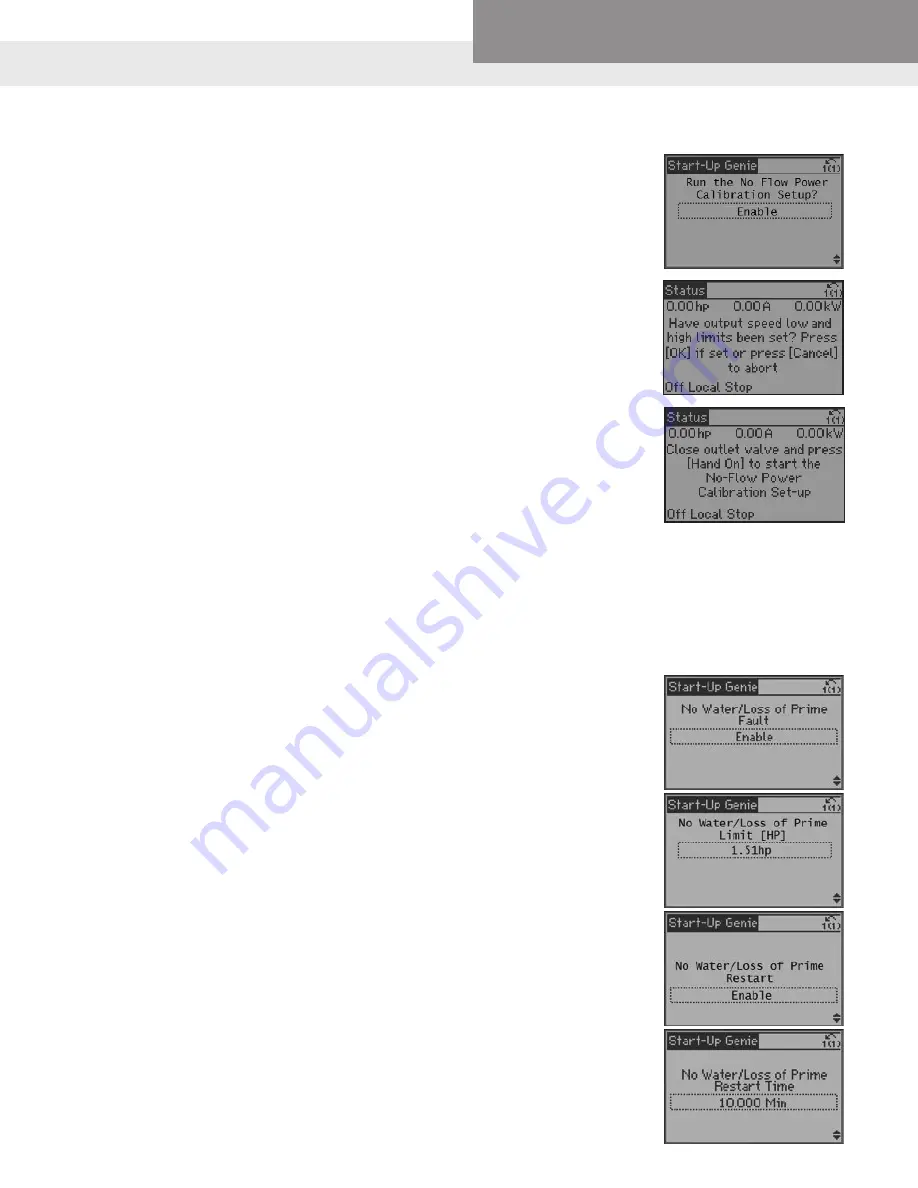
PAGE 13
Aquavar IPC Start-Up Genie
CentriPro
NO FLOW POWER CALIBRATION INSTRUCTIONS
• Select Enable to being the No Flow Power Calibration Setup
• The first screen prompts to ensure the Sleep Frequency/Low Limit and
Motor Frequency have been set. If these points are not set the No Flow Power
Calibration will not operate properly.
• The next screen prompts to close all discharge valves and to press [Hand On] to
begin the No Flow Power Calibration process. Doing this ensures the pump will
operate at no flow/shutoff. If the pump does not operate at no flow during the
setup, the calibration data will be invalid.
• The controller will now begin running the pump while monitoring the power. In the first two steps the pump
is operated at 85% of maximum speed defined at Motor Speed High Limit [Hz] and the power to the pump
is monitored and saved. The pump then operates at 50% of maximum speed and the power is monitored
and saved. The no flow power curve is then constructed within the controller based on these 2 points using
the affinity laws. The No Flow Power Calibration Set-up is now complete. The power data can be saved by
pressing [OK] and then the down arrow. If any issues were encountered during the calibration process
discard the data by pressing [Cancel] and repeat the calibration process.
• No Water/Loss of Prime Fault: No water/loss of prime fault protects the
pump by turning off the pump when a high speed and low power condition is
detected.
• No Water/Loss of Prime Limit: This is the no flow power corresponding to High
Speed. Controller scales this value based on the affinity laws to determine the
no flow power at full speed. Set this value using the No Flow Power Calibration
Setup (previous page).
• No Water/Loss of Prime Restart: No Water/Loss of Prime Restart function
allows the controller to restart after a No Water/Loss of Prime fault is detected.
If No is selected and a No Water/Loss of Prime fault is detected, the drive will
require a manual reset to clear the fault.
• No Water/Loss of Prime Restart Time: The No Water/Loss of Prime Restart
Function allows the controller to restart after a No Water/Loss of Prime fault is
detected. The Restart time is set by the parameter 13-12.3
CHAPTER 6: PUMP PROTECTION
(continued)