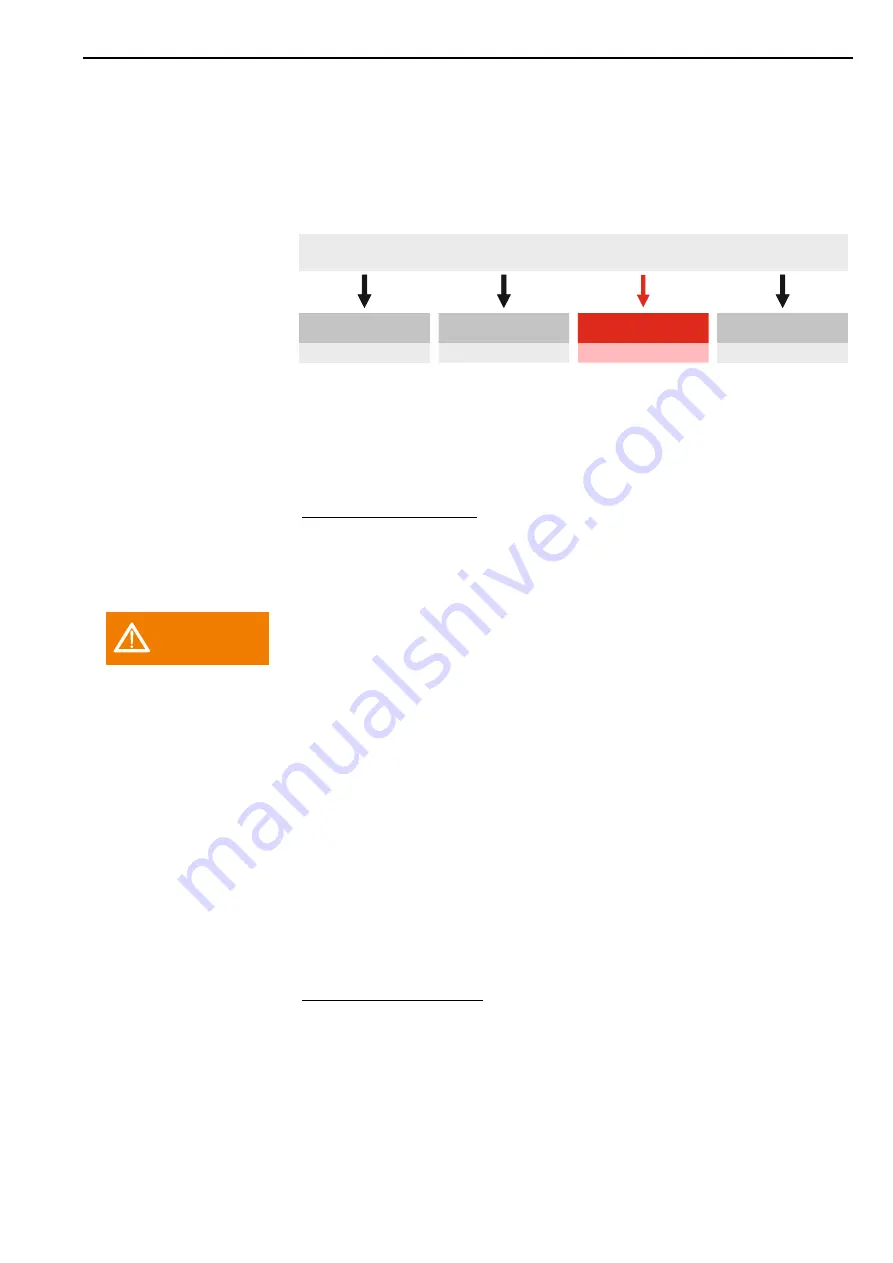
6. Setting of parameters
106082
– MRF-M2 -E - V0.7 - 23.04.2021
Page 31
6.4 Level
“Hardware configuration” (A parameters)
Switch to level
“Hardware configuration” see section 6.1
This configuration is very important and should be the first step when setting the
parameters for a system!
Assignment of digital input
Def.
A21 Functional access digital input
One of the following functions can be assigned to the digital input
here. The digital input must be connected to a corresponding poten-
tial-free switch contact.
The digital input of the regulator may only be connected
to a potential-free switch contact!!
Do not apply any external voltage - risk of destruction!!
0
0: deactivated
1: Remote start cooling
The cooling can be started from the OFF mode via the digital
input. No further parameters need to be set to use this function.
2: external temperature switching T1/T2 [P80=4]
The digital input is used to switch the target temperature. For
this, this option must also be activated in parameter [P80] = 4
3: external compressor lock (see section 7.7.2)
4: Freeze protection via low pressure switch (see section 7.7.3)
5: Compressor fault monitoring (see section 7.4)
6: Safety switch cover of the milk cooling vat
(Switch off the agitator when the lid is on) see section 7.5
PC interface setting RS485
Range
Def.
A95 Baud setting
1: 9600
2: 19200
3: 38400
1 .. 3
3
A96 Device address
1 .. 4
1
Code 212
Code 345
Code 0E5
Code 384
Working level
Cooling parameter 1
C parameter
Cooling parameter 2
P parameter
Hardware configuration
A parameter
I/O test parameter
o. parameter
WARNING