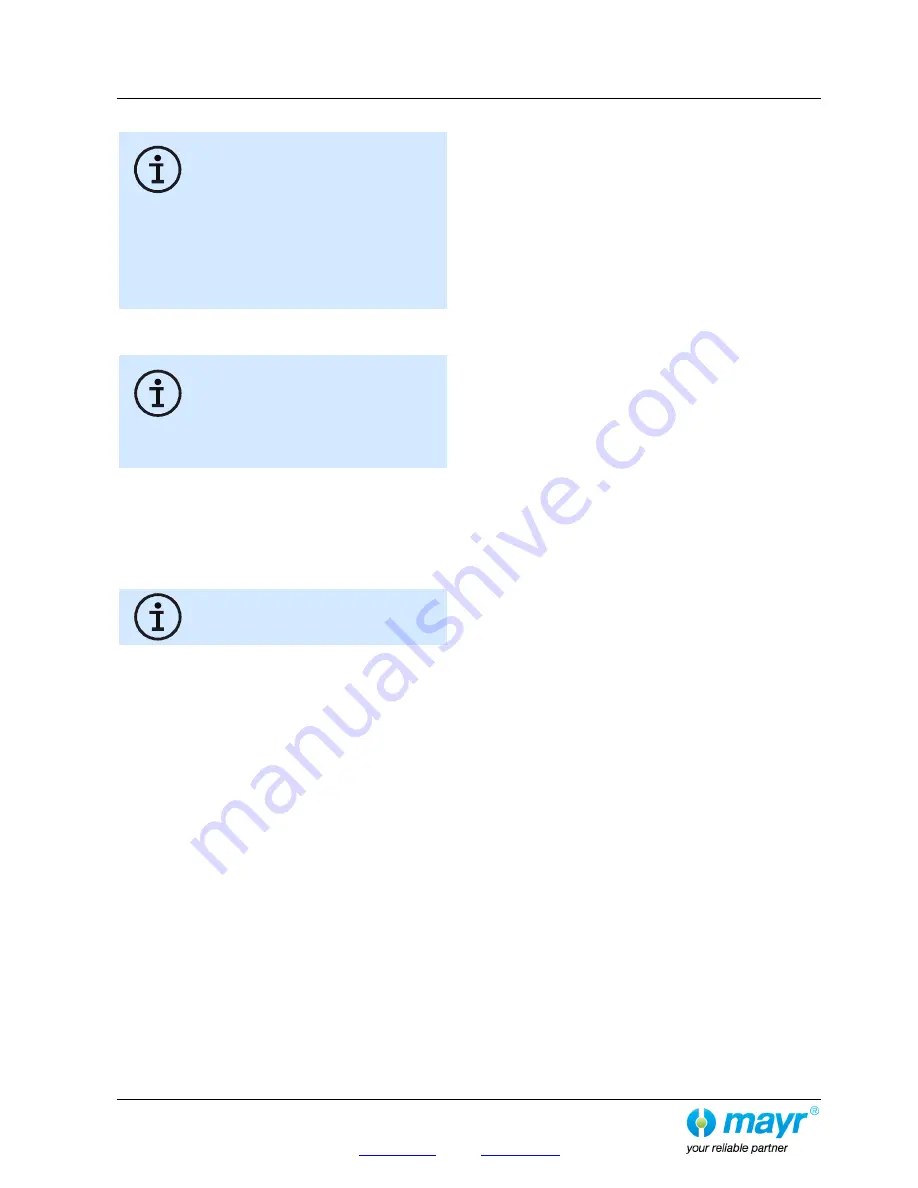
Installation and Operational Instructions for ROBA
®
-diskstop
®
Type 894.5_ _._ _ Size 10
(B.8.4.5.EN)
23/03/2017 TK/TL/GC/SU
Chr. Mayr GmbH + Co. KG
Eichenstraße 1, D-87665 Mauerstetten, Germany
Tel.: +49 8341 804-0, Fax: +49 8341 804-421
Page 12 of 16
www.mayr.com
, E-Mail:
Adjustment
The brakes are equipped manufacturer-side with
the respective springs for the braking force
stated on the Type tag. Adjustment is not
necessary. Adaptions or modifications are not
permitted as a rule. This rule also applies to the
manufacturer-side adjusted noise damping.
The microswitches are also adjusted manufacturer-side.
Despite great care during the manufacturer-side adjustment, re-
adjustment might be necessary after installation due to
transportation and handling. Furthermore, such switches
cannot be considered fail-safe.
Please observe the sections Release Monitoring and Wear
Monitoring.
Noise Damping (Item 11 / Fig. 1):
The noise damping was set and adjusted
manufacturer-side. However, this component is
subject to ageing dependent on the application
or operating conditions (torque adjustment,
switching frequency, ambient conditions,
system vibrations etc.).
Replacing the damping element is only
permitted at the
mayr
®
site of manufacture.
Brake Installation (Figs. 1
– 8)
The brake is pre-assembled manufacturer-side.
1. Release the brake mechanically using a suitable auxiliary
device.
2. Push the released brake over the brake disk and position it
so that both hexagon head screws (10) can be screwed in.
While pushing the brake over the brake disk,
please make sure that the friction linings are
not damaged.
3. Screw in the hexagon head screw (10) and tighten to a
tightening torque of 710 Nm
.
4. Remove the auxiliary device for releasing the brake.
5. Switch the brake 3 - 4 times so that it aligns with the brake
disk.
6.
Check that the brake moves axially on the pad (7). It
must be possible to move the opened brake in the guide
by hand. On an engaged brake, there must be a gap of at
least 2 mm between the pad (7) and the counterplate (3)
as well as between the pad (7) and the armature disk (2),
see Fig. 7.
7.
Check the air gaps "a" (Fig. 2) between the coil carrier
(1) and the armature disk (2).
In new condition, the air gap "a" must be max. 1 mm on a
de-energised brake. Measurements on both sides at friction
pad (4) level
– calculate the average.
8. On the de-energised brake, tighten the cap screws (17) with
10 Nm.
9. Energise the brake.
10. Measure the effective air gap between the friction lining and
the side of the brake disk facing away from the screw-on
surface on the right and left-hand sides and calculate the
difference between the measurement values.
The
differential dimension must be < 0.3 mm
.
11. Turn the brake disk. The brake disk must not rub against
anything.
Installation of Bowden Cable Hand Release
The hand release is pre-assembled manufacturer-side.
In order to install the Bowden cable, the lock washer (6.2) must
be mounted on the correct side. If this is not the case, the lock
washer (6.2) must be screwed off and screwed onto the opposite
side.
The hand release lever (6.1) can be pivoted by approx. 30°.
Adjust the Bowden cable so that the hand release can pivot back
to the middle position (after actuation)
=> Functional inspection
.
Brake Inspection
(before brake initial operation)
Visual inspection:
for proper condition of the brake (rust etc.) and no grinding.
Carry out a release inspection:
by energising the brake or manually by actuating the hand
release.
Switch functions inspection of the release monitoring /
for connection as NC contact:
Brake energised
Signal “OFF”
Brake de-energised
Signal "ON"
for connection as NO contact:
Brake energised
Signal “ON”
Brake de-energised
Signal “OFF”
The braking torque is not achieved until after the run-in
procedure has been carried out.
The run-in conditions must be aligned with the manufacturer.
Braking Torque
The (nominal) braking torque is the torque effective in the shaft
train on slipping brakes, with a sliding speed of 1 m/s referring to
the mean friction radius.
The brake is loaded statically when used as a service brake and
loaded dynamically in EMERGENCY STOP operation (part of
the brake equipment against overspeed or inadvertent
movement of the elevator cage). Respectively, there are different
speed values for the friction material, which in practice also
leads to different friction values and therefore braking torques.
The braking torque is dependent on the respective run-in
condition of the friction surfaces.
We recommend allowing the friction surfaces to run in when
installed and under permitted loads.
Friction materials develop their optimum effect only under speed
at the appropriate contact pressure, as continuous regeneration
of the friction surface then takes place (torque consistency).
Furthermore, friction materials (synthetic resin bonded rubber
mixtures) are subject to ageing, which is also influenced, among
other things, by higher temperatures and other ambient
influences. We recommend regular inspection of the braking
torque (1 x per year) including the respective dynamic braking
actions as a refresher.