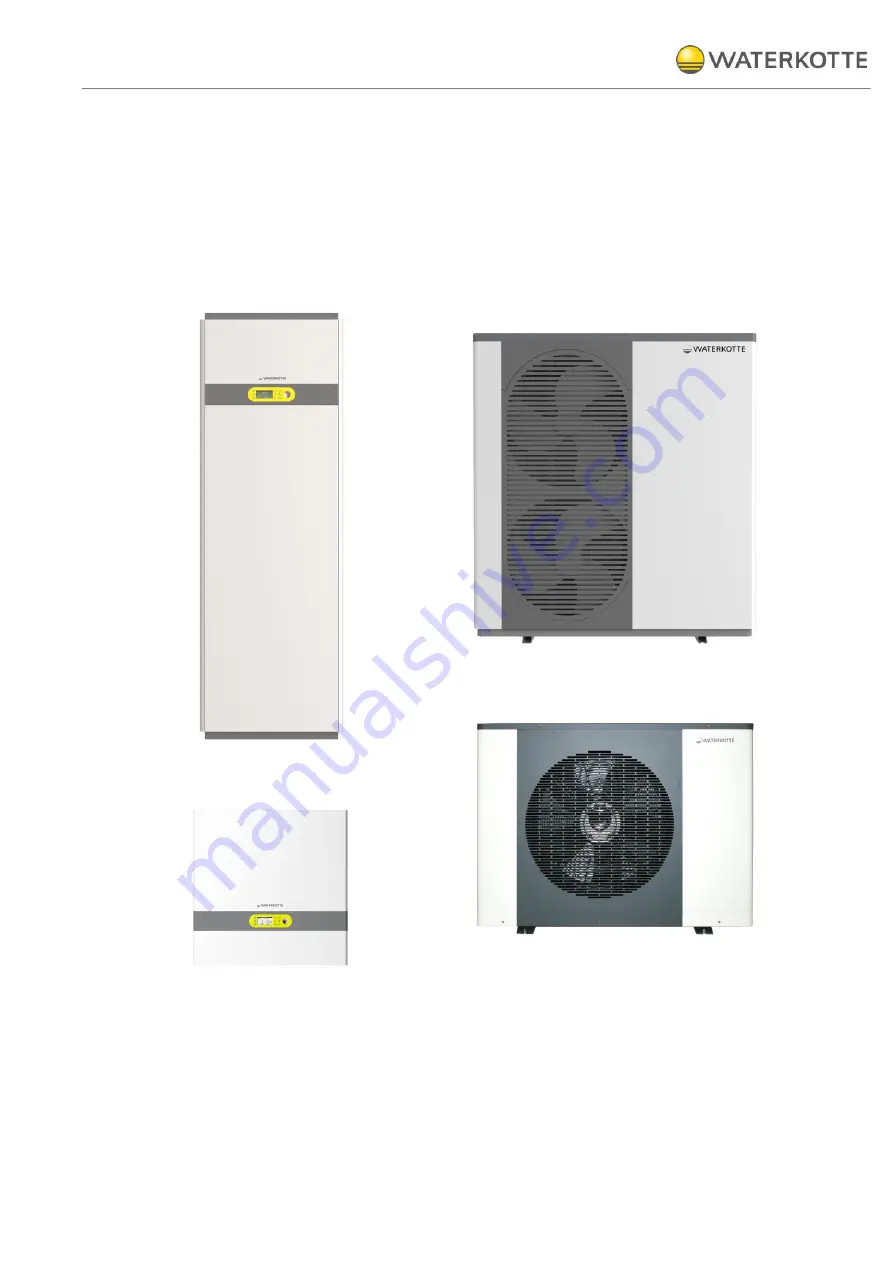
Planning and installation
Basic Line Ai1 Air
Air to water heat pump
WATERKOTTE GmbH, Gewerkenstraße 15, D-44628 Herne
Tel.: 0049/(0)2323/9376-0, Fax: 0049/(0)2323/9376-99, E-Mail: [email protected]
Internet: http://www.waterkotte.de
21.10.2015 / Z21437
Basic Line Ai1 Air – Indoor unit
Basic Line BS7010 – Hydraulikstation
- Indoor unit
Basic Line Ai1 Air /Basic Line BS 7010
- Outdoor unit
Basic Line Ai1 Air /Basic Line BS 7006
- Outdoor unit