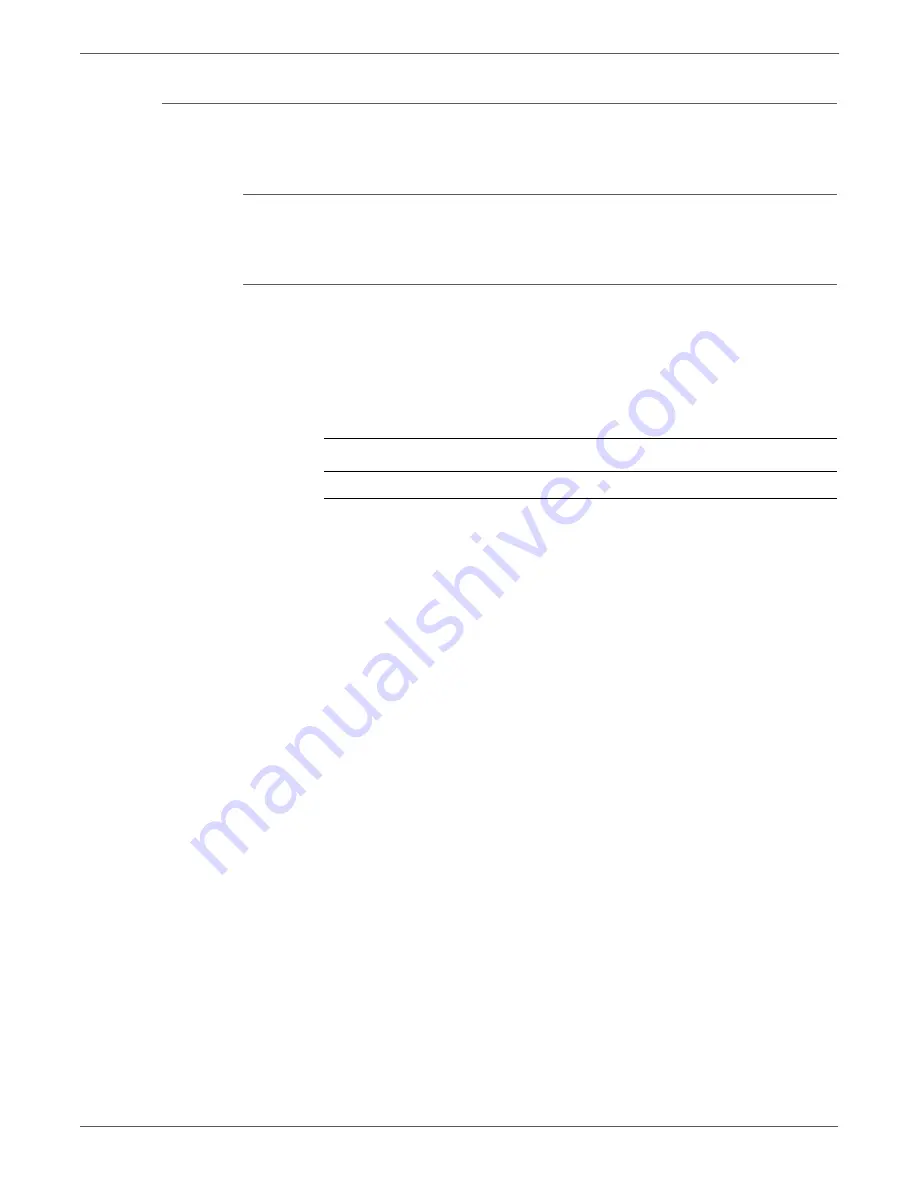
3-94
Phaser 7500 Printer Service Manual
Error Messages and Codes
ATS/ APS No Paper (IOTsc Detect)
The paper specified for printing is not loaded in the Tray.
Applicable Chain-Link Code
•
024-965
: ATS/APS No Paper, APS/ATS NG (No Paper)
Initial Actions
•
Inspect the tray to ensure that it is free of obstructions, is loaded with
supported paper, and the Guides are adjusted correctly.
•
If the problem persists, follow the procedure below.
1. Add paper into the appropriate tray.
2. If the problem persists, refer to the
“General Sensor Failure” on page 3-28
to
check the sensor.
3. If the problem still persists, perform the
“Common System Fail” on page 3-22
Troubleshooting Reference
Applicable Parts
Wiring and Plug/Jack Map References
Summary of Contents for PHASER 7500
Page 1: ...Phaser 7500 Color Printer Phaser 7500 Service Manual Xerox Internal Use Only ...
Page 2: ......
Page 60: ...1 30 Phaser 7500 Printer Service Manual General Information ...
Page 448: ...3 310 Phaser 7500 Printer Service Manual Error Messages and Codes ...
Page 484: ...4 36 Phaser 7500 Printer Service Manual General Troubleshooting ...
Page 544: ...5 60 Phaser 7500 Printer Service Manual Print Quality Troubleshooting ...
Page 545: ...6 Chapter Adjustments and Calibrations In this chapter Adjustments Calibrations ...
Page 554: ...6 10 Phaser 7500 Printer Service Manual Adjustments and Calibrations ...
Page 562: ...7 8 Phaser 7500 Printer Service Manual Cleaning and Maintenance ...
Page 900: ...9 118 Phaser 7500 Printer Service Manual Parts List ...
Page 958: ...10 58 Phaser 7500 Printer Service Manual Plug Jack and Wiring Diagrams ...
Page 980: ...11 22 Phaser 7500 Printer Service Manual Reference ...
Page 990: ...I 10 Phaser 7500 Printer Service Manual Index ...
Page 991: ......