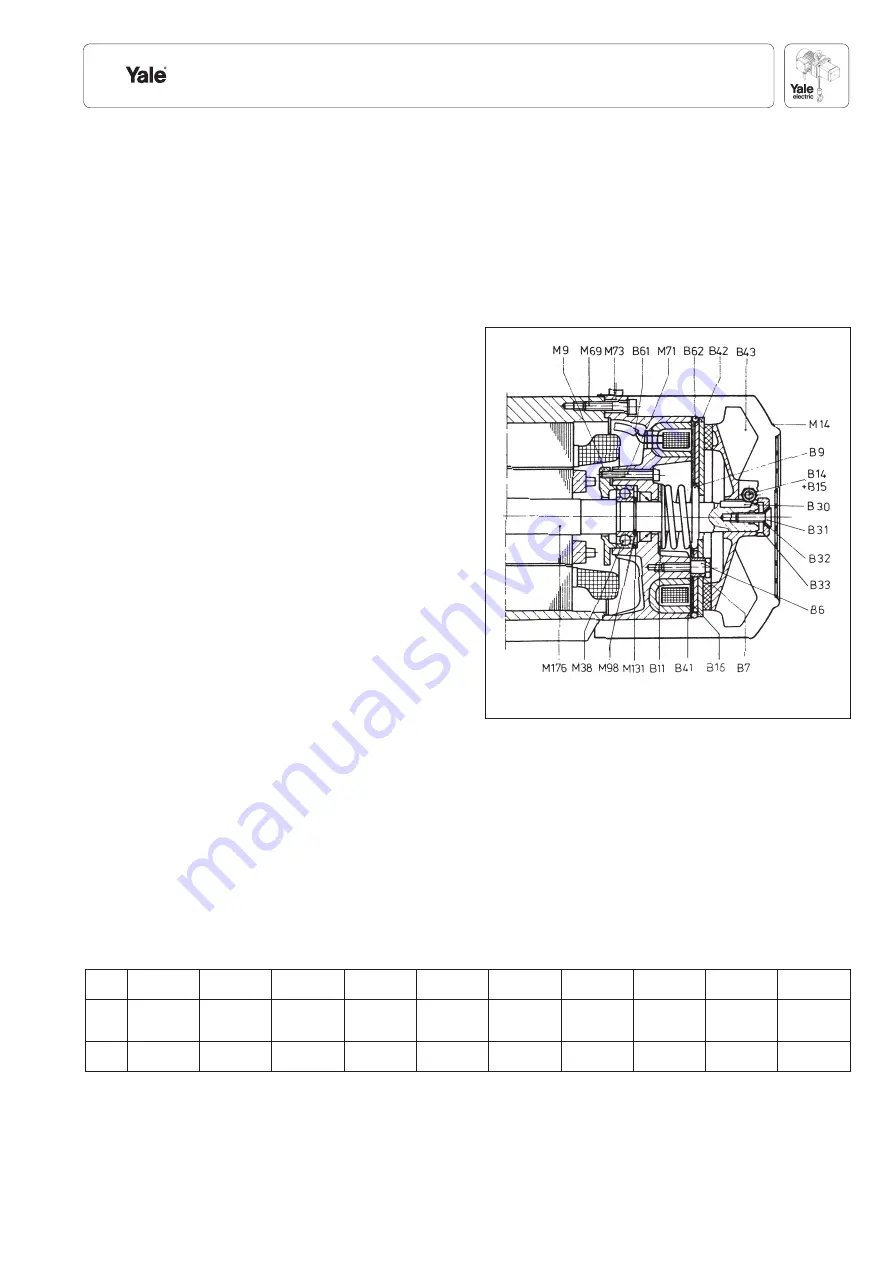
Electric Chain Hoist CPE/F
13
Reassemble the gearbox
Reassemble the gearbox in the reverse order strictly in accordance with
the sectional drawing.
Special care should be taken for clean and correct installation of planet
gears (7) with needle bearings (8) in equal sorting and stop washers (6)
as well as spacer rings (9) in the planet gear carrier (3).
The friction discs (28) on either side of the ring gear (29) must be installed
oil-soaked (leave in oil for 1 hour before installation).
The exact adjustment of the overload device is only possible when the
hoist is completely reassembled. Preadjustment of the cup spring (41)
is made with the fixing screw (42).
After the exact adjustment has been made, the fixing screw (42) is
secured by means of the ball (46) and the threaded pin (47).
The gear box is to be fi lled with approx. 0,3 Litre gearbox oil
(CLP 460, DIN 51547)
Afterwards the fill hole can be closed with the screw plug (44) and the
seal (45).
8.8 MOTOR
Motor
Under normal conditions the motor is practically maintenance-free. Every
2 ½ years the bearings are to be inspected, cleaned and repacked half-full
with grease. We recommend K 3 N / KL 3 N DIN 51825 / DIN 51502.
Disc brake (Fig. 18)
Service to the disc brake is reduced to checking and adjusting the brake
air gap. The disc brake air gap should be between 0,25 and 0,6 mm.
This guarantees a short reaction time and low noise emission.
When the wear and tear of the brake lining comes down to the point where
the max. possible air gap has finally been reached, it is indispensible to
carry out a re-adjustment of the brake:
1. Remove fan guard M14.
2. Loosen binding screws B14.
3. Remove O-ring B62 , insert spacer blocks B40 between armature
disc B42 und adhesive plate B16 (thickness of the spacer blocks is
to be found in the table below).
4. Tighten screws B31, or - in case of two shaft extensions - nut B35
to an extent as to permit the removal of the spacer blocks B40.
5. Evenly tighten the binding screws B14. Please tighten first screw
placed opposite of the fitting key (for the permissible torque consult
the table below).
6. Tighten screw B31 once more.
7. Remove spacer blocks B40.
8. Put on fan guard M14.
9. Make a test run for checking the brake funtion.
Attention: Do not allow the brake friction pads to come into contact
with lubricant or similar!
1
2 3 4 5 6 7 8 9 10
11
Type
Nominal
Fan B 43 with
Spacer block
Air gap
Pressure spring
Tightening
Tightening
Adhesive plate
Threaded pin
Quantity of
brake torque
brake lining
mm
max. mm
B9 colour
torque for B14
torque for B6
B16
B71
fi tting plate B11
EBF
20,2 Nm
WS 5907
0,25 - 0,3
0,6
no colour
7 - 9 Nm
7 + 0,5 Nm
no
M 5 x 80
0
8.9 ELECTRIC CHAIN HOIST IN GENERAL
In particular check following parts:
• Threaded connections in general
Check all nuts, screws and locking devices for tightness.
• Chain container
Ensure the chain container is securely fastened. Check for cracks or
wear.
• Suspension bolt
(Connection between hoist and suspension bracket resp. trolley)
Check for cracks or wear. Ensure all safety devices are in place and
secure.
Fig. 18
Summary of Contents for CPEF
Page 15: ...Electric Chain Hoist CPE F 15...
Page 16: ...Electric Chain Hoist CPE F 16...
Page 17: ...Electric Chain Hoist CPE F 17...