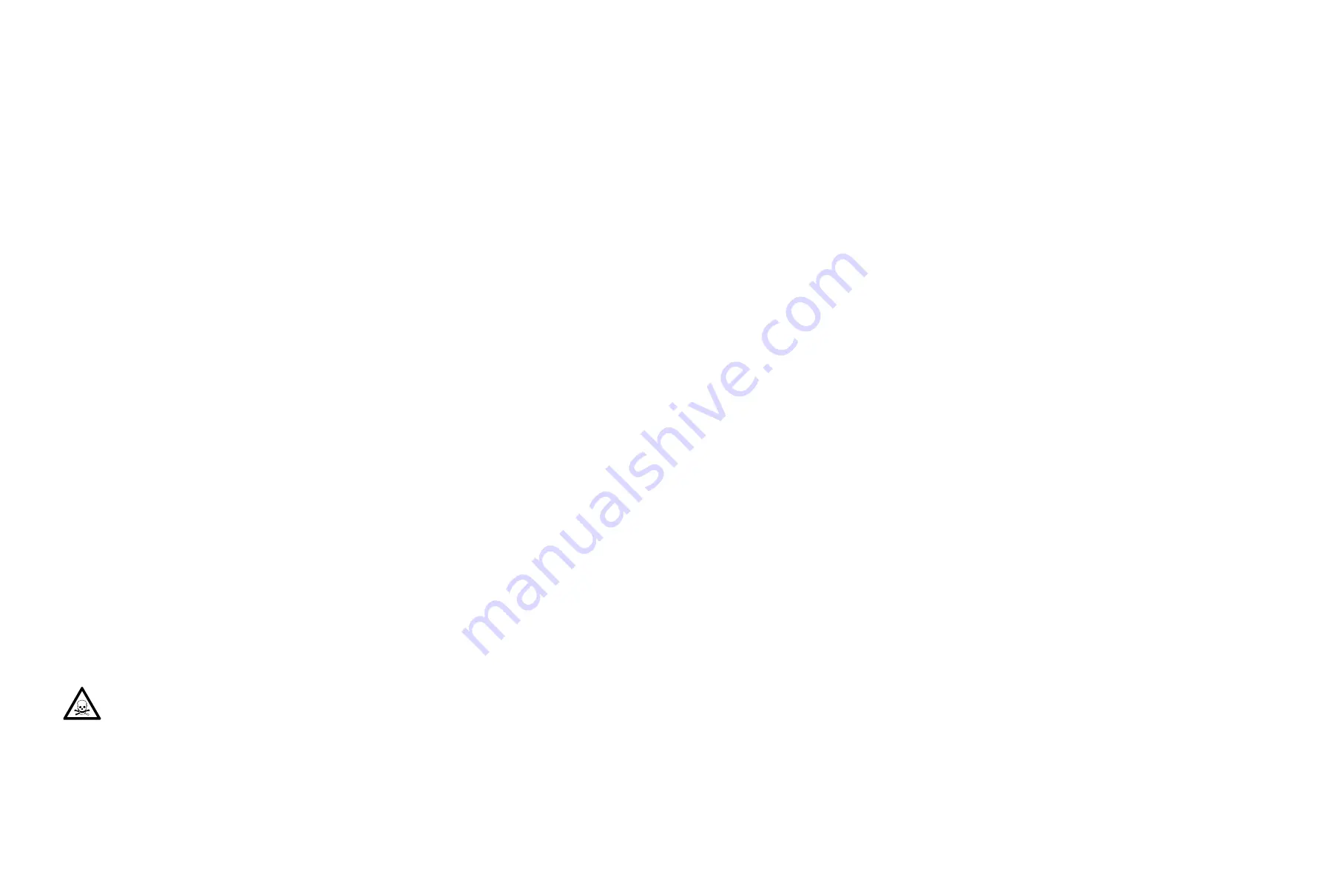
26
27
English
English
5.6 Dry-run protection
The machine must always be submerged up to the top edge
of the pump housing. Make sure that no air enters the pump
housing.
For optimum reliability, we recommend installing a dry-
run protection system. Correct running is ensured by float
switches or electrodes. The float switch / electrode is fastened
in the pit and switches off the machine when the water level
falls below the minimum coverage level.
For dry installations, the float switch must be fitted at an
appropriate height in the collector tank.
Please observe the information about the minimum water
coverage.
If dry-run protection is only put into effect with one float
or electrode when filling levels deviate strongly, then the
machine may turn on and off constantly!
This can result in the maximum number of motor start-ups
being exceeded.
5.7 water level control
Manual reset
The motor is switched off when the water level falls below
the minimum coverage level and switched back on when a
sufficient water level is reached.
Separate reactivation point
Using a second switching point (additional float or electrode),
a sufficient difference is obtained between the activation and
deactivation points. This prevents constant switching. This
function can be put into effect with a level control relay.
5.8 Removal
When removing the machine, make sure that it is first disconnected
from the mains.
On portable installations, the machine can be lifted out of
the pit after it has been disconnected from the mains and the
discharge pipe has been emptied. You may have to disconnect
the hose first. Here too, you should use appropriate lifting gear
if the pit is deep, or the machines are heavy.
On wet installations with suspension units, the machine is
raised out of the pit using the chain or lifting cable with the
help of a hoisting gear. This does not have to be emptied
especially for this purpose. Make sure the power supply cable
does not become damaged.
Beware of poisonous substances!
Machines which pump fluids hazardous to health
present a fatal
risk. These machines must be decontaminated before
any other
work is carried out. Wear the necessary protective
clothing/
equipment when doing so.
6 Start up
The "Startup" chapter contains all the important instructions
for the operating personnel for starting up and operating the
machine safely.
The following specifications must be adhered to and checked:
- Type of installation
- Operating mode
- Minimum water coverage / max. submersion
If the machine has not been operated for some time, check
these specifications again and rectify any faults you find.
The operation and maintenance handbook must always be
kept either by the machine or in a place specially reserved
for it where it is accessible for operating personnel at all
times.
In order to prevent damage or serious injury during startup of
the machine, the following points
must be observed:
The machine may only be started up by qualified personnel.
The safety advice must be followed at all times.
- Every person working on the machine must have received,
read and understood this operating and maintenance
manual. This must also be confirmed with a signature in the
machine operator list.
- Activate all safety devices and emergency stop elements
before startup.
- Electrical and mechanical settings may only be made by
specialists.
- This machine may only be used under the working conditions
specified in this handbook.
6.1 Preparatory measures
The machine has been designed and constructed using the
very latest technology. Under normal working conditions it will
operate reliably and for long periods. The one condition for this
is that all instructions and advice are observed.
Minor oil leakage in the mechanical shaft seal on delivery is
no cause for concern. However, it must be removed prior to
submersion in the pumped liquid.
Please check the following:
- Cable guidance – no loops, slightly taut
- Check the temperature and submersion depth of the
pumped liquid – see machine data sheet
- If a hose is used on the discharge side, it should be flushed
out with clean water before use to prevent any sediment
causing blockages
- The pump sump must be cleaned for wet installation
- Clean the discharge and intake side pipe system and open all
sliders
- The pump housing must be flooded, i.e. it should be completely
full of fluid, with no air in it at all. Bleeding can take place using
a suitable bleeding device in the system, or, if available, with
bleeder screws on the discharge port.
- Check that all accessories, the pipe system and suspension
unit are properly fitted
- Check all level control and dry-run protection systems
An insulation test and filling level check must be carried out
prior to start-up, as described in chapter 7.
6.2 Electrical system
Observe the relevant local and national regulations when
laying out and selecting the electric lines as well as when
connecting the motor. The motor must be protected by a
motor protection switch.
Have the motor connected in accordance with the "Electrical
connection" data sheet. Pay attention to the direction of
rotation. If the direction of rotation is incorrect, the machine
will not perform as specified, and under certain circumstances,
can become damaged. In accordance with the machine data
sheet, check the operating voltage and make certain that the
current consumption remains uniform during all phases.
Make sure that all temperature sensors and monitoring
devices, such as the sealing chamber monitor, are connected
and that their function is tested.
Electrical current can cause fatal injuries if not handled
correctly!
All machines with free cable ends (i.e. without plugs) must
be connected by a qualified electrician.
6.3 Direction of rotation
The machine must be connected in accordance with the
data sheet “Electrical connection plan”. Rotation direction is
controlled by a rotating field tester. This tester is switched
on when the pump is connected and displays the rotation
direction of the rotating field. There must be a clockwise
rotating field for the machine to run correctly.
If a counter-clockwise rotating field is displayed, two phases
must be swapped.
6.4 Motor protection and activation types
Motor protection
The minimum requirement is a thermal relay / motor protection
switch with temperature compensation, differential triggering and
an anti-reactivation device in accordance with the appropriate
national regulations. If the machines are connected to electrical
systems in which faults frequently occur, we recommend
installing additional protective devices (overvoltage, undervoltage
or phase failure relays, lightning protection). Local and national
regulations must be adhered to when connecting the machine.
Activation types with plugs /relays
Units with plugs
Connect the plug to the socket provided and press the On/Off
switch on the relay.
Activation types for cables
Units with relays
Please observe the relay manual.
Activation types for cables with free ends (without plugs)
Direct activation
Motor protection should be set to the rated current when fully
loaded. At partial load, we recommend that motor protection
is set 5% above the measured current at the operating point.
Star-delta activation
If the motor protection is installed in the line:
Set the motor protection to 0.58 x the rated current. The maximum
start-up time in star-delta mode is 3 seconds.
If the motor protection is not installed in the line:
Set the motor protection to the rated current when fully loaded.
Starting transformer/soft start
Motor protection should be set to the rated current when fully
loaded. At partial load, we recommend that motor protection
is set 5% above the measured current at the operating point.
The maximum start-up time at reduced voltage (approx. 70%)
is 3 seconds.
Monitoring equipment
Overheating protection: Up and equal to4kW power of the
pump with double metal temperature sensor, Power ≥ 5.5kW
pumps with thermistor PTC.
Leakage protection: For pumps power between 5.5kW to
22kW, there are equipped with leakage sensors in the motor
housing and oil chamber, to detect if any leakage in the motor.
The sensor in the oil chamber could detect if any oil leakage
into the oil chamber to further protect the motor damaged
from more water leakage. The alarm will shut off the motor to
avoid the damage of motor.
For power ≥ 30kW pumps, there are also equipped with leakage
sensor in the terminal compartment. This signals if there is any
leakage in the terminal compartments.
Depending on the customer's requirement, power ≥ 30kW
pumps can equipped with an anti-condansation heater.
There are protection function like lack-phase protection,
overload protection, low-voltage protection, and short-circuit
protection available through the control panel.
Monitoring device connections
Power between 5.5kW to 22kW pumps have a 3 wires control
cable (K1/K2/K3) connecting with electric protector. Thermal
monitoring of the motor is performed by PTC sensors. K1 and
K2 wires are connected with PTC sensors to monitor motor
overheat. K3 wire is connected with the internal electrode to
monitor the motor and sealing chamber leakage.
The motor rated power ≥ 30kW has a 7 wires control cable (K1/
k2/k3/K4/K5/K6/K7) connecting with electric protector. K1
and K2 wires are connected with PTC sensors to monitor motor
overheat. K3 wire is connected with the internal electrode
to monitor the motor compartment leakage. K4 wire is con-
nected with the internal electrode to monitor the sealing
chamber leakage. K7 wire is connected with the internal electrode
to monitor the terminal compartment leakage. K5 and K6 wires
are connected with the anti-condansation heater (Depending
on the customer’s requirement).