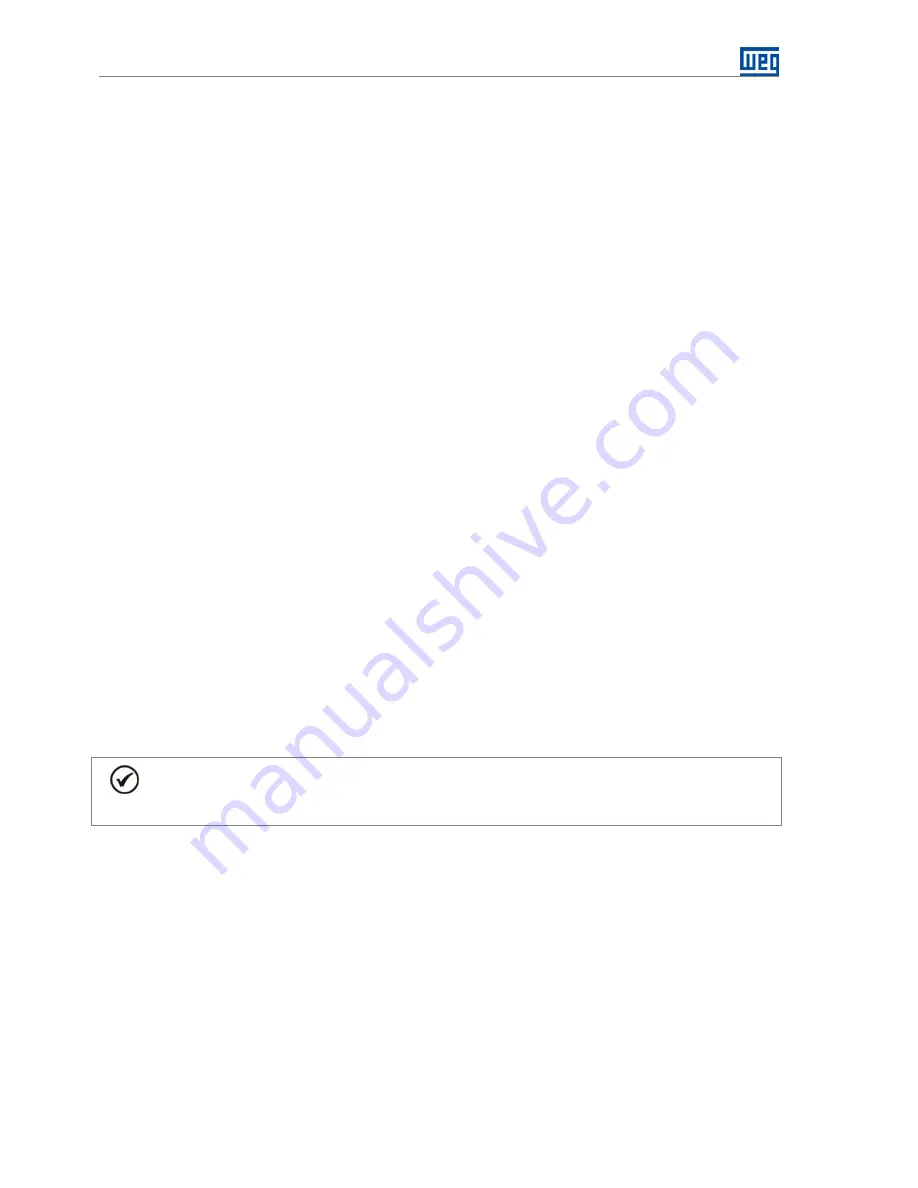
Crane
Crane | 18
2.2 HORIZONTAL MOTION
The crane horizontal motion consists in moving a load horizontally, executing commands for load forward and
load reverse together with the mechanical brake control, which must assure that the load remains in the
intended position when no load forward or load reverse commands exist.
The crane horizontal motion control developed for the CFW500 SoftPLC presents the following characteristics:
■
Speed reference selection through electronic potentiometer (EP), logical combination of digital inputs
(maximum of 5 references), analog input (step less) or communication networks;
■
Commands for load forward and load reverse through digital inputs or through communication networks;
■
Option of inverting the motor rotation direction adopted as standard for load forward and load reverse;
■
Linear or “S” curve acceleration and deceleration ramps for crane horizontal motion;
■
Option of stopping command via digital input, which can be for coast to stop, fast stop or emergency stop
with deceleration ramp;
■
Minimum and maximum speed limits for crane horizontal motion;
■
Gain, offset and filter settings for control speed signal through analog input;
■
Mechanical brake release logic controlled by motor frequency and/or motor current and/or motor torque;
■
Possibility of brake release delay time;
■
Mechanical brake closing logic controlled only by motor frequency (total speed reference in Hz);
■
Possibility of brake closing delay time;
■
Adjust of the time to enable a new command to brake release after the command to brake closing preventing
a new command to be generated without the brake being mechanically closed;
■
Possibility of brake inhibition during the transition from load forward to load reverse and vice-versa;
■
Digital inputs programmed for limit switches (over travel limits) functions to reduce the speed (slowdown) while
load forward and to reduce the speed (slowdown) while load reverse;
■
Lightweight detection while load forward or load reverse;
■
Momentary overload detection while load forward or load reverse, with subsequent alarm;
■
Inverter in torque limitation detection while load forward or load reverse, with subsequent fault;
■
Fault trip by improper use of the crane horizontal motion;
■
Crane horizontal motion alarm (the last three);
■
Possibility of applicative implementation or modification by the user through the WLP software.
2.3 CONTROL CONNECTIONS
The selection of the speed reference defines four different control connection types, because it can be through
electronic potentiometer (EP), logical combination of digital inputs (maximum of 5 references), analog input (step
less) or communication networks. The control connections (analog inputs/outputs and digital inputs/outputs) are
made at the plug-in of the CFW500 frequency inverter.
NOTE!
Refer to the CFW500 frequency inverter manual and the plugin module installation guide used for
more information on the connections.
Summary of Contents for Crane CFW500 series
Page 2: ......