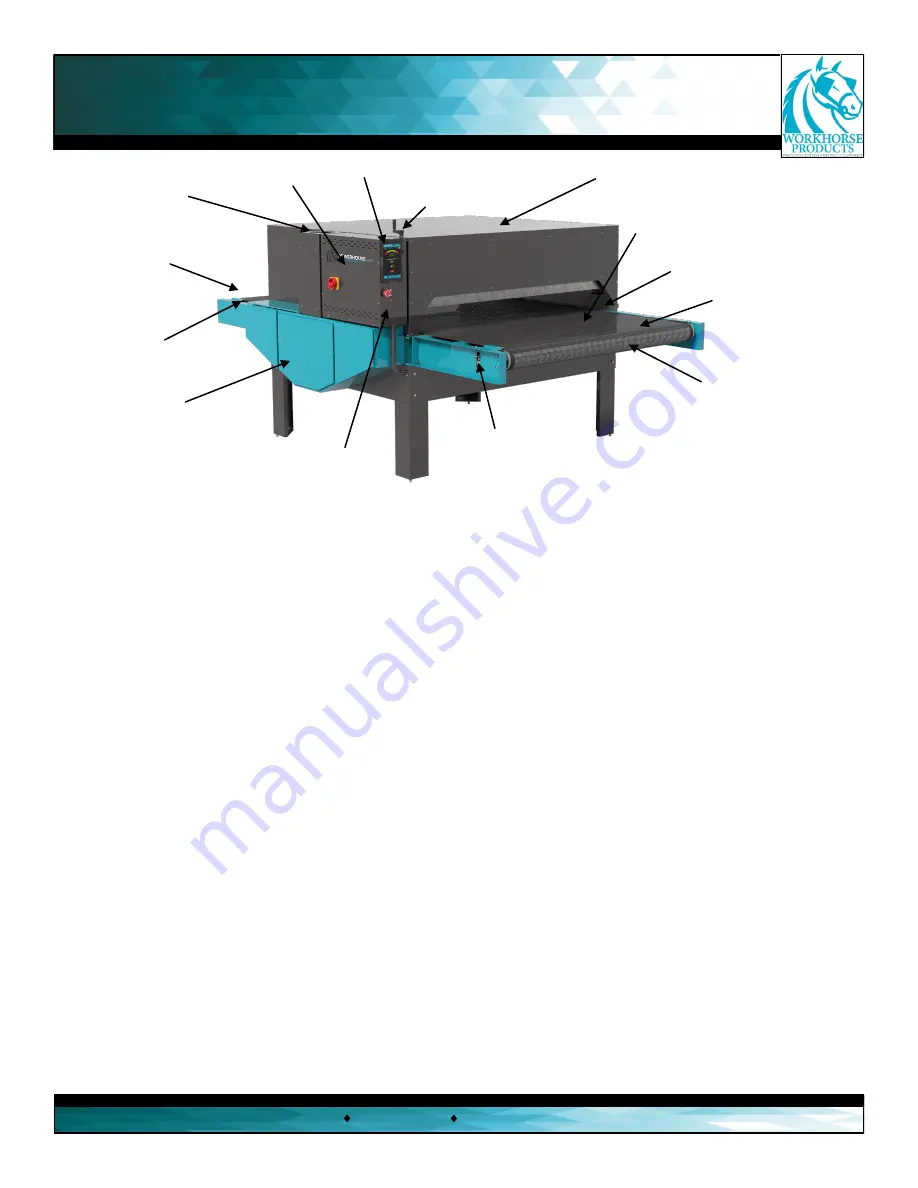
Assembly of Dryer
3730 E. Southern Avenue, Phoenix, AZ 85040 USA
800-778-8779
Workhorseproducts.com
4
Infeed
Outfeed
Conveyor Belt
Front Pulley
Rear Pulley
Belt Tracking
Adjust
Exhaust
Convection System
Panel Heating Elements
Control Box
Underneath the top panel there are three infrared radiant panel heating elements that are controlled by the tablet
controller. They can cure plastisol, water-based ink, and any evaporative cured ink. They are capable of heating up
and cooling down within seconds.
Most of the machine’s electrical components are located within the control box. This box is easily accessible for any
necessary maintenance.
Used to raise and lower the heating elements to adjust heat distance to the garment. To raise the element turn the
crank handle clockwise. Turn the crank handle counterclockwise to lower the element.
The exhaust is used to release heat. Use the push pin handle next to the exhaust to control the amount of heat re-
leased.
Filters the incoming air and needs to be cleaned whenever it becomes filled.
The conveyor belt is created of Teflon coated fiber glass and is placed on a self-aligning belt tracking system. The
belt is designed to withstand heat, but be sure the belt is always moving when the Powerhouse II is operating
above 300 degrees.
Used for tracking the belt and keeping the belt on the pulley. If the belt moves to the side, use the belt tracking
adjust to center it.
The pulleys are created for precise rolling at an even center.
The tablet controller is the main control system for the Powerhouse Series II. The tablet programs the temperature,
belt speed, warm up, cool down, power consumption, create presets, access the owner’s portal, and contacts
Workhorse technical support if ever needed.
A precisely designed air system to utilize and release heat within the dryer.
Where the garments are placed to start the curing process.
Where the garments exit the curing process. They land on a cool down table and eventually run off the belt.
Crank Handle
Filtered Intake
Tablet Controller
Panel Heating
Elements
Control Box
Crank Handle
Exhaust
Filtered Intake
Conveyor Belt
Belt Tracking
Adjust
Pulley
Tablet
Controller
Convection
System
Infeed
Outfeed
E-Stop