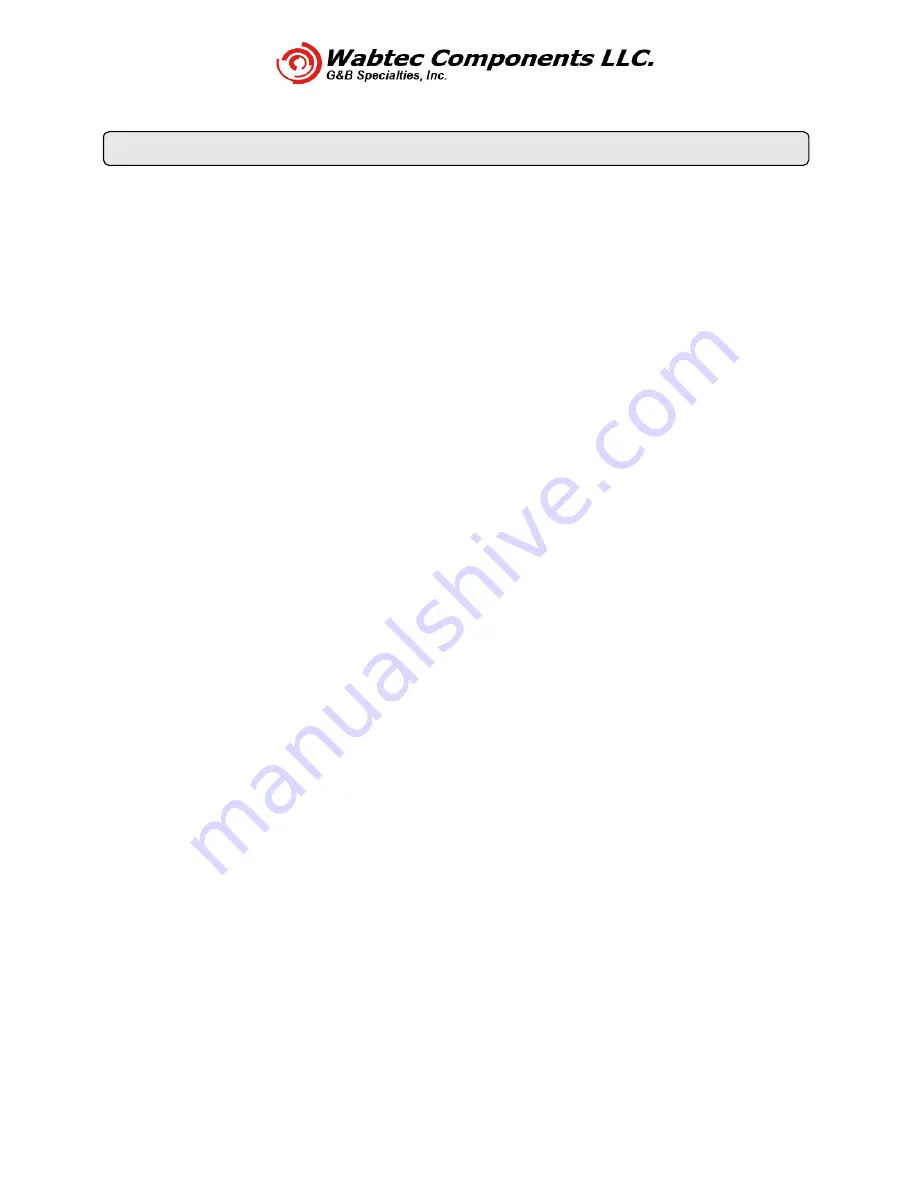
MIO-R290GM2011 Rev E
G&B Specialties Inc. 535 West 3
rd
Street, Berwick, PA, USA Tel: (570) 752-5901 Fax: (570) 752-6397
US Field Service: 570-441-6988; CAN Field Service 570-854-0482; www.rafna.com
-103-
R
AIL
W
HEEL
L
OAD
A
DJUSTMENT
During rail travel, the railgear removes a predetermined portion of the vehicle’s load from
the vehicle’s wheels and carries it on the rail wheels. A minimum amount of load must be
maintained on the rail wheels to avoid derailment. Likewise, a minimum amount of load must
be maintained on the vehicle wheels to provide traction for acceleration and braking, this
load at installation must be a minimum of 450 lbs and a maximum of 750 lbs and is checked as
described below using a bottle jack equipped with a gauge.
The rail wheel load should be adjusted following the installation of the railgear and once the
vehicle has had all its permanent load (service body, crane, welders, etc.) installed. The rail
wheel load requires periodic checks; however, it should only require re-adjustment if the
railgear is moved, the permanent vehicle equipment is changed, or the vehicle suspension
settles or is changed. The rail wheel load should be checked at regular intervals that coincide
with regular maintenance schedule for the vehicle or minimally once a year during vehicle
annual FRA inspection. As non-permanent load is added to and/or removed from the vehicle,
the rail wheel load will change also. This is acceptable if the weight ratings of the vehicle,
axles, wheels, tires and railgear are not exceeded and if the minimum rail wheel load is
maintained and the maximum wheel load of 750 lbs per wheel is not exceeded.
Check each rail wheel load as follows:
1.
Place the vehicle on a straight and level section of rail with the railgear lowered to the
rail position. Ensure the railgear is taking load through the tread of the rail wheel and not
on the flange of the rail wheel. The vehicle should only be carrying the permanently
attached load (service body, crane, etc.) and any always carried non-attached load
(welders, etc.) during this procedure. Do not include the operator or passengers. Ensure
the vehicle tires are not in contact with any obstructions except the rails.
2.
Place the hydraulic bottle jack on a solid surface beneath the rail wheel spindle housing
and jack the rail wheel off the rail.
3.
Insert a piece of paper between the rail and the rail wheel. Lower the jack until the rail
wheel squeezes the paper so that it cannot be pulled out.
4.
Slowly jack up the rail wheel while pulling on the paper and observe the jack gauge. When
the paper can be pulled out, stop jacking.
5.
Record the load or pressure reading on the jack gauge. If necessary, convert the pressure
reading to a load reading using the supplied table