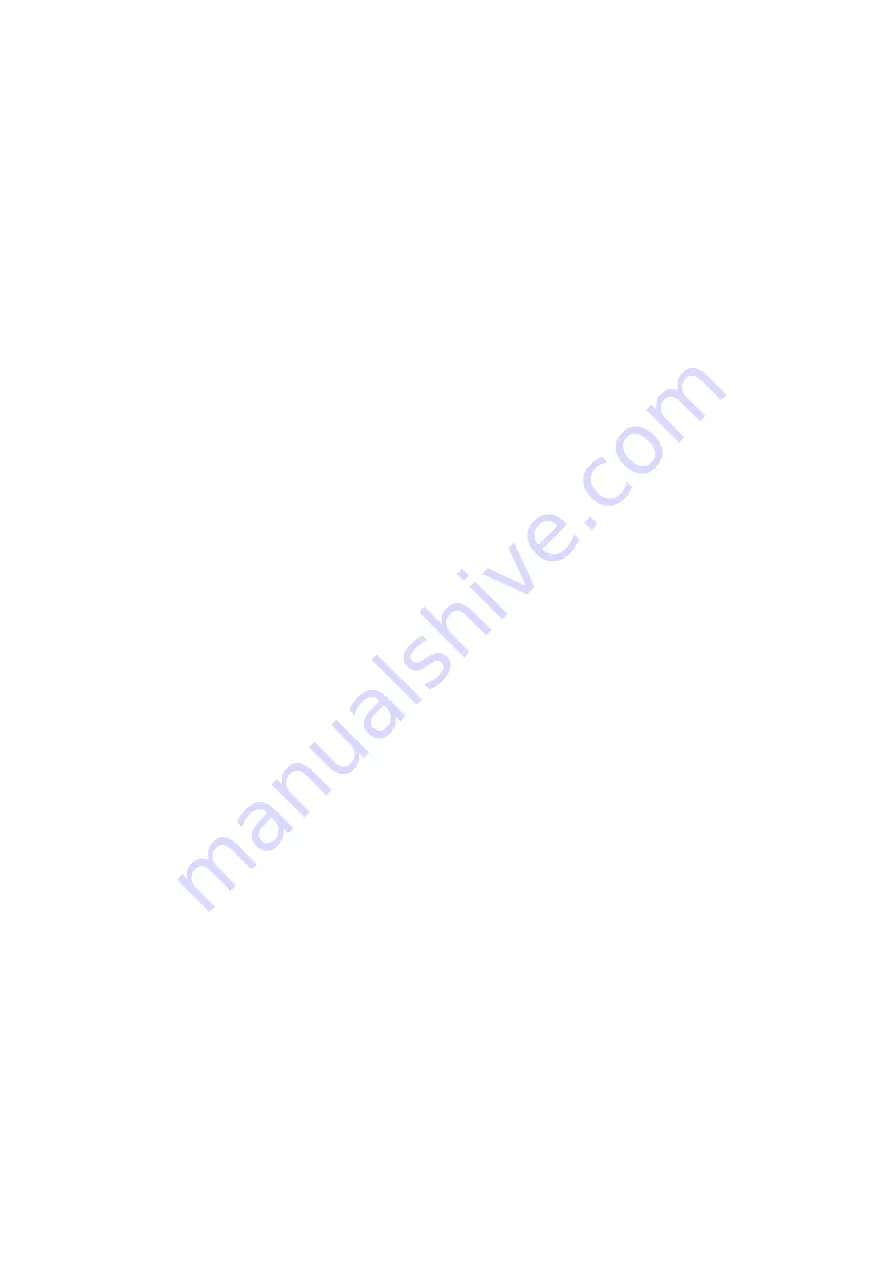
TOROMOCHO PROJECT - WEG MOTORS
TAG´s :
210-PP-001-M
210-PP-003-M 210-PP-101-M
210-PP-002-M
210-PP-004-M
Motor-generator sets are assembled and tested at the factory prior to delivery. However, before putting into service at
site, coupling alignment should be carefully checked as the metallic base could have suffered displacement during
transit due to internal stresses of the material. The metallic base is susceptible to distortion if secured to a foundation
that is not completely flat. Machines should not be removed from their common metallic base for alignment; the metallic
base should be level on the actual foundation with the aid of a spirit level (or similar instrument). When a metallic base is
used to adjust the height of the motor shaft end with the machine shaft end, the latter should be level on the
concrete base. After the base has been levelled, foundation, studs tightened, and the coupling checked, the metal base
and the studs are cemented.
3.1.3- ALIGNMENT
The electric motor should be accurately aligned with the driven machine, particularly in cases of direct coupling. An
incorrect alignment can cause bearing failure, vibrations and even shaft rupture. The best way to ensure correct
alignment is to use dial gauges placed on each coupling half, one reading radially and the other axially.
Thus, simultaneous readings are possible and allow checking for any parallel (Fig. 3.4) and concentricity deviations (Fig.
3.5) by rotating the shafts one turn. Gauge readings should not exceed 0.05 mm.
Fig. 3.4 - Deviation from parallelism
Fig. 3.5 - Deviation from concentricity
3.1.4- COUPLING
a) Direct Coupling
Direct coupling is always preferable due to low cost, space economy, no belt slippage and lower accident risk.
In cases of speed ratio drives, it is also common to use a direct coupling with a reducer (gear box).
CAUTION: Carefully align the shaft ends using, whenever feasible, a flexible coupling, leaving a minimum tolerance of 3
mm between the couplings (GAP).
b) Gear Coupling
Poorly aligned gear couplings are the cause of jerking motions which cause vibrations on the actual drive and on the
motor. Therefore, due care must be taken for perfect shaft alignment: exactly parallel in the case of straight gears and at
the correct angle for bevel or helical gears. Perfect gear engagement can be checked by the insertion of a strip of paper
on which the teeth marks will be traced after a single rotation.
c) Belt and Pulley Coupling
Belt coupling is most commonly used when a speed ratio is required. Assembly of Pulleys: To assemble pulleys on
shaft ends with a keyway and threaded end holes the pulley should be inserted halfway up the keyway merely by
manual pressure. On shafts without threaded end holes, the heating of the pulley to about 80ºC is recommended, or
alternatively, the devices illustrated in Figure 3.6 may be employed.
Fig. 3.6 – Pulley mounting device
Fig. 3.7 - Pulley extractor
Hammers should be avoided during the fitting of pulleys and bearings. The fitting of bearings with the aid of hammers
leaves blemishes on the bearing races. These initially small flaws increase with usage and can develop to a stage that
completely impairs the bearing. The correct positioning of a pulley is shown in Figure 3.8.
Fig. 3.8 - Correct positioning of pulley on the shaft.
RUNNING: To avoid needless radial stresses on the bearings it is imperative that shafts are parallel and the pulleys
perfectly aligned. (Figure 3.9).
Fig. 3.9 - Correct pulley alignment
Pulleys that are too small should be avoided; these cause shaft flexion because belt traction increases in proportion to a
decrease in the pulley size. Table 1 determines minimum pulley diameters, and Table 2 and 3 refer to the maximum
stresses acceptable on motor bearings up to frame 355.
Fig. 3.10 - Belt tensions
Laterally misaligned pulleys, when running, transmit alternating knocks to the rotor and can damage the bearing
housing. Belt slippage can be avoided by applying a resin (rosin for example). Belt tension should be sufficient to avoid
slippage during operation.
Concerning ODP NEMA 48 & 56 fractional motors, these have the following features:
- Rotor: Squirrel cage
- Protection: Open drip proof
- Insulation: Class “B” (130ºC) - IEC 34
- Cooling system: internal
Summary of Contents for Warman 650 M200-MCR-G
Page 1: ......
Page 3: ......
Page 4: ......
Page 5: ......
Page 6: ......
Page 8: ......
Page 9: ......
Page 10: ......
Page 11: ......
Page 97: ...SUPLEMENTO M9 DEL MANUAL EMITIDO JUNIO DE 1998 7 Copyright WARMAN INTERNATIONAL LTD ...
Page 125: ......
Page 126: ......
Page 127: ......
Page 128: ......
Page 129: ......
Page 130: ......
Page 131: ......
Page 132: ......
Page 133: ......
Page 243: ......
Page 244: ......
Page 274: ......