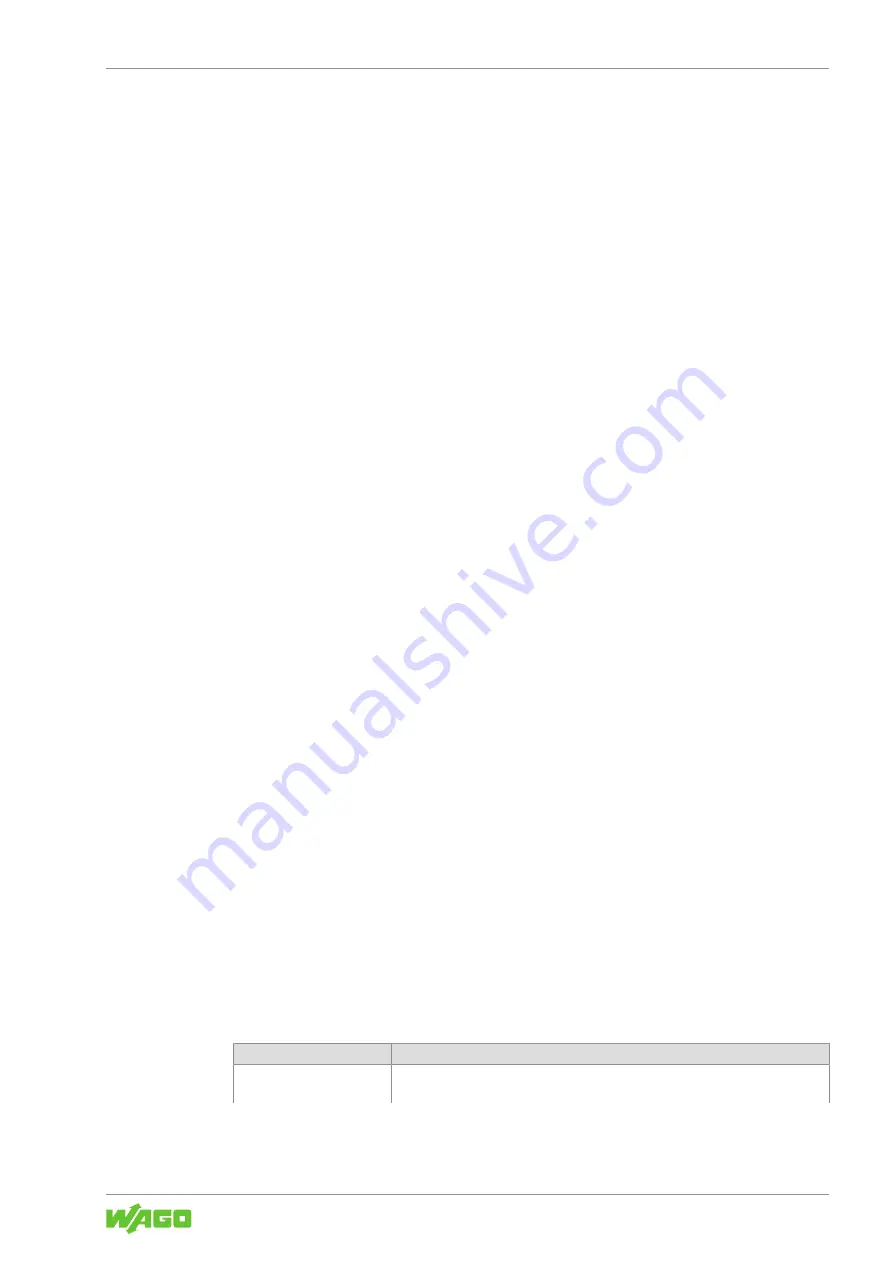
765-1202/0100-0000
Functions
Product manual | Version: 1.0.0
27
16DIO FLD EC DC 24V 2.0A
“Forcing” Operating Mode Must Be Enabled in the Parameterization
The “Forcing” operating mode can be switched off by the higher-level controller. This is
done with the “Force mode setting” parameter – see
8
enable forcing, the “Force mode setting” parameter value must be set to 0 (“Enable force
mode”). This is the default setting in the device description file provided with the device.
The functional scope described can vary depending on the module type.
5.3 Monitoring Functions
The 765 Series modules have extensive internal sensors for measuring:
• Temperatures
• Currents
• Voltages
The measurements are performed for the module and for pin 1, pin 2 and pin 4 of each
port. The measured values can be displayed in the WAGO I/O Field Webserver or the
WAGO I/O Field app. Alternatively, an OPC UA client can read out the measured values
and display them.
In the module, the measured values are compared to limiting values. An alarm or event is
generated if a value falls above or below a limiting value (e.g., a temperature limiting
value). The module can send this alarm/event
• EtherCAT
®
: Send emergency telegram to the controller, or the controller can read the
diagnostic history object (Index 0x10F3),
• to the OPC UA client upon: OPC UA: event.
The OPC UA client application can use the measured values, for example to implement
load management. You can find information on load management in
8
5.4 Overload protection
The module has built-in overload protection and periodically measures the current, volt-
age and temperature.
If the output current, supply voltage or temperature exceeds the maximum value, the
module switches off a pin/port
5.5 Parameterization Tools
5.5.1 Overview
There are several ways to set the module’s parameters. The following table provides an
overview of the tools.
Table 27: Overview of Parameterization Tools
Tool
Description
Controller with EtherCAT
®
Master
The
EtherCAT master
must be configured to exchange process data with the
765 Series modules.