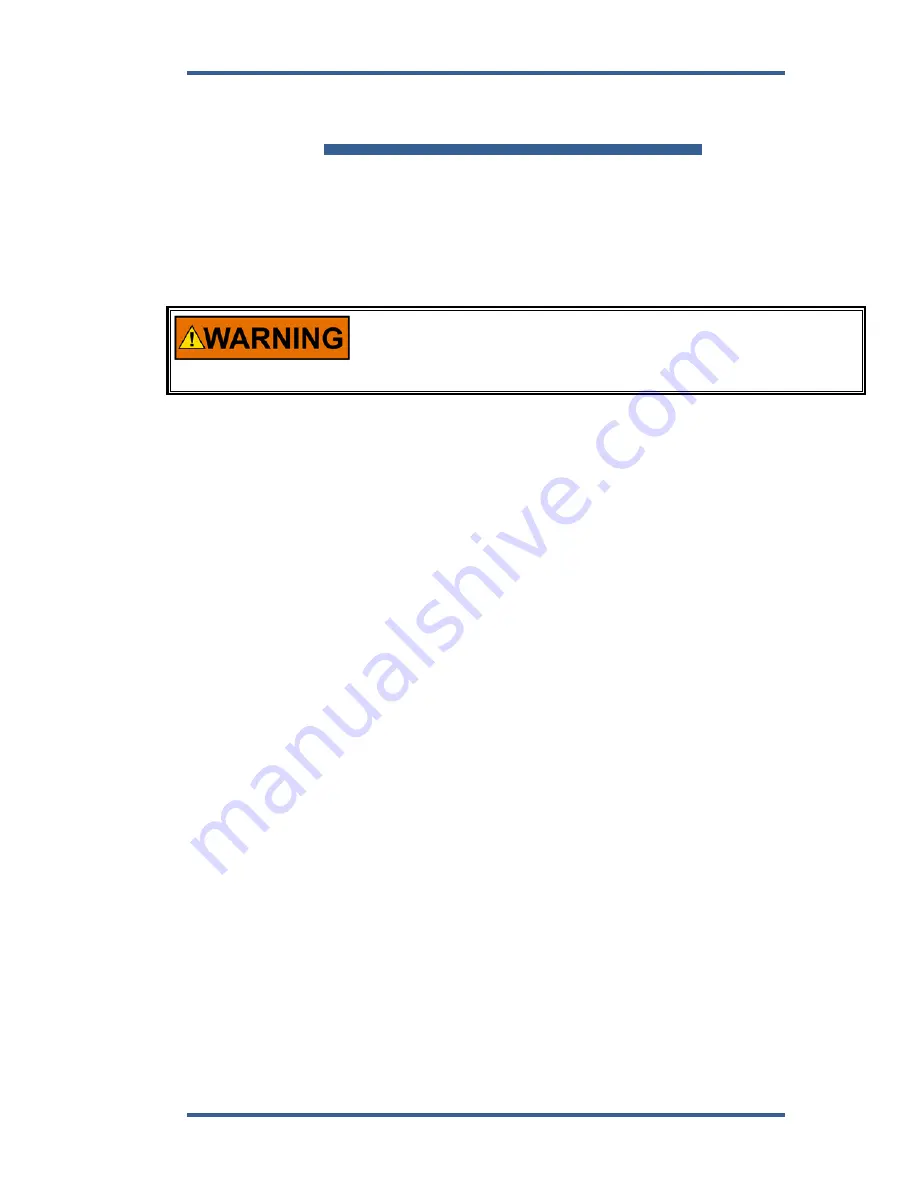
Manual 04121
ProAct I/II
Woodward
31
Chapter 4.
Operation and Adjustment
Introduction
Because of the variety of installations, plus system and component tolerances,
the control must be tuned to each system for optimum performance.
This chapter contains information on control calibration. It includes initial
prestart-up and start-up settings and adjustments.
An improperly calibrated control could cause an engine overspeed or
other damage to the engine. To prevent possible serious injury from
an overspeeding engine, read this entire procedure before starting
the engine.
Using the Hand Held Programmer
The Hand Held Programmer (Figure 4-1) is a hand-held terminal, powered by the
ProAct™ Digital Speed Control. The terminal connects to the RS-422 D
connector port on the control. Firmly seat the connector on the terminal into J1.
Control boxes are equipped with a cover which must be removed to access the
J1 receptacle and the two other terminal strips.
When power is applied to the terminal by plugging it into the control, it performs a
power-up self-test. Upon successful completion of the self-test, the screen will
remain blank. Press the ID key to display the part number and revision level of
the software in the control. Refer to this number and revision level in any
correspondence with Woodward.
The programmer screen is a four line, back-lighted LCD display. The display
permits the user to look at two separate functions or menu items at the same
time. Use the “up/down arrow” key to toggle between the two displayed items.
The first letter of the active menu will blink.
Changes recorded in the menus may be lost should the ProAct control be
powered down. Push the SAVE key to permanently record changes before
leaving a menu.
Summary of Contents for ProAct I
Page 10: ...ProAct I II Manual 04121 8 Woodward Figure 1 3 Example of ProAct II Actuator...
Page 11: ...Manual 04121 ProAct I II Woodward 9 Figure 1 4 Outline Drawing of ProAct I or II Actuator...
Page 12: ...ProAct I II Manual 04121 10 Woodward Figure 1 5 ProAct Wiring Diagram...
Page 13: ...Manual 04121 ProAct I II Woodward 11 Figure 1 6 Outline Drawing of ProAct Control Box...
Page 39: ...Manual 04121 ProAct I II Woodward 37 Figure 4 2 Typical Transient Response Curves...