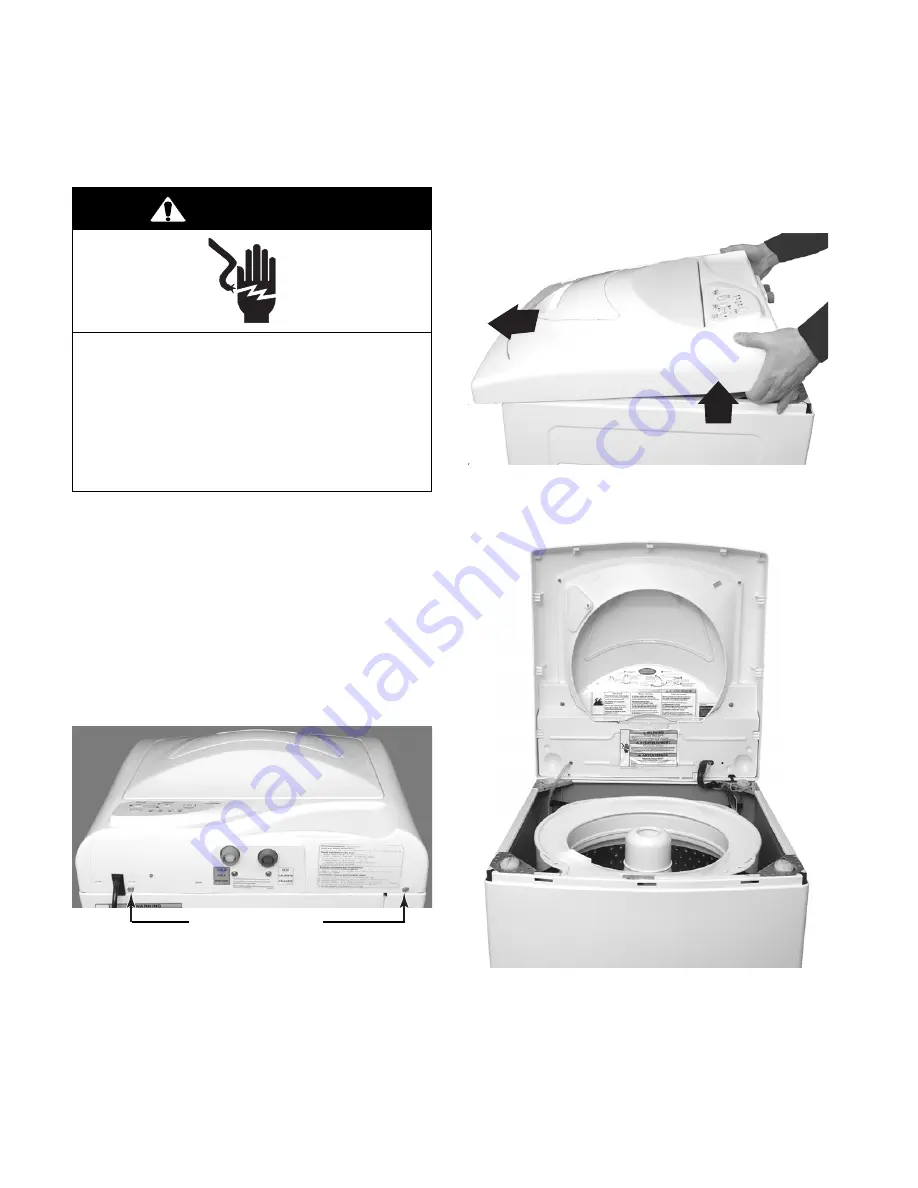
4-2
REMOVING THE PRESSURE SWITCH,
WATER INLET VALVES, LID SWITCH,
INTERFACE AND ELECTRONIC CONTROL BOARDS
Electrical Shock Hazard
Disconnect power before servicing.
Replace all parts and panels before
operating.
Failure to do so can result in death or
electrical shock.
WARNING
1.
Unplug washer or disconnect power.
2.
Turn off the water supply to the washer.
3.
Tape the lid of the washer closed so it does
not open when you handle the top cover in
the following steps.
4.
Pull the washer away from the wall so you
can access the rear of the unit.
5.
Remove the two 5/16
″
hex-head machine
screws from the back of the top cover.
6.
Lift the rear of the top cover and push it
forward to unhook it from the front.
7.
Rotate the front of the top cover up, and
rest it against a wall.
Top Cover Screws