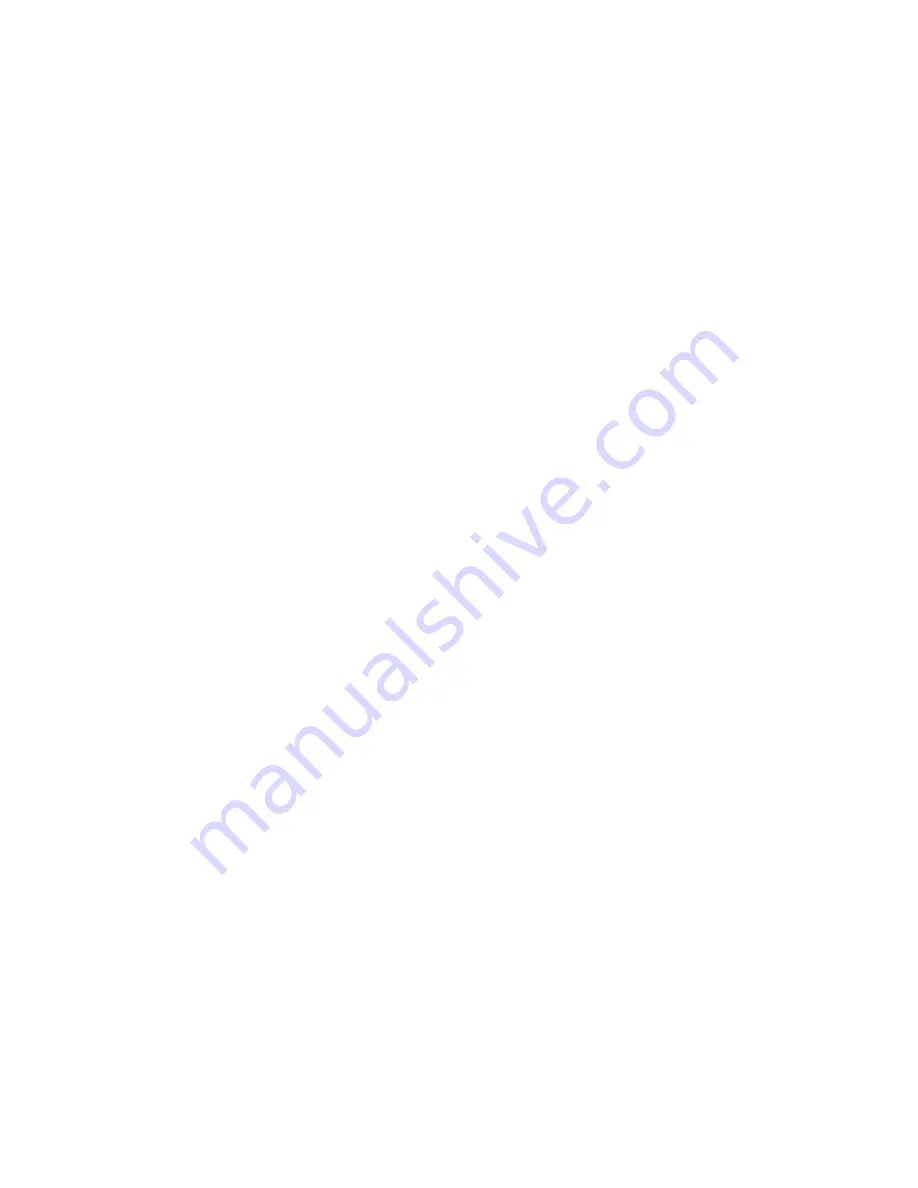
14
Warner Electric • 800-825-9050
P-0204-WE • 819-0485
Burnishing
Intimate metal to metal contact is essential between
the armature and the metal rings (poles) of the magnet
or rotor . Warner Electric clutches and brakes leave the
factory with the friction material slightly undercut to
assure good initial contact .
Normally, the desired wearing-in process occurs nat-
urally as the surfaces slip upon engagement . The time
for wear-in, which is necessary to obtain the ultimate
torque of the unit, will vary depending on speed, load,
or cycle duty .
If maximum torque is required immediately after instal-
lation, the unit should be burnished by slipping the
friction surfaces together at reduced voltage . It is rec-
ommended that the burnishings be done right on the
application, if at all possible .
Burnishing at high speed will result in a smoother
wear-in pattern and reduce the time for burnishing .
The voltage should be set at approximately 30% or
40% of the rated value .
The unit should be cycled on and off to allow sufficient
time between slip cycles to prevent overheating .
When a Warner Electric brake or clutch is properly
assembled and installed, no further servicing, lubrica-
tion, or maintenance should be required throughout
the life of the unit .
Maintenance
Wear Pattern:
Wear grooves appear on the armature
and magnet surfaces . This is a normal wear condition,
and does not impair functioning of the unit . Normally,
the magnet and armature, as a mating pair, will wear
at the same rate . It is the usual recommendation that
both components be replaced at the same time .
Remachining the face of a worn armature is not rec-
ommended . If a replacement armature is to be used
with a used magnet, it is necessary to remachine the
worn magnet face . In refacing a magnet: (1) machine
only enough material to clean up the complete face of
the magnet; (2) hold the face within .005” of parallel
with the mounting plate; and (3) undercut the molded
facing material .001” - .003” below the metal poles .
Heat:
Excessive heat and high operating temperatures
are causes of rapid wear . Units, therefore, should be
ventilated as efficiently as possible, especially if the
application requires fast, repetitive cycle operation .
Foreign Materials:
If units are used on machinery
where fine, abrasive dust, chips or grit are dispelled
into the atmosphere, shielding of the brake may be
necessary if maximum life is to be obtained .
Where units are used near gear boxes or transmis-
sions requiring frequent lubrication, means should be
provided to protect the friction surfaces from oil and
grease to prevent serious loss of torque .
Oil and grease accidently reaching the friction surfac-
es may be removed by wiping with a rag dampened
with a suitable cleaner, which leaves no residue . In
performing this operation, do not drench the friction
material .
If the friction materials have been saturated with oil
or grease, no amount of cleaning will be completely
effective . Once such a unit has been placed back in
service, heat will cause the oil to boil to the surface,
resulting in further torque loss .
Torque Loss:
If a brake or clutch slips or loses torque
completely, the initial check should be the input volt-
age to the magnet or field as follows:
90-Volt Series:
Connect a DC voltmeter with a range
of 0-100 or more directly across the magnet or field
terminals . With the power on and the potentiometer
turned up, a normal reading is 90 volts, although 85
to 95 is satisfactory . The reading should drop as the
potentiometer control is adjusted counterclockwise .
24-Volt Series:
Use a DC voltmeter with a range of
0-30 volts or more . A normal reading is approximately
22-26 volts .
6-Volt Series:
Use a DC voltmeter of approximately
0-15 volt range . A normal reading is from 5 .5 to 6 .5
volts .
The above checks normally are sufficient . Further
checks may be made as follows: a low range amme-
ter, when connected in series with one magnet lead,
will normally indicate approximately .40 amperes for
the 90 volt units, 1 .0 ampere for the 24 volt, and 3 .5
amperes for the 6 volt series . These readings are with
the power on and the potentiometer control in the
maximum position .
Ohmmeter checks should be made with the power
off and the circuit open (to be certain, disconnect one
lead to the magnet) . Average resistance for the 90 volt
series is 220 ohms; for the 24 volt, 20 ohms; and for
the 6 volt series, 1 .5 ohms . A very high or infinite resis-
tance reading would indicate an open coil .
If the above checks indicate that the proper voltage
and current is being supplied to the magnet, mechani-
cal parts should be checked to assure that they are in
good operating condition and properly installed .
Burnishing and Maintenance
Send Quote Requests to [email protected]
Call +1(800)985-6929 To Order or Order Online At Warnerelectricparts.com
Send Quote Requests to [email protected]
Call +1(800)985-6929 To Order or Order Online At Warnerelectricparts.com