS
Axis
Qty
Shipping bracket
Status
Remark
X-axis
1 position
LOCK,X-AXIS
LF3-M220W-00
BOLT,HEX,SOKET
HEAD
M5xL8 Qty:2
91312-05008
Y1-axis
1 position
LOCK,Y-AXIS
LE6-M260Y-00
BOLT,HEX,SOKET
HEAD
M5xL10 Qty:2
91312-05010
Y2-axis
1 position
LOCK,Y-AXIS
LF3-M220Y-00
BRKT.LOCK
LF3-M220X-00
BOLT,HEX.SOKET
HEAD
M5xL10 Qty:4
91312-05010
Z-axis
1 position
LOCK,Z-AXIS
LF3-M740Y-00
BOLT,HEX,SOKET
HEAD
M5xL10 Qty:2
91312-05010
Caution:
Keep shipping brackets as they are required for the next shipping.