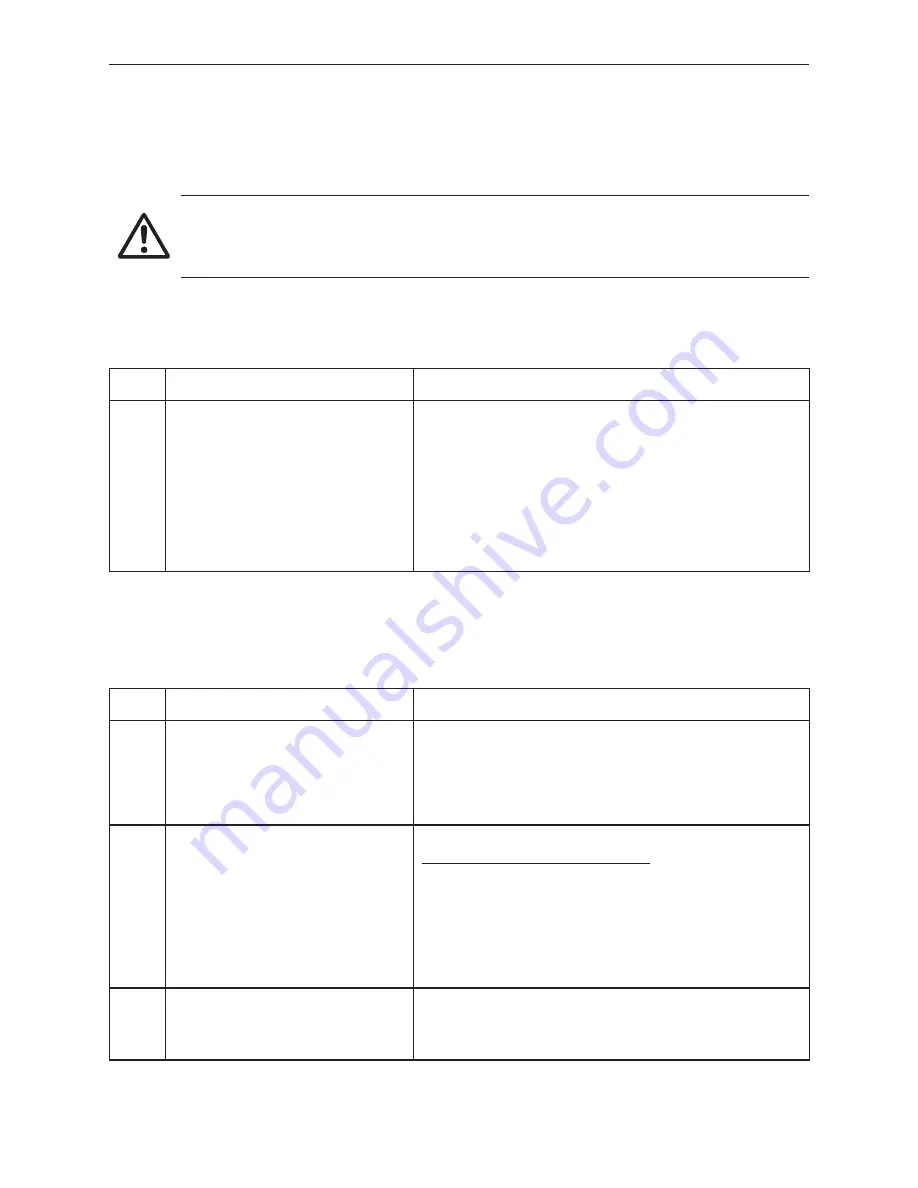
31
4.
Troubleshooting
4.2 No display on InfoWIN
Code
Display on InfoWIN
Cause/remedy
–
No display,
LED not lit up
Boiler is off, cannot be switched on with the
On/Off button.
a) No mains voltage, check the cable to the device and the building fuse.
b) No mains voltage, device fuse blown – check and replace if necessary
- see Fig. 75.
c) Mains power plug loose or poorly or not connected together during in-
stallation – check and connect together firmly if necessary
d) InfoWIN plug loose or poorly or not connected together during instal-
lation – check and connect together firmly if necessary, plug is located
behind the right side panel cladding – see LogWin assembly instruc-
tions; Installing the cladding.
e) Inform Windhager Customer Service or a heating technician.
4.3 FE – messages
Code
Display on InfoWIN
Cause/remedy
FE 226
No flame during ignition
Ignition failurel.
Press reset..
a) No fuel in front of ignition opening. Heating up process not performed
according to the instructions. Press the Reset button.
b) Ignition opening in lighting door or on vertical grate covered with ash,
clean (see 3.1.2). Press the Reset button.
c) Ignition element defective, inform Windhager Customer Service or a
heating technician.
FE 268
Cladding door switch defective
Do not continue heating!
Let the boiler burn out, the fault must be rectified.
After burning out (Standby operating phase):
Open the cladding door – blower must be running.
Cladding door closed or press cancel heating up – blower must stop.
If this doesn’t happen:
a) Check and adjust shifting travel of cladding door switch (audible click)
– see LogWIN assembly instructions.
b) Cladding door switch defective, inform Windhager Customer Service
or a heating technician.
FE 281
Flue gas temperature sensor
defective
Check the flue gas temperature sensor and
connections.
It is not possible to display the flue gas temperature. No effect on opera-
tion.
Replace flue gas temperature sensor. Inform Windhager Customer Ser-
vice or a heating technician.
4.1 Thermal process safeguard
If the thermal process safeguard is dripping, clean the seals and the valve seat. Replace the piston and the seal
if necessary – see the enclosed list of spare parts.
Note:
There is no need to remove the fitting for this purpose.
Att
ention!
The function of the thermal process safeguard must be checked once a year by a technician and
the thermal safety device must be checked for limescale – see assembly instructions. If there is
limescale in the thermal safety device then it must always be removed.