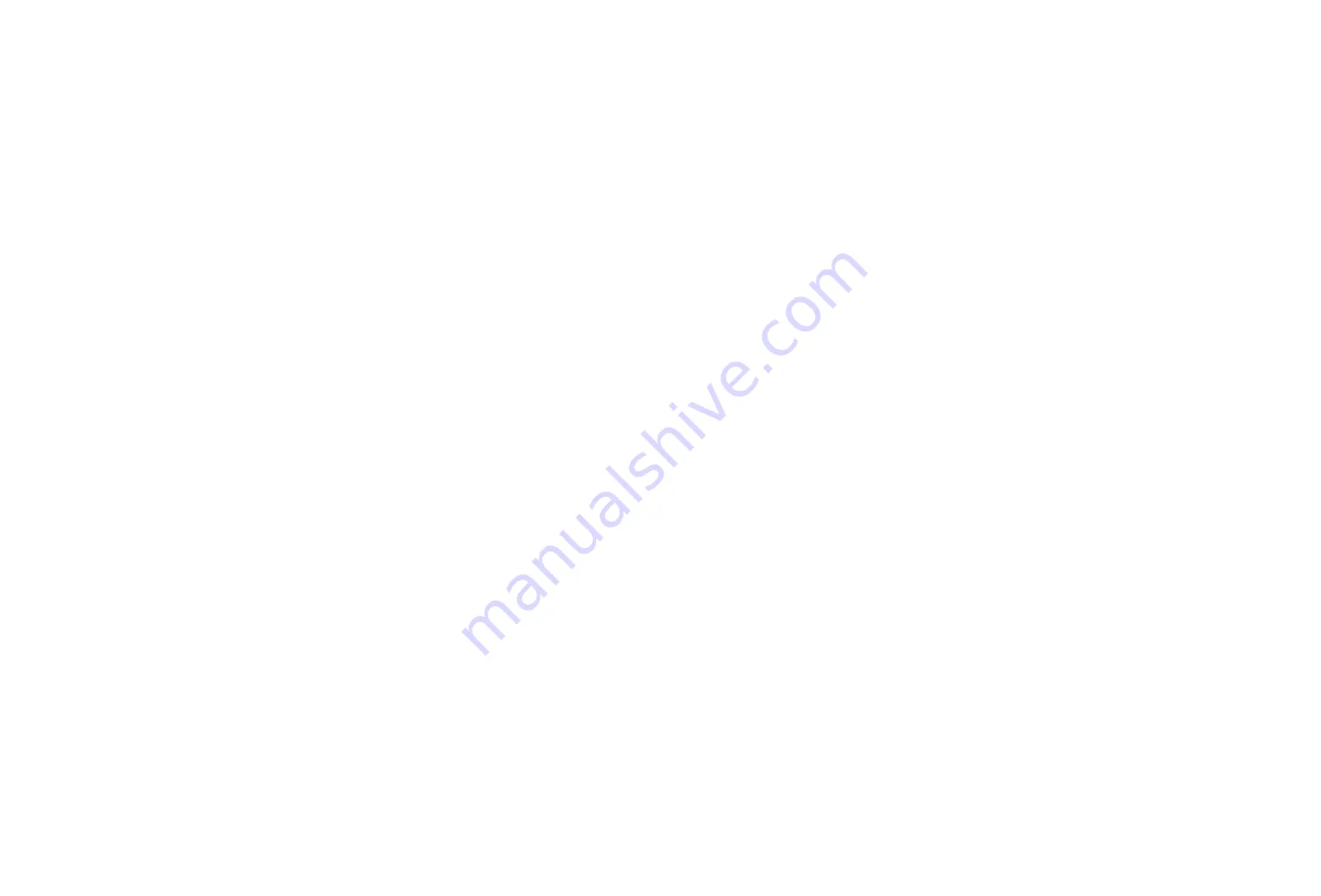
28
29
English
English
6.5 After starting
The rated current is briefly exceeded during the start-up procedure.
Once this process has ended, the operating current should no longer
exceed the rated current.
If the motor does not start immediately after the machine is
switched on, it must be switched off immediately. The start
pauses specified in the technical data must be adhered to
before starting up again. If the fault recurs, the machine must
be switched off again immediately. The machine may only be
started again once the fault has been rectified.
The following items should be monitored:
- Operating voltage (permissible dev/-5% of the rated
voltage)
- Frequency (permissible dev/-2% of the rated
frequency)
- Current consumption (permissible deviation between phases
is a maximum of 5%)
- Voltage difference between the individual phases (max. 1%)
- Starts and stops per hour (see technical data)
- Air entry in the infeed, a deflector plate should be fitted if
necessary
- Minimum water immersion level, level control unit, dry-run
protection
- Smooth running
- Check for leaks, if need be, follow the necessary steps as set
out in “Maintenance”
- Check for suspension device leakage. There is no obvious
leakage from the fitting surface between the pump flange
and coupling base when the water level is submerged to 1/2
of the motor at 0.7 rated flow
As mechanical shaft seals have a certain running-in phase,
it is possible that minor leaks may occur. This running-in
phase lasts approx. 1 – 3 months. Change the oil several
times during this phase. Please consult the manufacturer if
leakage continues after this running-in phase has ended.
Operation in the limit range
The maximum limit range deviation for operational data is
+/-10% of the rated voltage and +3% to –5% of the rated
frequency. The permissible voltage difference between the
individual phases is a maximum of 1%. Continuous operation
in the limit range is not recommended.
7 Maintenance
The machine and the entire system must be inspected and
maintained at regular intervals. The time limit for maintenance
is set by the manufacturer and applies to the general
conditions of use. The manufacturer should be consulted if the
system is to be used with corrosive and/or abrasive pumped
liquids, as the time limit between inspections may need to be
reduced.
Note the following information:
- The operating and maintenance manual must be available
to the maintenance personnel and its instructions followed.
Only the repair and maintenance measures listed here may
be performed.
- All maintenance, inspection and cleaning work on the
machine and the system may only be carried out by trained
specialists exercising extreme care in a safe workplace.
Proper protective clothing is to be worn. The machine must
be disconnected from the electricity supply before any
work is carried out. There must be no way that it can be
inadvertently switched on.
- Above a weight of 50kg, only hoisting gear which has been
officially approved and which is in a technically perfect
condition should be used for lowering and raising the
machine.
Make sure that all fastening devices, ropes and safety
devices of the hand winch are in a technically perfect
condition. Work may only commence if the auxiliary hoisting
gear has been checked and found to be in perfect working
order. If it is not inspected, danger to personnel may result.
- Electrical work on the machine and system must be carried
out by an electrician. For machines approved for work
in areas subject to explosion danger, please refer to the
“Explosion protection in accordance with the ... regulation”
chapter. Defective fuses must be replaced. Under no
circumstances are they to be repaired. Only fuses at the
specified current and of the prescribed type may be used.
- When working with inflammable solvents and cleaning
agents, fires, unshielded lighting and smoking are prohibited.
- Machines which circulate fluids hazardous to health, or which
come into contact with them, must be decontaminated. It must
be ensured that no dangerous gases can form or are present.
If injuries involving hazardous pumping liquids or gases
occur, first-aid measures must be performed in accordance
with the notices in the workplace and a doctor should be
called immediately.
- Ensure that all necessary tools and materials are available.
Tidiness and cleanliness guarantee safe and problem-free
operation of the machine. After working on the machine all
cleaning materials and tools should be removed from it. All
materials and tools should be stored in an appropriate place.
- Operating supplies such as oil and lubricants must be collected
in appropriate vessels and properly disposed of .Appropriate
protective clothing is to be worn for cleaning and maintenance
jobs. Only lub-ricants expressly recommended by the
manufacturer may be used. Oils and lubricants should not be
mixed. Only use genuine parts made by the manufacturer.
A trial run or functional test of the machine must be
performed as instructed in the general operating conditions.
7.1 General overhaul
During this the bearings, shaft seals, O rings and power supply
cables are inspected and replaced as required in addition to
normal maintenance work. This work may only be conducted
by the manufacturer or an authorized service workshop.
7.2 Lubricants
- The machine lubricants may only be topped up or replaced
with lubricants from the same manufacturer.
- Machines which have previously been operated using other
lubricants must first be thoroughly cleaned before they can
be operated.
7.3 Maintenance intervals
Before initial start-up or after a longer period of storage
- Checking the insulation resistance
- Fill level check in sealing room/chamber – lubricant must
reach up to the lower edge of the filling opening
Monthly
- Monitoring the current consumption and voltage
- Checking the used relays for posistors, sealing room monitor,
etc.
Every six months
- Visual inspection of the power supply cable
- Visual inspection of the cable holder and the cable bracing
- Visual inspection of accessories, e.g. the suspension device
and hoisting gears
Yearly
- Changing the lubricant in the sealing room/chamber
- Emptying the leakage chamber (not present in all models)
- Functional inspection of all safety and control devices
- Coating check and touch-up as required
7.4 Maintenance tasks
Monitoring the current consumption and voltage
The current consumption and voltage is to be monitored
periodically during all 3 phases. This remains constant during
normal operation. Slight fluctuations are a result of the
composition of the pumped fluid. The current consumption
can assist in early detection and correction of damage and/or
faulty operation in the impeller/propeller, bearings and/or the
motor. More extensive resulting damage can thus be largely
prevented and the risk of a total failure can be reduced.
Checking the used relays for posistors, sealing room
monitor, etc.
Check the relays used are functioning fault-free. Defective
devices must be immediately replaced, because these cannot
ensure safe operation of the machine. The test procedure
details should be followed closely (in the operating instructions
for each relay).
Checking the insulation resistance
To check the insulation resistance, the power supply cable
must be disconnected. The resistance can then be measured
with an insulation tester (measuring voltage = 500V DC). The
following values may not be exceeded:
The insulation resistance may not be below 100mega-ohms
during initial operation. For all further measurements the value
of cold insulation resistance must be greater than 5mega-
ohms,and the value of hot insulation resistance must be
greater than 0.5mega-ohms Insulation resistance too low:
Moisture may have penetrated the cable and/or the motor.
Do not connect the machine, consult manufacturer.
Visual inspection of the power supply cable
The power supply line must be examined for bubbles, cracks,
scratches, chafed areas and/or crushed sections. If damage is
found, the power cable must be exchanged immediately.
The cables may only be changed by the manufacturer or an
authorized/certified service workshop. The machine may
not be used again until the damage has been adequately
rectified.
Visual examination of the cable holders (carabiners) and the
cable bracing
When the machine is used in basins or pits, the lifting cables/
cable holders (carabiners) and the cable bracing are subject
to constant wear. Regular inspections are necessary in order
to prevent the lifting cables/cable holders (carabiners) and/or
cable bracing from wearing out and to prevent the electricity
cable from being damaged.
The lifting cables/cable holders (carabiners) and the cable
bracing are to be immediately replaced if any signs of wear
appear.
Visual inspection of accessories
Inspect accessories such as suspension units and hoisting gear
to check whether they are secured in a stable manner. Loose
and/or defective accessories should be repaired immediately or
replaced.
Functional inspection of safety and control devices
Motor temperature monitor
PTC sensors must be connected via an evaluation relay in the
switchgear. The max. motor temperature is 135 °C. This equals
to a threshold of 750 Ohm. When the threshold is reached, the
unit must switch off. For this reason, no warranty claims can
be accepted for any damage to the winding resulting fromun-
suitable motor monitoring.
Monitoring the sealing chamber
The sealing chamber is monitored by an internal pencil
electrode. This must be connected via an evaluation relay. The
recommended threshold is 100 kOhm. When the threshold is
reached, a warning must be given or the unit switched off.
Monitoring the Motor/terminal compartment
The Motor/terminal compartment is monitored by an internal
pencil electrode. This must be connected via an evaluation
relay. The recommended threshold is 100 kOhm. When the
threshold is reached, a warning must be given or the unit
switched off.