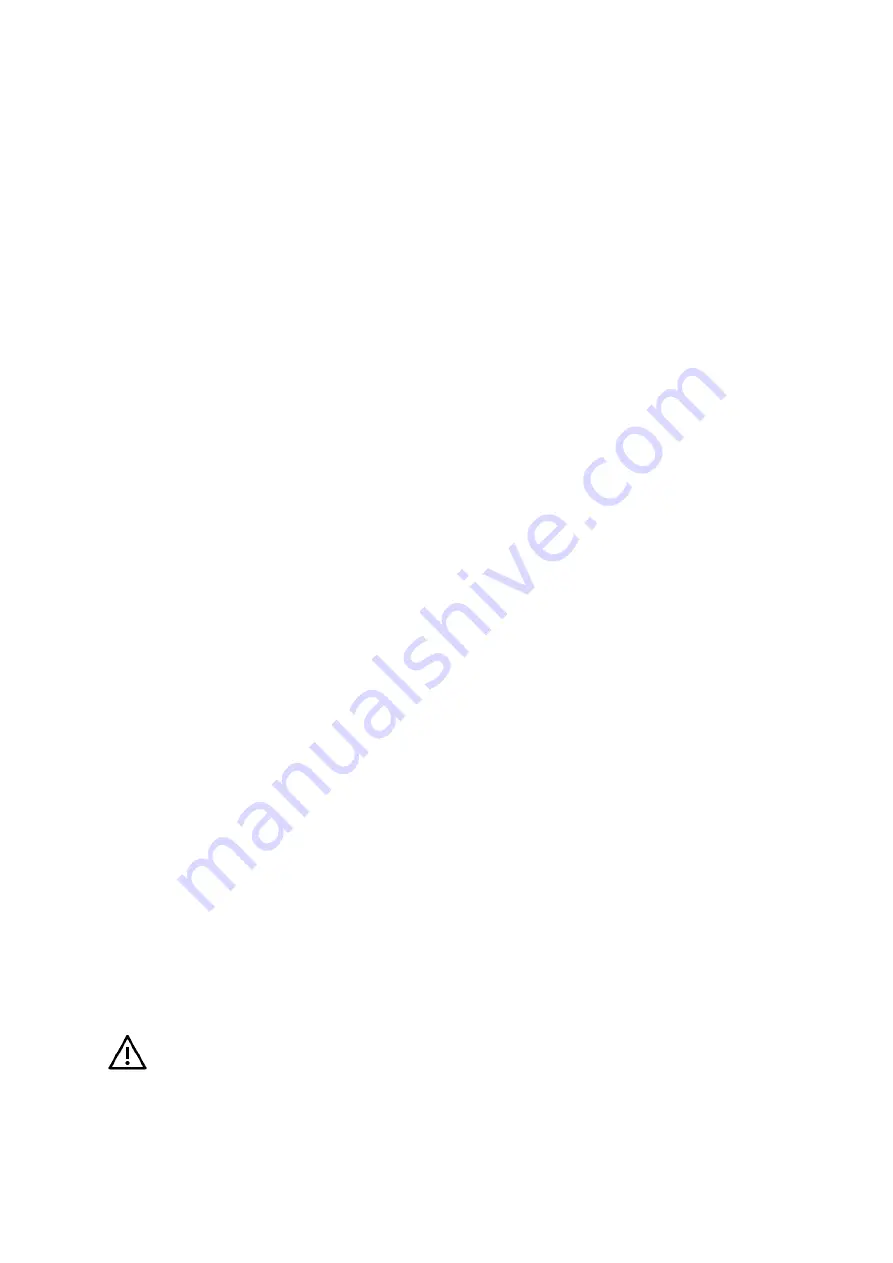
English
48
PLE Systems & Solutions, Engineering Center Systems Oschersleben
2530098 Ed.3 EBA-VBH- vorläufig De/En- 01.11.2018
7.6 Connecting the pressure boosting system
The connection between the break tank and the pressure boosting system is set up at the draw-off
connection (3). It is absolutely necessary that the connection be made stress-free in order to avoid any
damage caused by the transfer of mechanical vibrations. Depending on the type and size of the tank,
and thus in accordance with the type of draw-off connection being used, a flexible connection line (Fig.
5a) or a compensator (Fig. 5b) should be utilised for this purpose.
To avoid water losses, it is recommended that a check valve be installed without fail between the break
tank and the pressure boosting system for facilitating maintenance work.
7.7 Connection to the water supply network
The connection between the break tank and the water supply network is accomplished by means of an
inlet valve which opens and closes in accordance with water levels (accessory; to be ordered
separately). Depending on the type and size of the tank, there are basically two different possible
versions available for use.
7.4.3 Float valve (for type ACS already installed in scope of delivery)
One or more feedthroughs are provided for installation in tanks which will be connected and fed to the
drinking water supply system by means of a float valve (16) (see dimension sheets Fig. 1a to l (1)). For
installation (Fig. 3a and 3b) the float valve is guided from the inside through the opening of the tank
provided for this purpose with the connecting thread of the housing (16-4) and fixed from the outside
with the lock nut (16-3). The linkage (16-4) and the outlet opening of the float valve must point
downwards. On float valves with SlowFlow adapter (Fig.3b (16-6)) the valve is additionally secured by
means of the screws (16-7).
After the float valve, a detachable screwed pipe connection (17) and a shut-off valve (18) should be
fitted so that the water supply can be interrupted and the valve can be easily dismantled if necessary.
A T-piece (example see Fig.3a (19)) must be provided, especially for fire extinguishing systems which
are used relatively rarely, so that an automatic flushing device (32) can be connected in the case of
stagnating water in the supply pipe in order to enable water replacement.
When the connection to the supply network has been completed and the tank is already filled via the
float valve, the closing level must be adjusted by adjusting the rod and moving the float. The valve
should close tightly at the latest when the level is about 100 to 50 mm below the lower edge of the
overflow.
7.4.4 Diaphragm valve (for tanks with appropriate connection)
In the case of break-tanks which are fed by a diaphragm valve (Fig.4), there is a connection flange (2)
on the cover (standard flange, dimensions correspond to DIN EN 1092 PN10) and a through-hole (1)
for a pilot float valve (24) on the front face side. In addition to the description given here, the installation
instructions enclosed with the valves must also be observed for installation. The pilot valve float valve
(24) is to be installed in the same way as a float valve as described under 7.4.1. The diaphragm valve
(21) must be installed horizontally at a suitable height above the tank (see Fig. 4). A shut-off valve (23)
of the same nominal size must be installed before and after the diaphragm valve. The pipeline from the
valve to the vessel must be led to the connection flange intended for this purpose and connected with
the threaded inserts provided by means of screws. It must be ensured that the weight of the diaphragm
valve, all other fittings and the weight of the pipeline do not have any effect on the tank, but must be
transferred to the building structure (wall or ceiling) by means of pipe clamps (20) or other suitable
devices.
WARNING! Danger of injury and danger of damage to the tank.
The cover of the break tank cannot be walked on! Non-permitted loads on the cover
can lead to destruction.
Once the diaphragm valve and the supply piping have been installed, install a control pipe (22) from
the diaphragm valve to the float valve. An armoured hose from the accessories range can be used for
this purpose. This has to be mounted on the diaphragm valve (21) at the intended screw connection on