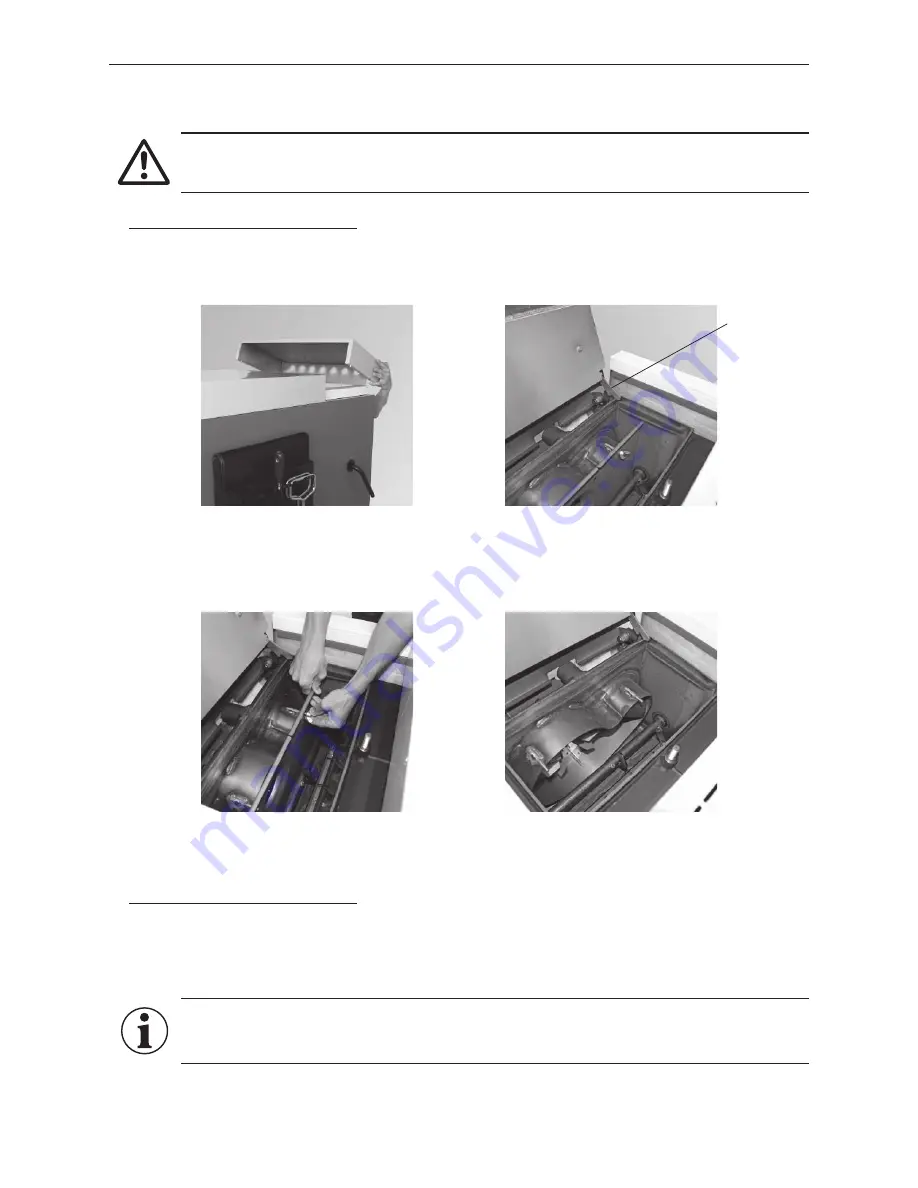
27
3.
Care, cleaning and maintenance
3.3.2 Blower box, blower wheel
Att
ention!
Before cleaning the blower box and blower wheel, de-energise the boiler!
Recommended cleaning implement: Spatula, brush and vacuum cleaner
– Remove the rear boiler cover – Fig. 63.
– Remove screw connection from cleaning cover and fold up cover until cover lock snaps in – Fig. 64.
Fig. 63 Removing the boiler cover
Fig. 64 Opening cleaning cover
Cover lock
– Remove wing nut from blower box (Fig. 65), take out blower cover and clean.
– Clean all of blower box, including blower wheel – Fig. 66.
Fig. 65 Removing wing nut from blower cover
Fig. 66 Cleaning blower box and blower wheel
3.3.3 Exhaust pipe:
Recommended cleaning implement: Spatula, cleaning brush, soft cloth
– Clean the exhaust pipe leading to the flue through the cleaning opening provided in the exhaust pipe or
through the blower box.
– Use soft cloth to clean exhaust sensor.
Information!
Watch out for the sensors in the flue outlet when cleaning the exhaust pipe. Do not bend or damage
them. No warranty claims will be accepted for damage attributable to incorrect cleaning!