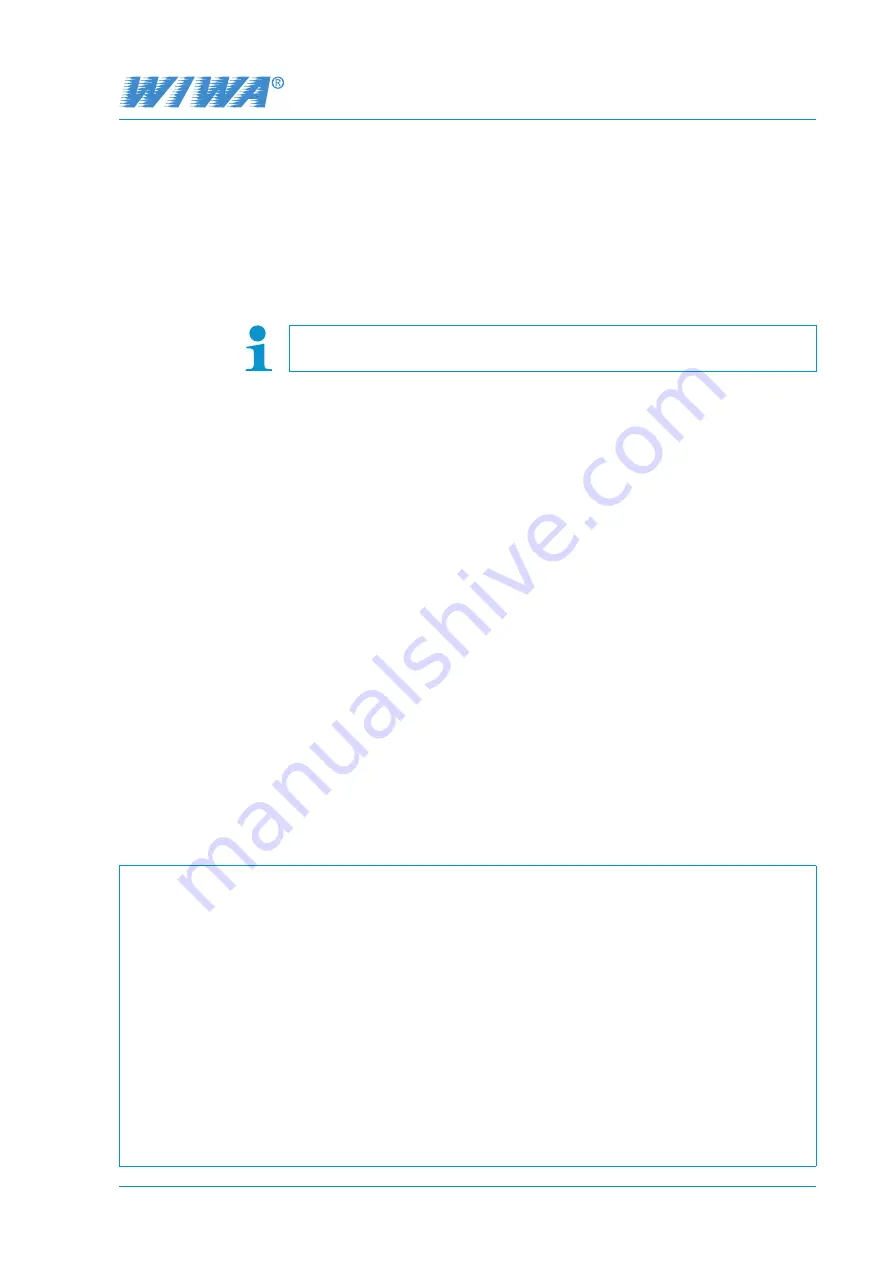
Translation of the original operation manual
DUOMIX 230
5
DM230_BAoDB_en_1307 · rs
Foreword
1 Foreword
Dear Customer!
We are delighted that you have decided in favour of a
DUOMIX 230
from our
company.
This operating manual is intended for the operating and maintenance person-
nel. It contains all the information required to working with this unit.
The owner of the unit must ensure that the operator of the unit always has
an operating manual at his/her disposal in a language he/she understands!
Safe and reliable operation of the unit requires further information in addition
to this operating manual. Read and comply with the applicable guidelines and
accident prevention instructions for your country.
In Germany, these are:
➤
the “Richtlinien für Flüssigkeitsstrahler (Spritzgeräte)” (Guidelines for
Liquid Jets), issued by the Hauptverband der Gewerblichen Berufsge-
nossenschaften.
➤
the BGR 500, chapt. 2.29 „Verarbeiten von Beschichtungsstoffen“ (Applica-
tion of Coating Materials),
➤
the BGR 500, chapt. 2.36 „Arbeiten mit Flüssigkeitsstrahlern“ (Working
with Liquid Jets), both issued by the Berufsgenossenschaft der Gas-, Fern-
wärme- und Wasserwirtschaft.
We strongly recommend to add all relevant guidelines and accident prevention
instructions to this operating manual.
Moreover the manufacturer’s instructions and guidelines for coating or feeder
materials are to be respected at all times.
However, if you have any questions, please do not hesitate to contact us.
Excellent work results with your
WIWA
DUOMIX 230
wishes
WIWA
Wilhelm Wagner GmbH & Co. KG
.
Copyright
© 2013 WIWA
The copyright for this operating manual lies with
WIWA
Wilhelm Wagner GmbH & Co. KG
Gewerbestr. 1-3 • 35633 Lahnau • Germany
Phone: +49 6441 609-0 • Fax: +49 6441 609-50 • E-Mail: [email protected] • Internet: www.wiwa.de
This operating manual is solely intended for personnel involved in preparation,operation and servicing.
It is prohibited to pass on this operating manual for reproduction, utilisation or communication of its
contents, unless this has been explicitly permitted. Infringements incur an obligation to pay damage
compensation. All rights reserved in the event of registration of the patented design, industrial design or
registered design.
This operating manual only applies in conjunction with the machine card that was given to you with
the user manual for your unit. Please check that the type plate data is identical with the information on
the machine card. Please notify us immediately if there are discrepancies, if the user manual has been
incorrectly compiled or if the type plate is missing.
Summary of Contents for Duomix 230
Page 2: ......