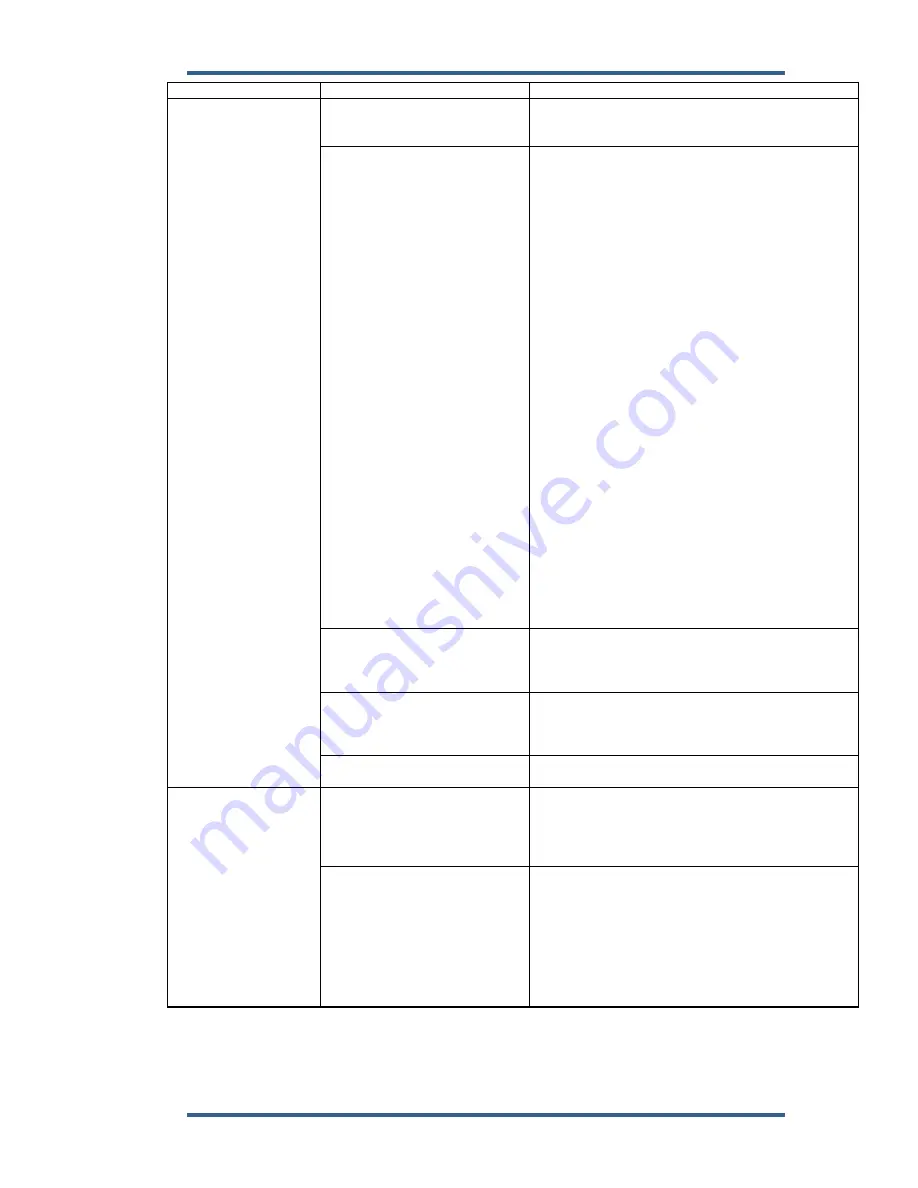
Manual 04121
ProAct I/II
Woodward
55
Problem Cause
Remedy
Prime mover will not
stabilize at rated no-
load speed. The
instability may occur
at no load or it may
vary with load. Control
may be erratic.
ProAct control.
Adjust GAIN, Stability, and ACTUATOR
COMPENSATION in Menu 1 or 2. Check Gain
Breakpoint for the lower speeds.
Necessary external wires not
properly shielded. (Electrical
noise, caused by wiring carrying
an ac voltage, stray magnetic
fields from transformers, etc.,
can be picked up by improperly
shielded wire. Noise will cause
instability if picked up by
magnetic pickup, position
feedback, auxiliary input, or
remote reference lines.)
The following tests will isolate noise and
interference.
Verify that the switchgear frame, governor chassis,
and prime mover have a common ground
connection. Temporarily remove the battery-charger
cables from the control battery system.
If the prime-mover operation is significantly
improved by these modifications, replace the wires
one at a time to locate the source of the trouble.
External wiring may require additional shielding or
rerouting from high-current lines or components.
If the problem cannot be solved by these checks, it
will be necessary to remove the control from the
switchgear. Temporarily mount the control next to
the prime mover and connect only a battery,
magnetic pickup, and actuator to the control (use a
separate battery placed next to the prime mover).
After starting the prime mover, if necessary, apply
load to check stability.
If stability occurs when the control is mounted next
to the prime mover, return the control to the
switchgear. Run new magnetic pickup, actuator
feedback, and battery power lines. Shield all wires
to the control. Route all wires through conduit or an
outer shield. Tie the outer shield to system ground
at the end opposite to the control.
Prime mover may not be
receiving fuel as called for by
the actuator voltage.
Check actuator linkage to fuel-controlling
mechanism for any lost motion, binding, or
excessive loading. Verify a steady fuel pressure of
proper value.
Prime mover not operating
properly.
Prime mover may be causing speed variations.
Control engine manually to determine if instability is
in prime mover or governor control. Verify proper
adjustment of fuel control linkage.
Input voltage low.
Check supply voltage. It should be at least 18 Vdc,
not more than 32 Vdc.
Prime mover will not
accept full load.
Prime mover.
If droop occurs near the full-load point only, it is
possible the prime mover is not producing the
power called for by the fuel control, or is being
overloaded. Either is indicated if the fuel control is at
maximum position.
ProAct control.
Check Max Fuel Limit setting. Increase if required.
Check Torque Limiter settings. Increase if required.
Check droop setting. Set to 0 if required.
Check Aux Input terminals to see if the auxiliaries
are out of range. Maximum voltage is 2.5 Vdc.
Check linkage from actuator to fuel rack.
Summary of Contents for ProAct I
Page 10: ...ProAct I II Manual 04121 8 Woodward Figure 1 3 Example of ProAct II Actuator...
Page 11: ...Manual 04121 ProAct I II Woodward 9 Figure 1 4 Outline Drawing of ProAct I or II Actuator...
Page 12: ...ProAct I II Manual 04121 10 Woodward Figure 1 5 ProAct Wiring Diagram...
Page 13: ...Manual 04121 ProAct I II Woodward 11 Figure 1 6 Outline Drawing of ProAct Control Box...
Page 39: ...Manual 04121 ProAct I II Woodward 37 Figure 4 2 Typical Transient Response Curves...