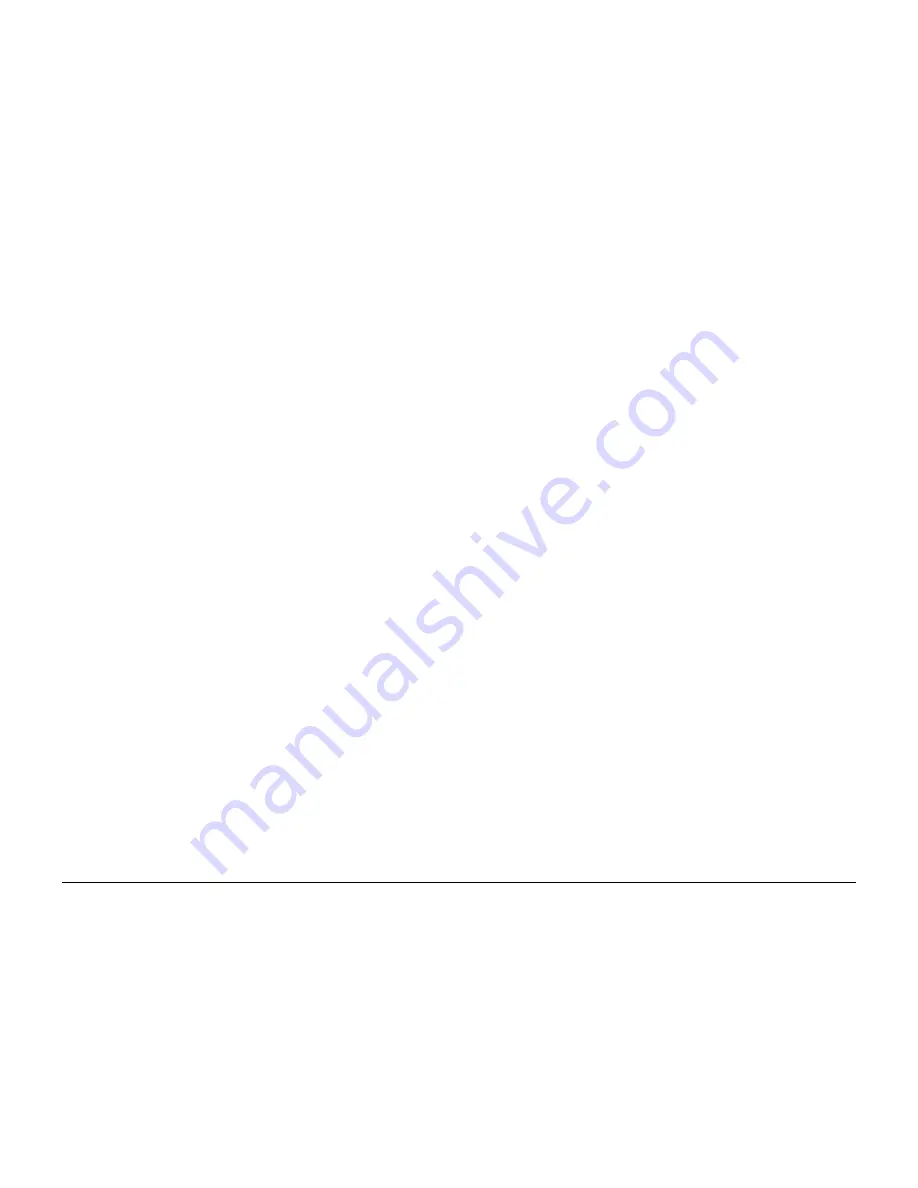
5/2011
2-74
Phaser 4600/4620 Printer Service Manual
17-900-00, 17-910-00
Revision - Xerox Internal Use Only
Status Indicator RAPS
17-900-00 802.1X Authentication Error RAP
17-200-00 802.1X Authentication failed.
Initial Actions
•
Close the Rear Door.
•
Check for obstructions blocking the latch.
Procedure
Ensure that the 802.1X EAP type, user name and password for the machine authentication
switch and authentication server match.
17-910-00 Firmware Upgrade Fault RAP
17-910-00 Upgrade aborted invalid file.
Initial Actions
•
Download a new firmware file.
•
Check the USB connection
Procedure
Cycle system power and repeat the upgrade procedure.