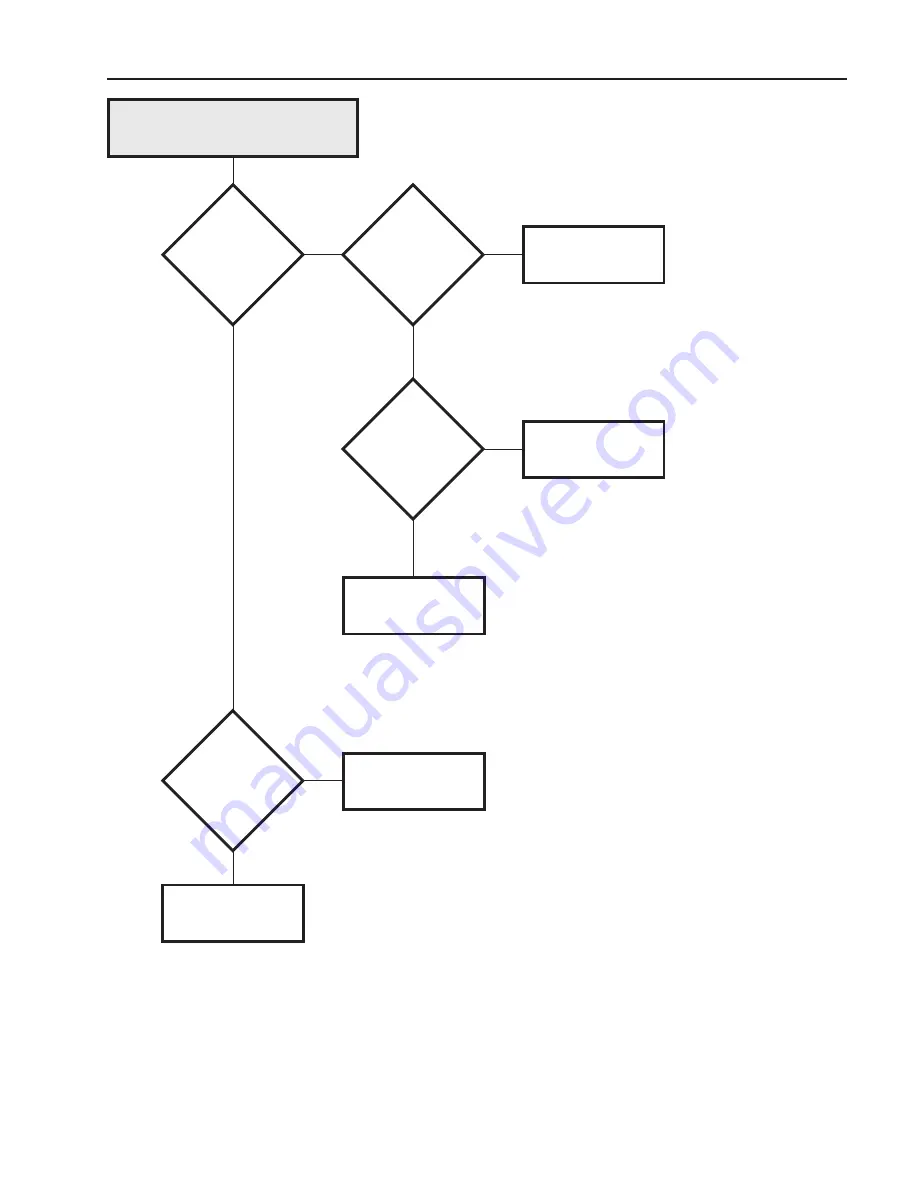
Wash program cannot be
selected
Are only some
buttons not
functioning?
Yes
No
Connect panel plate
correctly
Is panel plate
correctly
connected?
Yes
No
Change panel plate
Is cable
connector for
panel plate correctly
fitted and clean?
No
Yes
Rectify
Is connector
clean?
Yes
No
Change PCB
Clean it
Fault-finding
5
95.08
Summary of Contents for Selecta S28/125
Page 2: ......
Page 6: ......
Page 35: ...28 Mechanical and electrical design 1791 46 S28 185 208 240 V 60 Hz single phase...
Page 55: ...Fault finding Circuit Board...
Page 76: ......