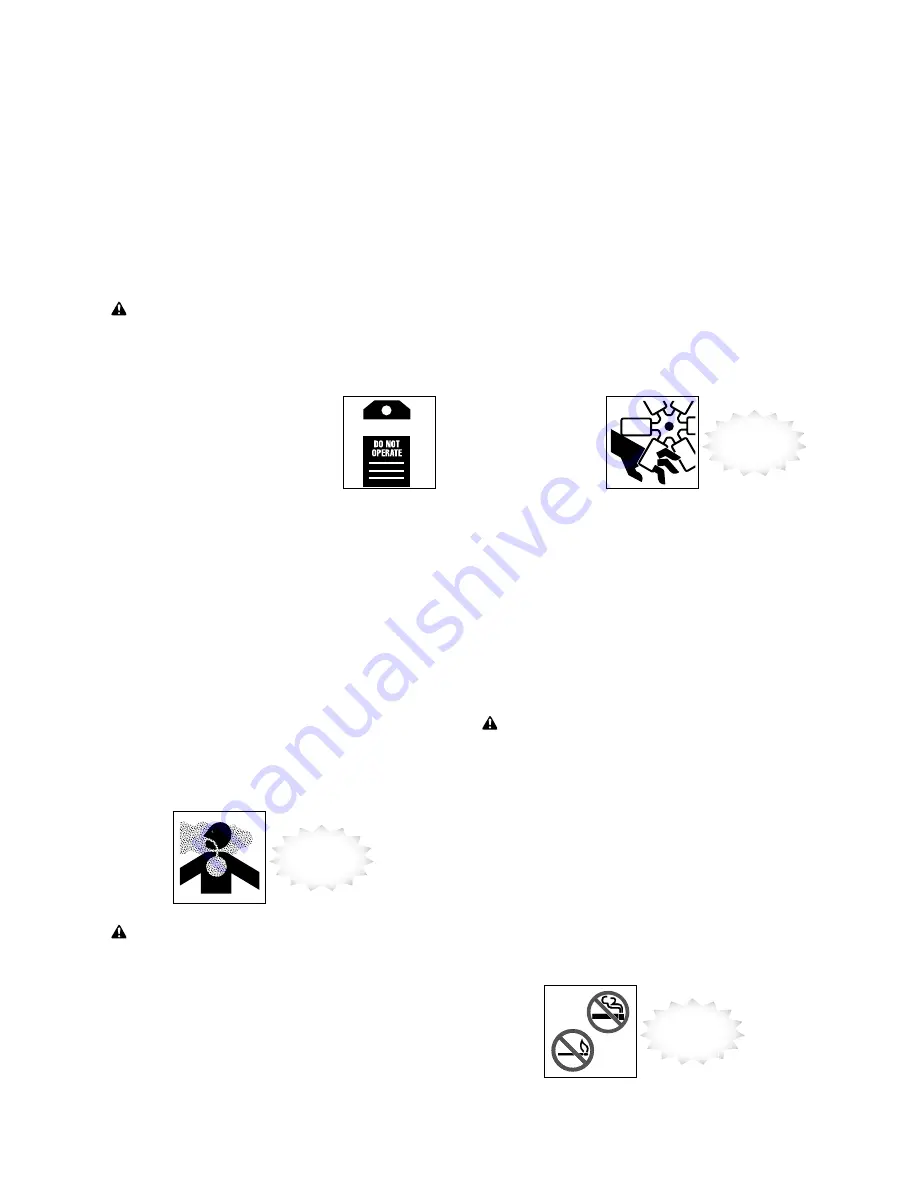
Attach a “DO NOT OPERATE” warning tag to the
control levers. Lockout/tagout the unit according to the
manufacturer’s operating manual(s). If there is a key,
remove it and take it with you.
Install approved support device(s) when working under
or near raised equipment.
Remove only guards or covers that provide access to
the area being serviced. Replace all guards and covers
when work is complete.
Do not operate the machine with gaurds removed.
WARNING!
Avoid injury or death.
Never work on
machinery with the engine running unless instructed
by the manufacturer’s manual(s) for specific service.
Trowel Maintenance and Repair
MAKE SURE
the trowel is
disconnected from the power source
or the appropriate circuits are dead
and OSHA Lockout/Tagout is applied
before doing any maintenance or
repair work on the trowel.
Trowel Blades, Pans and Attachments
• Do not attempt to clean, service or perform
adjustments on the trowel while it is running.
• Do not remove blades or pans while the trowel
is hanging overhead. Always support the trowel
securely on a flat, level surface before changing
blades or pans.
• Always handle blades and pans carefully. Worn
blades or pans may develop sharp edges that can
cause serious cuts.
• Always replace worn or damaged parts with service
parts designated by the manufacturer.
• Replace blades and pans as a complete set – even
if only one blade or pan is showing wear or damage.
They can wear differently depending on different jobs,
and a difference in blade size will damage the finish
of the slab surface.
• Only use
manufacturer
approved
polishing
and brush
attachments.
WARNING
Avoid
rotating parts
25
Perform Maintenance Safely
25
Common Maintenance
Safety Practices
Use Proper Ventilation
Never run an engine in an enclosed area without an
approved ventilation system.
WARNING!
Exhaust fumes contain carbon
monoxide which could be deadly if inhaled.
Never
operate any type of engine without proper
ventilation.
EXHAUST FUMES CAN KILL.
A feeling of tiredness, or nausea, is an indication of
being overcome by exhaust. Shut the engine off
immediately if this occurs.
Fuel Hazards
WARNING!
Avoid serious injury or death.
Always
use approved fuel containers and/or fuel dispensing
equipment to reduce the risk of explosion or fire.
Always observe these practices to reduce the possibility
of a serious accident:
• Shut off engine and ignition during refueling.
• Turn off all electrical switches.
• Ground the fuel nozzle against the filler neck.
• Keep sparks and open flames away from fuel. Do
not smoke while refueling or when handling fuel
containers.
• Do not cut or weld on or near fuel lines, tanks or
containers.
• Do not overfill the tank or spill fuel. Clean up spilled
fuel immediately. Clean spills immediately.
No smoking and no
open flames
Ventilate work area
Perform Maintenance Safely
26
Summary of Contents for Trowel CT 24-4A
Page 6: ......
Page 16: ...Labels CT 24 4A 16 wc_si000742gb fm 2 Labels 2 1 Label Locations...
Page 65: ...33 Notes 34 Notes...
Page 68: ......