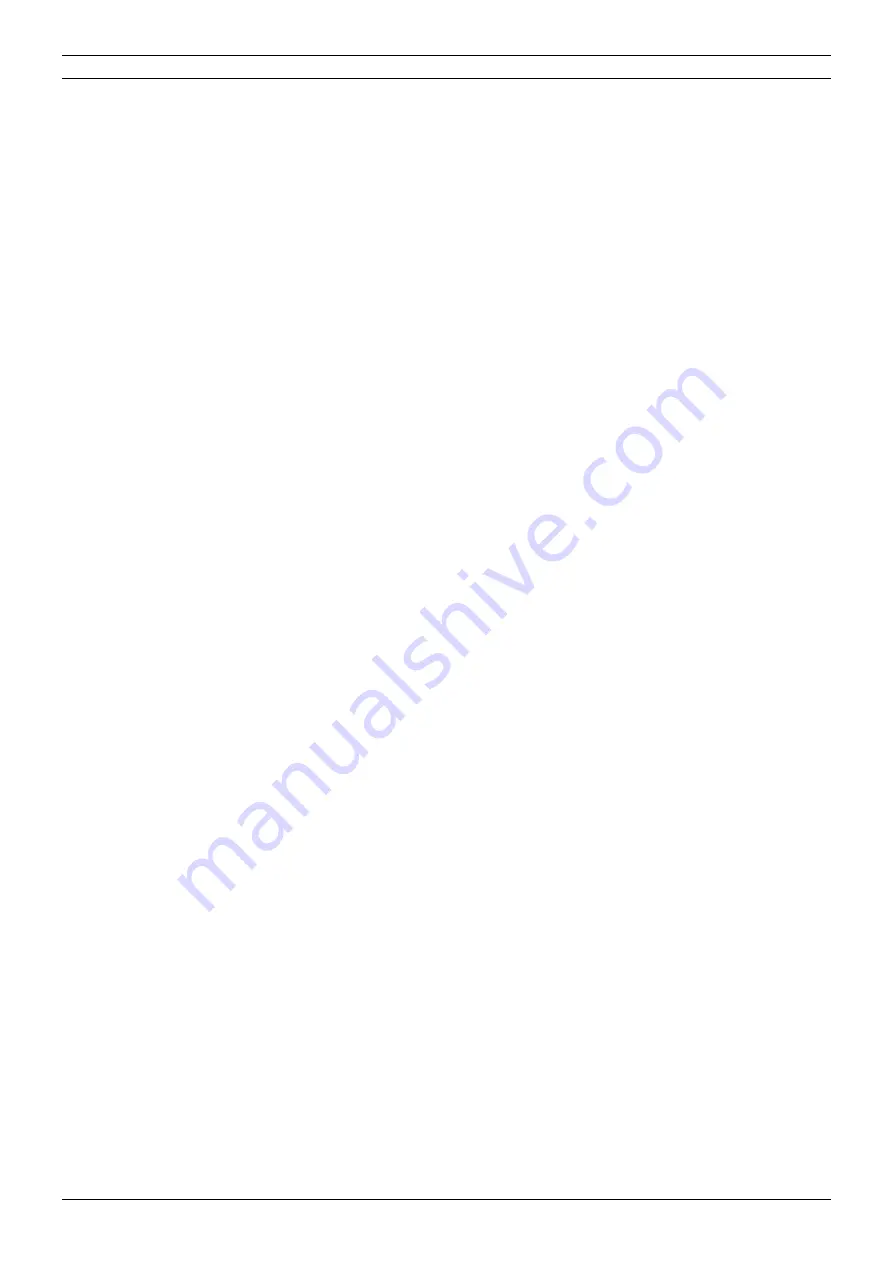
Bedienungsanleitung Steuerung S4_2006_09_25-neu.doc
Page 81 / 83
© wodtke GmbH Tübingen. All rights reserved. Subject to change without notice.
Month of issue xx/200x
Art. no. 950 281
15 Warranty and Guarantee
As of 1/1/2002 (delivery date) all wodtke products and components are subject to the new EU-
harmonised warranty periods. Products are sold through local craft enterprises only. For virgin
products the final customer’s warranty period in relation to the seller is 24 months. Damage
attributable to normal wear and tear is not covered by the warranty, since this bears no relation
to any product defect (similarly to car tyres, brake pads, spark plugs, filters etc.). Nor are the
performance of lubricants or fuel (similarly to petrol, engine oil etc.) or errors attributable to
improper use, installation, operation, use, care, servicing etc. covered by the warranty.
Independently of any legal regulations concerning the seller warranty wodtke gives a six-month
factory guarantee for all wearing parts.
Wearing parts in pellet stove technology and accessories include in particular:
fire-exposed inside components of the firebox such as chamotte, insulation, sealings, sheet
metal or cast metal plates, burner pots, grates, viewing window glass, ignition elements.
Not included in either the warranty or guarantee are in particular all damage attributable to
excessive chemical or thermal stress, overvoltage, faults attributable to operating errors or
improper installation, handling, use, cleaning, servicing or operation. Perforation of water heat
exchangers through rust as a result of oxygen diffusion, operation below dew point or exposure
to chlorinated hydrocarbons or other metal corroding substances or gases originating from the
environment or fuel likewise constitute faults attributable to improper operation and are
therefore excluded from the warranty and guarantee. The same applies to the use of
unapproved fuels or any kind of improper or unqualified work performed on the appliance.
All components (including glass components) of wodtke products have been tested by neutral
testing institutions as well as at the production plant’s outgoing inspection. These tests include
involved quality and approval tests for design which relate to normal operating conditions and
are based on stringent quality criteria. If errors should nevertheless occur, please immediately
make your complaint to your local dealer stating the purchase date as well as the serial number
of your appliance. Please appreciate that we are unable to process complaints properly unless
we have the serial number of the appliance in question.
By adhering to the proper use, operation, care and maintenance of our products you will
enhance their value stability and service life, help to conserve valuable resources and go easy
on the environment as well as your purse.