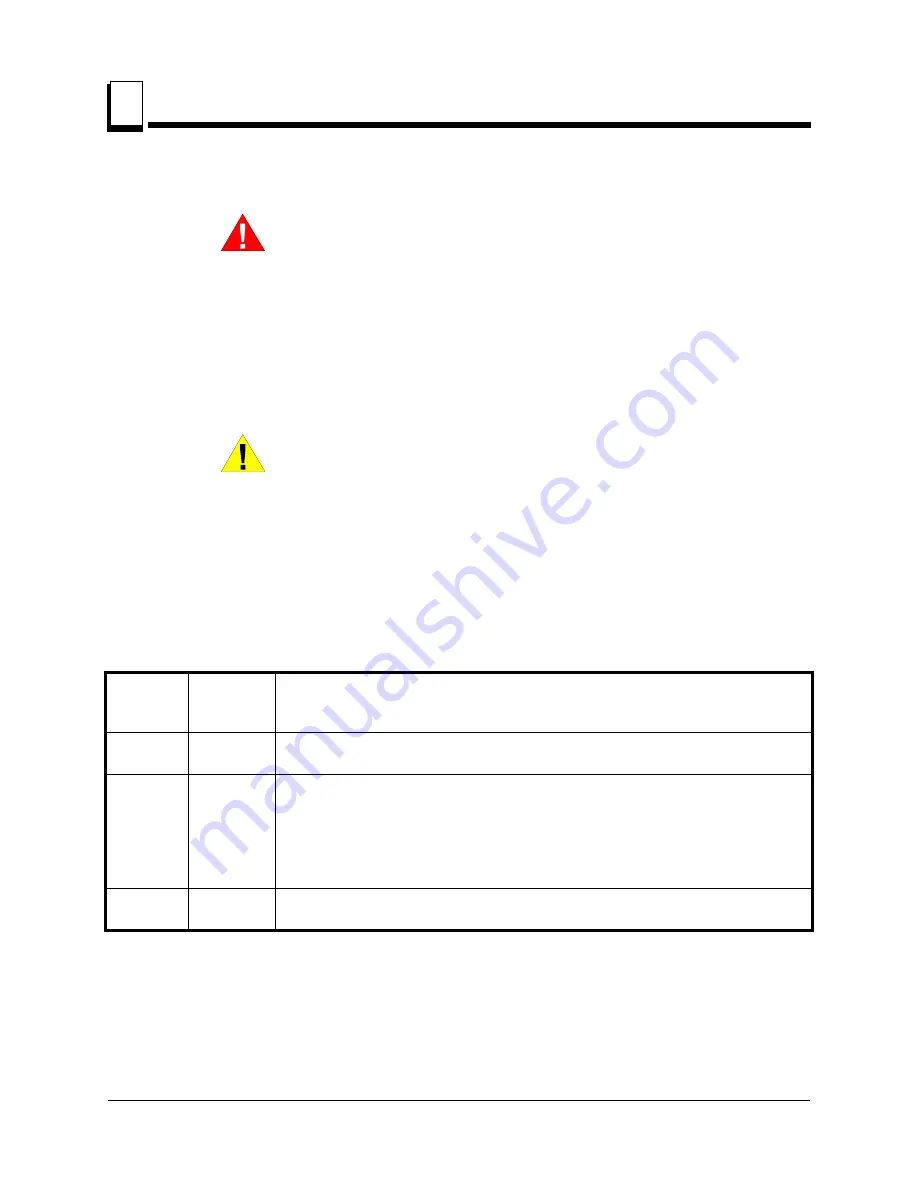
Debarker Installation
2
2-1
MKI96DB98doc011711
Debarker Installation
SECTION 2 DEBARKER INSTALLATION
DANGER!
On electric mills, hazardous voltage inside the
disconnect box, starter box, and at the electric motor can
cause shock, burns, or death. Disconnect and lock out
power supply before performing debarker installation! Fol-
low all applicable electrical codes.
DANGER!
Before performing any service to this equip-
ment, turn the key to the OFF (0) position, remove the key,
and disconnect the sawmill battery ground terminal. Failure
to do so will result in serious injury or death.
CAUTION!
Due to various design changes and past retro-
fits and options, you should very carefully look your mill
over to determine Debarker compatibility before beginning
Debarker installation.
The Debarker Option may be installed to most sawmills with the required up/down chains
and 60 amp or larger alternator systems.
See Table 2-1.
Look at your sawmill up/down chains to verify they are the proper style
for use with the Debarker Option. Refer to the chart below to determine if the Debarker
Option may be installed on your specific sawmill.
Up/Down
Chain
Type
Install
Debarker?
Comments
Single
#40
No
The Debarker Option can only be installed on sawmills equipped with dual
up/down chains (after 7/86).
Dual #40
Yes, if USA
chain. See
comments.
"USA" should be stamped into the side plates of the chain. If it is not, you will
need to replace the existing chains with the proper specified chains. If you did
not receive replacement chains with your Debarker order and find that you need
them, call Wood-Mizer Customer Service at
1-800-525-8100
.
Do not proceed
with Debarker installation or further operation until your mill is equipped
with the correct up/down chains.
#50-2
Yes
The Debarker Option can be installed on any sawmill equipped with #50-2
up/down chain (after 3/97).
TABLE 2-1