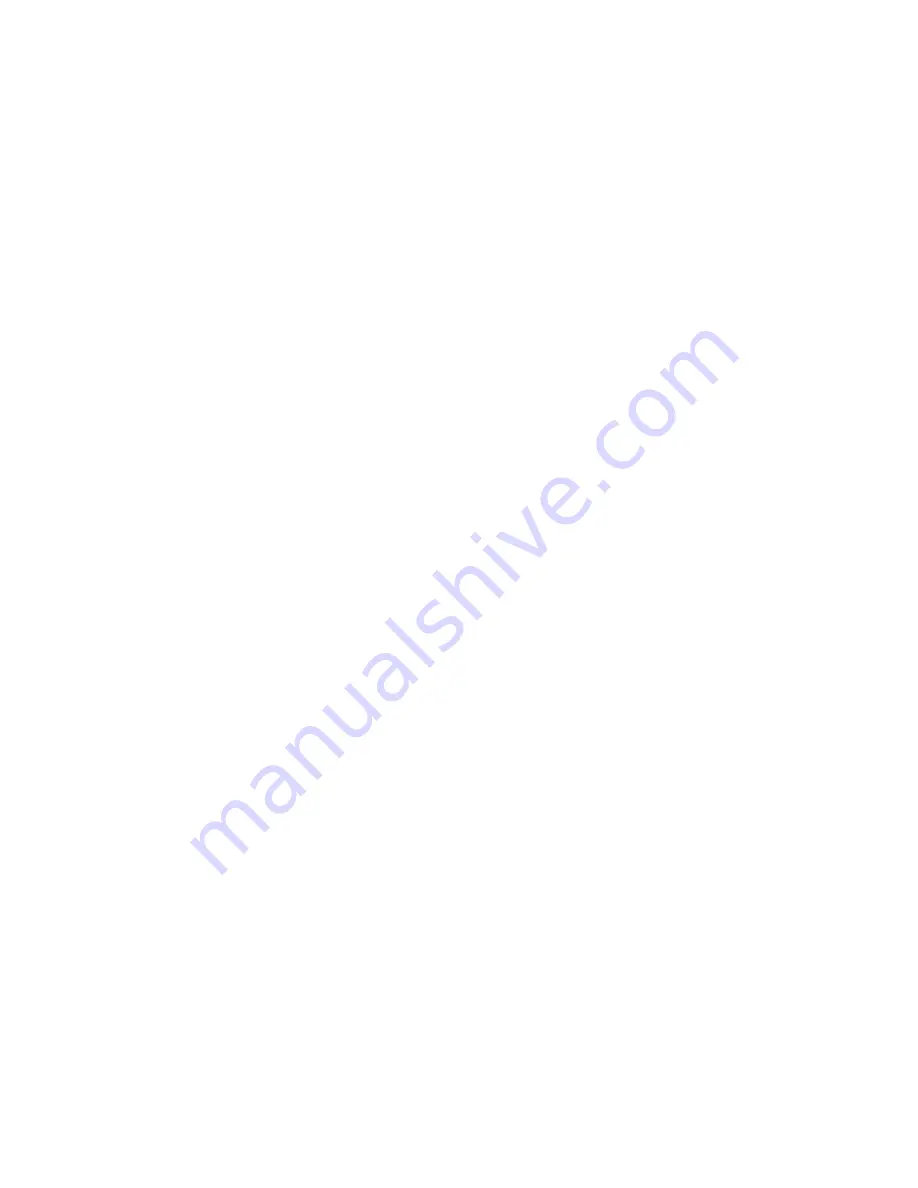
5
The Modular Drive System is the only product in the industry that allows the user to custom configure one
machine for various applications. The system consists of drives, plug-in control modules and carriages
that are easily assembled. The modular design allows the operator to quickly upgrade or reconfigure the
machine for straight line cutting and welding, stitch welding or weave welding. The system will run in any
position using Aluminum Rigid Rail, Aluminum Semi-Flex Rail [with a minimum radius of 15' (4.57 m)], Bent
Rigid Rail or Hi-Flex Rail [with a minimum radius of 40" (1 m)].
The straight line cutting and welding configuration consists of a carriage, master drive, racking group and
control module. The optional MDS-1060-10 Remote Control Cable can be used to remote the control
module.
A number of straight line control modules are available. The MDS-1002 Straight Line Module provides
simple direction and speed control for continuous cutting or welding. The MDS-1003 Stitch Module provides
a straight line and stitch welding mode with skip time, weld time and crater/puddle buildup time. The MDS-
1004 Programmable Stitch Module provides digital display of all stitch welding parameters. The MDS-1004
Stitch Module has closed position feedback so all distances are set in inches or mm as opposed to time and
are repeatable. The MDS-1055 Universal Limit Kit adds cycler, stop at limit and rapid return functions to the
MDS-1002 and MDS-1003 modules. The MDS-1004 Programmable Module has built in stop at limit and
rapid return modes. For more features, see the appropriate pages on each of the modules.
The Master Drive is rated at 60 lbs (27 kg) vertical load. (International Robotics Standards Rating)** The
machine is equipped with overload protection.
STANDARD FEATURES
The Master Drive Unit incorporates the following standard internal features:
•
High torque, low inertia motor for precise stops and starts.
•
Dedicated fail-safe brake with three times the stopping and holding power of the motor.
•
Motor overload protection which turns off the motor and engages the brake when excessive load is
placed on the machine.
•
Closed loop speed control for adjustable and repeatable control of critical welding or cutting parameters.
•
Closed loop position control to prevent position creep when the machine stops to perform an operation
such as crater fill at the end of a stitch weld.
**The International Robotics Standards Rating requires a minimum of 2:1 continuous-duty safety margin on
all power train and electronics components.
INTRODUCTION