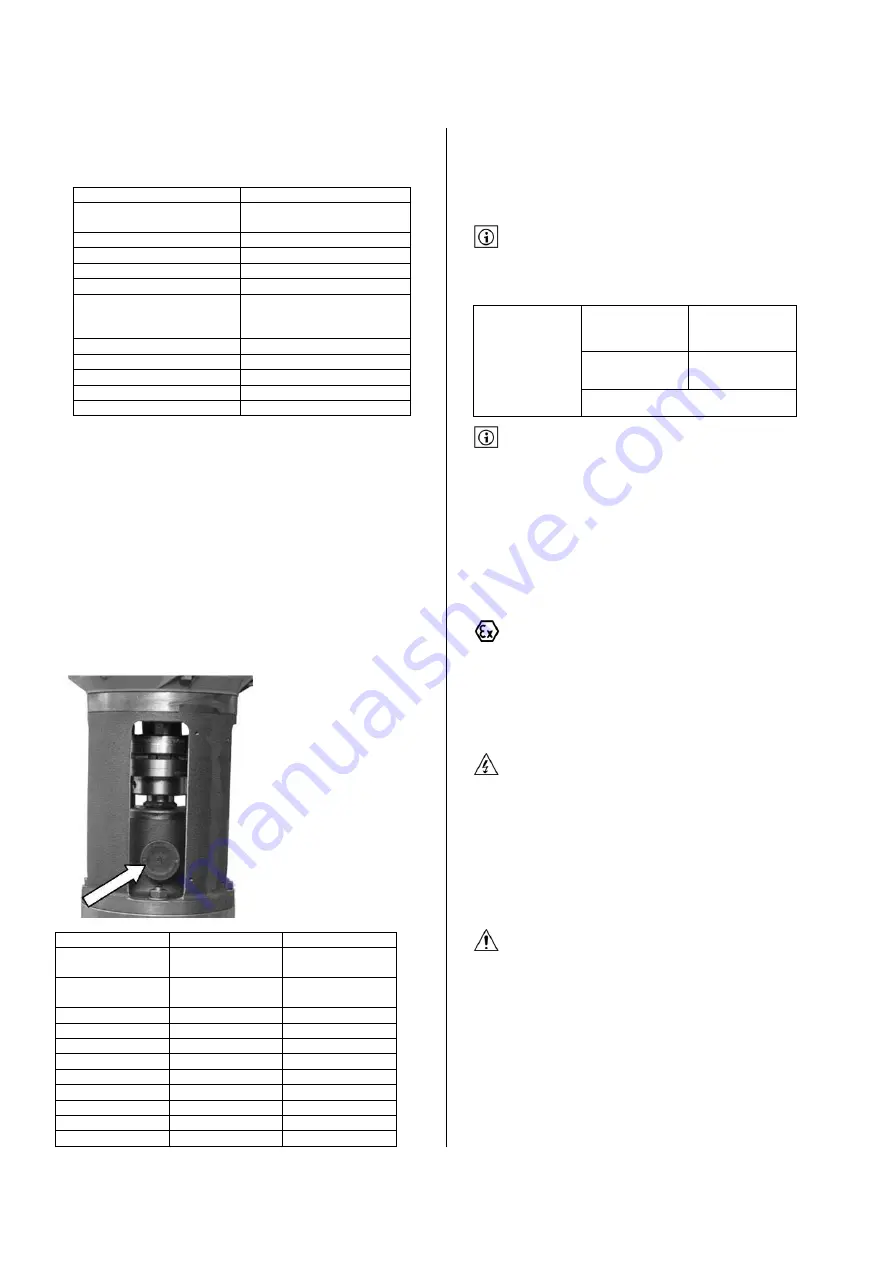
ENGLISH
18
-
Check coupling alignment (depending on pump variant),
-
Check if there is unusual noises (cavitations, hissing, purring, …) or
excessive vibrations.
Check point
Periodicity
State of the auxiliary systems
Depends on equipment type.
See dedicated equipment IOM
Motor
See manufacturer IOM
Shaft sealing
Weekly
Leaks from gaskets
Weekly
Oil level and grease quantities
Daily / Weekly / Monthly
Lubricants (ball bearings)
Replacement
frequency
according ball bearing type and
shaft speed
Bearings surface temperature
Monthly
Cleaning
Twice a year
Alignment and coupling wear
Twice a year
Noise, vibrations
Monthly
Anchoring quality
Yearly
Those frequencies are given for information only. They could be used as
a basis to the creation of a maintenance plan when starting a new
installation. Depending on installation conditions and use, the
periodicity will be shortened or prolonged.
9.2.1
LUBRICATION
NORMA V pumps use a bearing bracket fitted with lifetime lubricated
ball bearings (TH) or grease lubricated ball bearings (TM) integrating a
manually actuated greaser. Variants EM and CS have no ball bearing
inside.
For motor lubrication plan, please refer to the machine specific
instructions.
9.2.1.1
BEARING ASSEMBLY WIT H GREASER
Grease
NLGI2*
NLGI3
Temperature range
-20 to +100°C
(-4 to 212°F)
-20 to +100°C
(-4 to 212°F)
Description acc. To
DIN
KP2K-25
KP3K-20
BP
Energrease LS-EP2
Energrease LS-EP3
Elf
Multis EP2
Multis EP3
Fuchs
RENOLIT EP2
RENOLIT EP3
ESSO
Beacon EP2
Beacon EP3
Mobil
Mobilux EP2
Mobilux EP3
Q8
Rembrandt EP2
Rembrandt EP3
Shell
Alvania EP2
Alvania EP3
Texaco
Multifak EP2
Multifak EP3
SKF
LGEP 2
-
(*) NLGI 2 is a replacement grease and should not be mixed with other
quality of grease.
Grease quantity : 20 cm
3
.
9.2.1.2
LUBRICATION PLAN
First filling is performed in our plant during pump assembly.
Manual greaser must be tightened (1/4 turn) every 1000 hours or every
2 months.
Grease
change
intervals
Light
duty
conditions
n<1500 RPM
Standard or heavy
duty conditions
1500<n<3000 RPM
Every
3500 hours
Every
2500 hours
Or after 12 months
After 10000 operating hours or after 2 years, bearings should be
dismantled, cleaned and filled again with grease. For unfavorable
operating conditions (severely damp, dusty atmosphere or hot service)
greasing intervals may be shortened.
For grease replacement or re-lubrication, high quality lithium soap
grease should be used (eg. Mobilux 2, Esso Unirex N3, …).
9.3
DISMANTING AND RE-ASSEMBLY
9.3.1
DISMANTLING OF MOTOR
Make sure to operate in a safe area.
9.3.1.1
MOTOR ASSEMBLY TYPE CS AND EM
For those two motor assembly types it will be necessary to dismantle the
lineshaft before motor can be removed.
9.3.1.2
MOTOR ASSEMBLY TYPE TM AND TH
Make sure that electric power is disconnected (main power supply
and space-heater power supply). Only trained and qualified maintenance
operators are allowed to open motor junction box.
-
Open motor junction box and disconnect power cables. Disconnect
space heaters electric cable. Refer to motor instructions and
operating manual if necessary.
-
Identify cable connectors with corresponding phases and terminal
connectors in motor junction box. Secure and protect cables ends.
-
Disconnect sensors cables.
Select lifting devices according to the weight of goods to handle.
Motor weight is engraved on its nameplate.
-
Use slings and hooks to handle the motor. Use the lifting eyes or
lifting lugs available on motor frame to lift the motor.
-
Remove motor fastening srews/bolts [6577C].
Summary of Contents for Norma V Series
Page 2: ......
Page 34: ...FRAN AIS 34 13 DECLARATION CE...
Page 35: ...FRAN AIS 35...
Page 36: ...FRAN AIS 36...
Page 68: ...ENGLISH 34 13 EC DECLARATION OF CONFORMITY...
Page 69: ...ENGLISH 35...
Page 70: ...ENGLISH 36...
Page 73: ...5 1 1 1 2 2 1 2 2 WILO 2 3 2 4 2 4 1 25 68 5 C...
Page 74: ...6 2 4 2 2 4 3 2 5 WILO 2 6 2 7...
Page 77: ...9 3 3 1 3 2 3 3 6 WILO 3 4 25 3 4 1...
Page 83: ...15 7 7 1 ATEX 1 5 7 1 1 7 1 2 1 2 3 7 1 3 7 1 4 7 2 7 2 1 7 2 2...
Page 84: ...16 7 2 3 7 2 4 7 3 230 400 400 400 690 690 60079 14 7 3 1 Y 230 400 400 690 7 3 2 U...
Page 85: ...17 7 3 3 U 3 7 3 4 7 4 850 dU dt 2500 ATEX NPSHR NPSHA 40 55 8 8 1 2 1 ATEX...
Page 86: ...18 8 2 8 3 20 30 8 4 mwc HMTmwc Pbar x 100 d x 9 806 d CS ATEX 1 8 5 WILO 9 9 1...
Page 89: ...21 V18 TM TM 2 90 9 3 2 9 3 2 1 9 3 2 2 9 3 2 3 9 3 2 4 TM TH 9 3 2 5 6581 9200 4590A...
Page 98: ...30 2100 7416 M8 5 5 M6 4 7416 3 2 7412 9 3 9 3320 3250...
Page 101: ...33 10 SRV NPSH NPSH NPSH NPSH NPSH...
Page 102: ...34 11 12 12 1 12 2 90 12 3 2 DIN 24296 1 1 1 1 2 1 1 4 1 2 2...
Page 103: ...35 13...
Page 104: ...36...
Page 105: ...37...
Page 106: ...38...
Page 107: ...39...
Page 108: ...40...
Page 111: ......