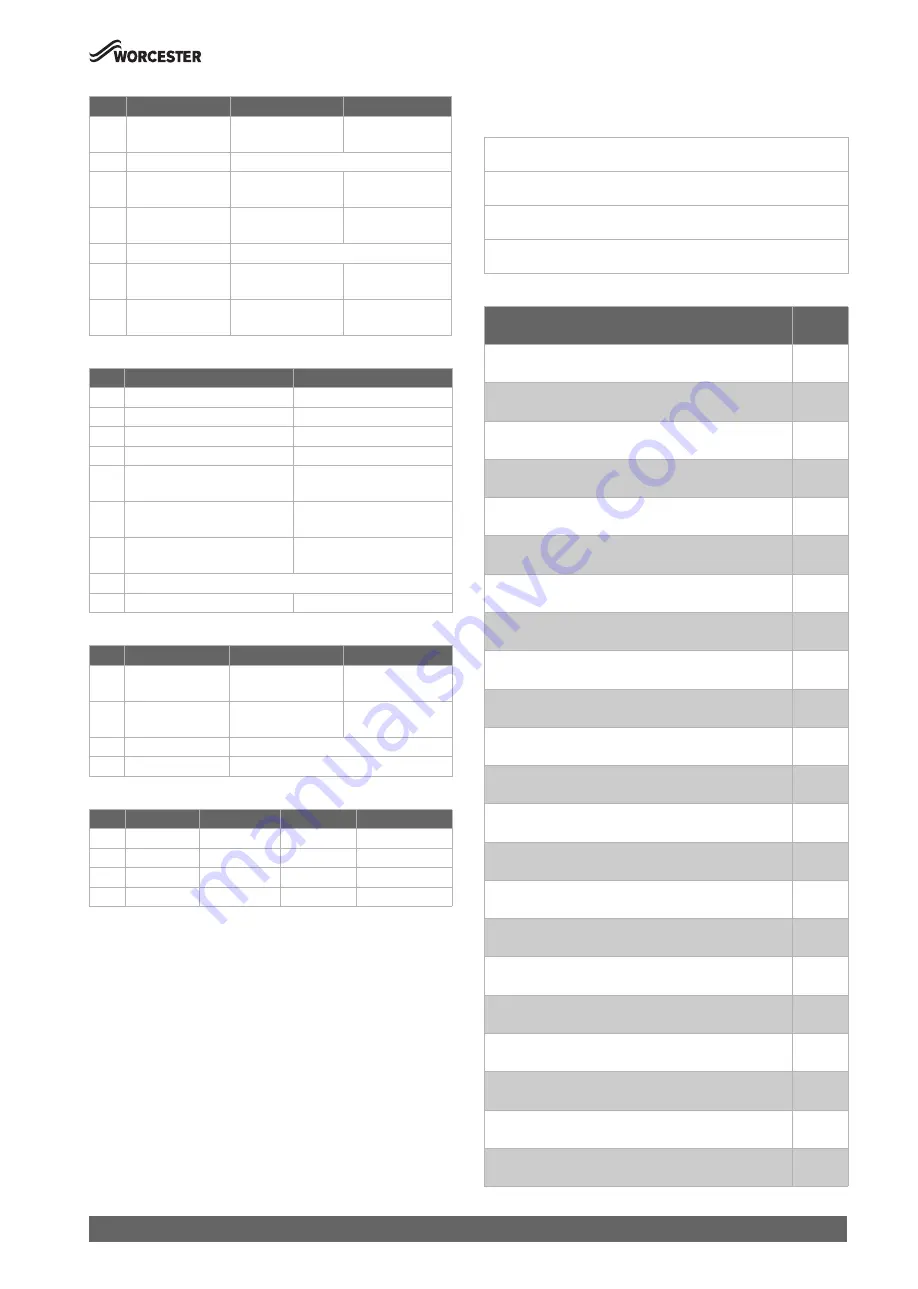
Commissioning
17
Greenstar – 6721852556 (2022/11)
Table 16 Loop 2 - Effective date
Table 17 Loop 3- Information loop
Table 18 Loop 4- Pulse loop
Table 19 Loop 6- Month loop
7.6
Commissioning checklist
▶ Complete and sign checklist following assembly and commissioning.
Table 20 General information on the system
Window 1
Window 2
Window 3
2.1
Accounting date 1
Date
Accounting date 1
Energy kWh
Accd 1 A
2.2
Accd. 1
Date of future accounting date 1
2.3
Accounting date 1
previous year date
Accounting date 1
previous year energy
Accd 1L
2.4
Accounting date 2
date
Accounting date 2
energy
Accd 2A
2.5
Accd 2
Future accounting date
2.6
Accounting date 2
previous year date
Accounting date 2
previous year energy
Accd 2L
2.7
Accounting date 1 Pulse input 1
Volume pulse input
1
Window 1
Window 2
3.1
Current date
Current time
3.2
Sec_Adr
Secondary address
3.3
Pri_Adr 1
Primary address 1
3.4
Pri_Adr 2
Primary address 2
3.5
Installation position (cold pipe/
return pipe as standard)
(depending on the setting)
3.6
Port 1
0 (no. of installed module in
port 1)
3.7
Port 2
1 (no. of installed module in
port 2)
3.8
Status of the integrated radio
3.9
Software version
Check sum
Window 1
Window 2
Window3
4.1
Pulse input 1
Cumulative value
pulse input 1
Value of pulse (L/P)
4.2
Pulse input 2
Cumulative value
pulse input 2
Value of pulse (L/P)
4.3
Pulse output 1
Value of pulse (L/P)
4.4
Pulse output 2
Value of pulse (L/P)
Window 1
Window 2
Window 3
Window 4
6.1
“LOG”
Date-1
Energy
Max. flow rate
6.2
“LOG”
Date-2
Energy
Max. flow rate
....
6.24
“LOG”
Date-24
Energy
Max. flow rate
User:
System location:
Installer:
Heat interface unit type:
Commissioning checklist
Mains power supply compliant with standards?
1. System hydraulics / primary circuit
Heating flushed, filled and checked for leaks?
Vented the system?
Differential pressure and volumetric flow rate of the central
primary pump checked?
If fitted, has the flushing valve been closed?
q
Operating pressure in primary circuit measured?
_____ bar
Central pressure-relief valve installed?
Strainer checked and cleaned?
2. Heating / tertiary circuit
Heating system flushed, cleaned and vented?
Has power been left switched on to ensure the pump anti
seize function can operate?
Have radiator flow rates been balanced?
Heating circuit with mixer: position of rotary selector?
_________
Underfloor heating system: overheating protection
installed?
Setting of heating circuit pump checked?
Does lowering the room thermostat remove the demand for
HTG?
Heating flow temperature (at HIU) measured?
______ °C
Heating return temperature (at HIU) measured?
______ °C
Have TRV's been mounted horizontally on radiators?
q
Record the return temperature limiter set point (default 50)
if adjusted?
______ °C
Primary circuit flow temperature measured?
______ °C