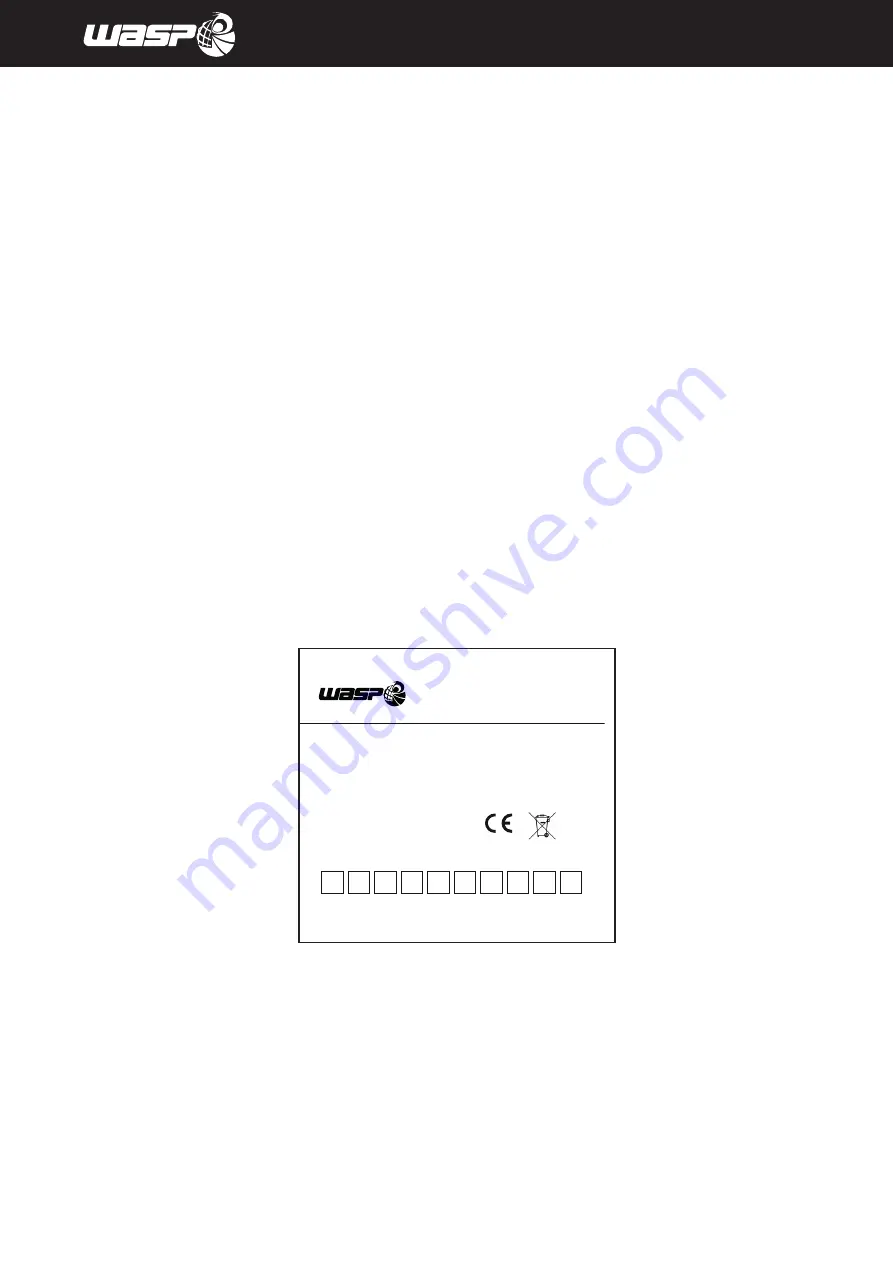
INTRODUCTION
© WASP S.r.l.
1
7
General information
1
1 GENERAL INFORMATION
1.1. Manufacturer identification data
WASP S.r.l.
Via Castelletto, 104 - 48024 Massa Lombarda (RA) Italy
Tel. +39 0545 87858
[email protected] / www.3dwasp.com
1.2. Indentification label
The printer is CE marked and complies with all relevant provisions:
Machinery Directive 2006/42 / EC, EMC Directive 2014/30 / EU and LVD Directive 2014/35 / EU
EN 55022
EN 55024
EN 60204-1
The marking can be identified by means of an identification plate of the Manufacturer as required by the Machinery
Directive. In case of damage, the Recipient must commission a copy.
Legend:
1. Stampante 3D: 3D printer
2. Modello: Model
3. Rif. TCT: Reference
4. Input: input power
5. Potenza Max: Maximum power absorption
6. Corrente a pieno carico: full load current
7. Anno di Produzione: Year of production
8. Numero di serie: Serial number
220v-240v
Stampante 3D
Modello: WASP 4070 HDP
Rif. TCF: WASP 4070 HDP
Input: 220V-240V 50/60Hz
Potenza Max: 2400W
Corrente a pieno carico: 9,8A
Anno di produzione: 2022
Numero di serie:
MADE IN ITALY
WASP s.r.l. via Castelletto 104
Massa Lombarda (RA) Italy
www.3dwasp.com
Summary of Contents for 4070 HDP
Page 1: ...MANUAL OF USE AND MAINTENANCE ORIGINAL INSTRUCTIONS WASP4070HDP ...
Page 4: ......
Page 14: ...INTRODUCTION WASP S r l 1 14 1 ...
Page 51: ...INTRODUCTION WASP S r l 51 Ordinary and extraordinary maintanance ...
Page 59: ...INTRODUCTION WASP S r l 59 Ordinary and extraordinary maintanance ...
Page 67: ...INTRODUCTION WASP S r l 67 Ordinary and extraordinary maintanance ...
Page 70: ...INTRODUCTION WASP S r l 70 Ordinary and extraordinary maintanance ...
Page 75: ...INTRODUCTION WASP S r l 75 Use of the printer Fig 8 4 Free Zeta System ...
Page 92: ...WASP S R L Via Castelletto 104 48024 Massa Lombarda RA Italia www 3dwasp com info 3dwasp com ...