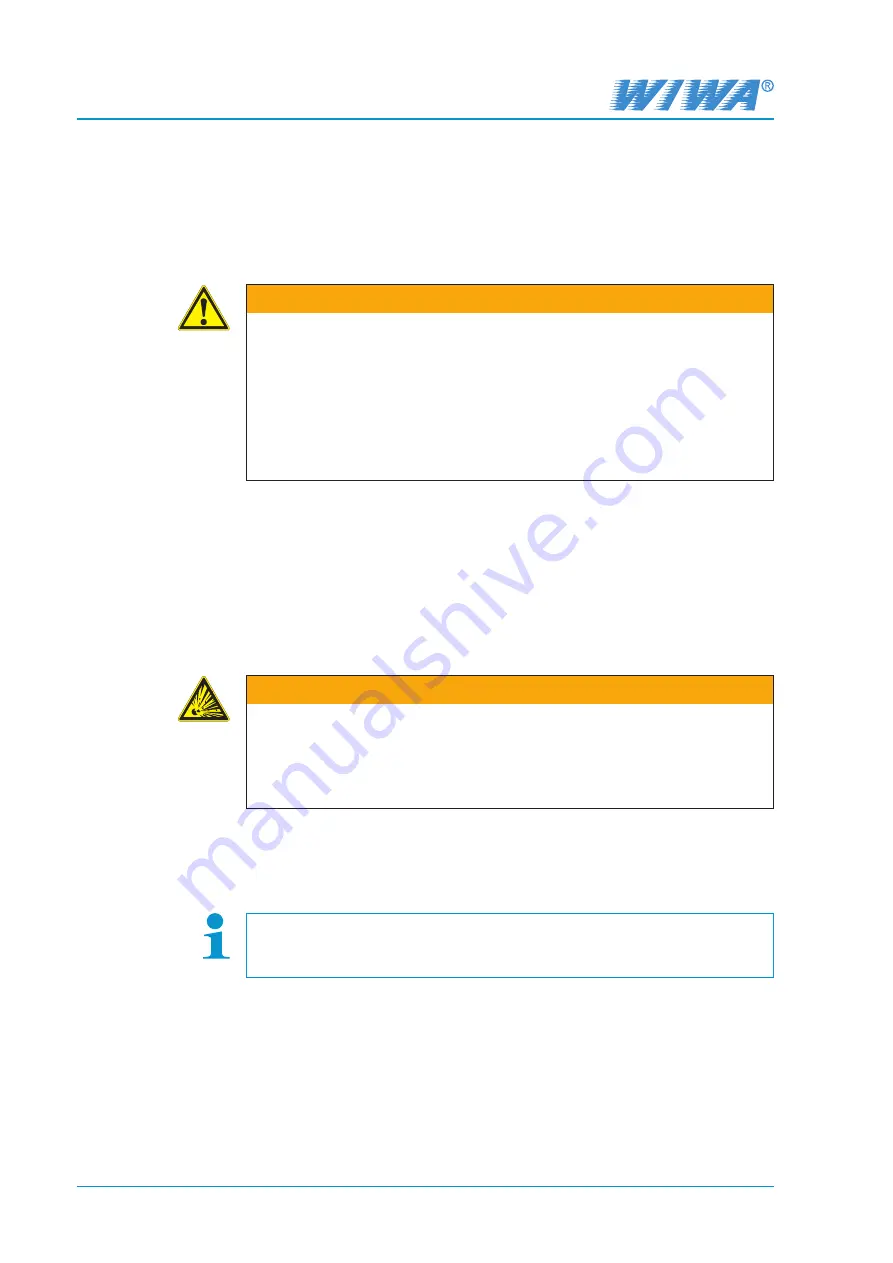
34
Translation of the original operating instructions
DUO
MIX
270
DM270_BAoDB_en_1507 • rs
Operation
5.4 Pressure relief
1.
Close the compressed air shut-off valve on the maintenance unit.
2.
Set the levers at the mixing unit to "Circulation".
3.
Trigger the spray gun, until the material pressure has been fully relieved.
WARNING
If parts of the equipment (e.g. spray nozzle, material filter on the spray gun,
material hose, high pressure filter, suction strainer, etc.) are clogged the
pressure cannot be fully released. Residual pressure could be released
during disassembly work and cause severe injuries.
➤
Cover the screw fitting with a rag during releasing to protect yourself
against sudden release of material.
➤
Release the screw fittings very carefully and release the pressure slowly.
➤
Remove the obstructions (see fault table in Chapter 7 on page 43).
5.5 Complete cleaning
Cleaning the machine completely is necessary:
➤
At initial commissioning to ensure that the spraying material is not negative-
ly affected by the test medium that was used at the factory to test correct
functioning.
➤
When changing materials.
➤
If you want to decommission the machine for a longer period of time.
WARNING
Explosive gases may be generated by the evaporation of flushing agent,
which may ignite on hot heat sources.
➤
Before you start cleaning work you must switch off all fluid heaters and
allow the machine to cool down. Quicker cooling can be achieved by
circulating the material through the machine (max. 20 minutes).
1.
Flush the machine as described in chapter 5.3, in order to clean the section
between mixing unit and spray gun.
Perform the following work steps to clean the section between material inlet
and mixing unit.
Both components must be strictly kept separated, also during cleaning.
Use a separate solvent and collecting container for each component to avoid
material reactions and thus possible damage to the machine.
2.
Drain the material off the feed tanks through the drain valves, then fill in the
flushing agent belonging to the material.
3.
Guide the return flow hoses into separate collecting vessels and secure
them against accidental slipping out.
4.
Set the levers at the mixing unit to "Circulation".
5.
Regulate the air pressure regulator of the proportioning pump so that the
proportioning pump runs slowly.