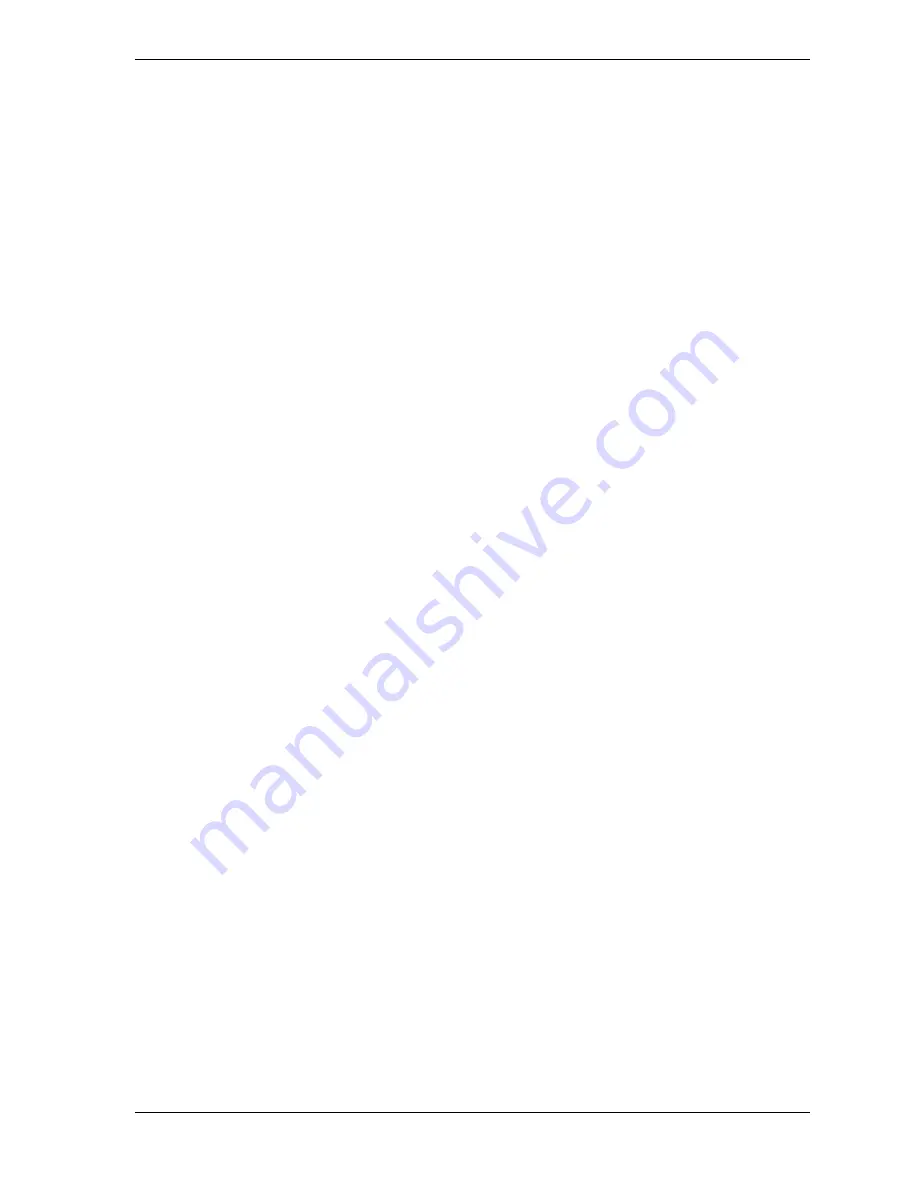
WPC 1000 User Manual
1125100
Introduction
1-7
•
Customized Status Codes–WPC 1000 provides three user inputs that allow you to monitor
auxiliary press functions, such as lubrication systems. When one of these functions issues a
Stop command, a unique status code is displayed on the digital LED readout to identify
why the press stopped. One of the inputs is a cross-checked pair, which you can use for a
safety interlock.
•
Brake Monitor–WPC 1000’s Top-stop brake monitor checks the press’s braking
performance every time a Top-stop command is initiated or when the press completes a
stroke at Top-stop. When the press’s stopping time is within ten milliseconds of the preset
Stop-time Limit, the Brake Warning LED flashes. When the stopping time exceeds the
Stop-time Limit, WPC 1000 issues a Stop command to the press and prevents the press
from being restarted until the brake has been serviced.
•
90° Stop-Time Test–This standard feature is required in order to set the correct safety
distance for personnel-guarding devices including light curtains, two-hand controls, and
type-B movable barriers. The test is performed at 90°, the press’s most critical stopping
point, with the press running in Continuous and the heaviest die installed. The results of
the test provide the stopping time (Ts) value specified in both OSHA 1910.217 and ANSI
B11.1-2009 (see Appendix A).
•
Micro-inch–A feature that allows you to set the amount of time that the Dual Safety Valve
is open in Inch mode when you push the Run/Inch palm buttons. Normally, in Inch the
DSV is open for only as long as the Run/Inch buttons are depressed. The Micro-inch
setting specifies the length of time the DSV is open regardless of how long the Run/Inch
buttons are held. Allowing finer adjustments than are possible in Inch, Micro-inch is
designed to facilitate setup on high-speed or short-stroke presses. Requires installation of
optional Micro-inch selector switch (see page 1-2).
•
Error Codes–WPC 1000 displays a two-digit code preceded by the letter “E,” “F,” or “H
whenever the press is stopped because of a fault. The two-digit code identifies the specific
problem that caused the fault. The initial letter indicates how the fault should be reset, and
in the case of F and H errors, specifies the processor (A or B) that detected the problem.
Underlying causes and remedies for each fault code are provided in Chapter 5.
•
Lockout–Selected error codes that are associated with serious error conditions generate the
lockout message “Loc,” which displays in the digital LED readout when the error has been
reset. The lockout function provides an added safety feature to WPC 1000, forcing the
operator to perform two different Reset operations. The “Loc” message is cleared by
turning the Stroke Select key switch to “OFF,” then to “INCH.”
Optional Features
•
Counterbalance Air Pressure Switch–Operating identically to the clutch air pressure
switch, this switch is used with the counterbalance air supply on presses equipped with
counterbalances, as required by OSHA regulations.
•
Two-channel Programmable Cam Switch–Provides cam timings for feed, pilot release,
air blow-off, lubricator, or other non-safety press equipment.
Summary of Contents for WPC 1000
Page 17: ...1125100 WPC 1000 User Manual xii Table of Contents ...
Page 99: ...1125100 WPC 1000 User Manual 2 72 Installation ...
Page 207: ...1125100 WPC 1000 User Manual A 18 Extracts from OSHA and ANSI ...
Page 217: ...1125100 WPC 1000 User Manual G 6 Glossary ...
Page 223: ......
Page 224: ......
Page 225: ......
Page 226: ......
Page 227: ......
Page 228: ......
Page 229: ......
Page 230: ......
Page 231: ......
Page 232: ......
Page 233: ......
Page 234: ......
Page 235: ......