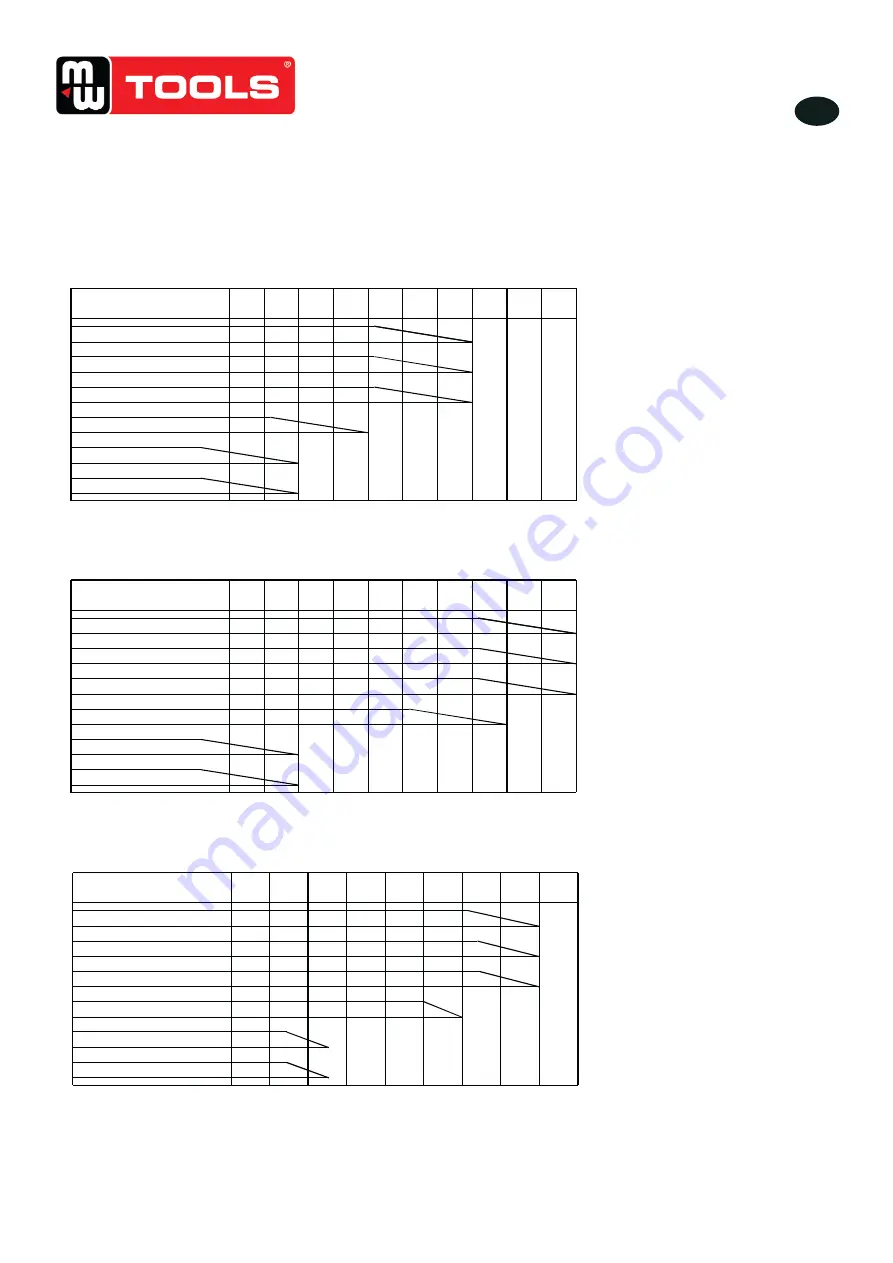
40
EN
M1.2.CUT80HFI.NLFREN 09102018
4�4 Cutting parameters table
Select proper current according to the cutting parameters table, workpiece material, cutting thickness and cutting speed,
etc. The figure in the below table is an approximation.
Cutting speed (m/min) when cutting current is 40 A:
Cutting speed (m/min) when cutting current is 60 A:
13
The workpiece is not cut fully. This may be caused by:
The cutting current is too low.
The cutting speed is too high.
The electrode and nozzle of the torch are burned.
The workpiece is too thick.
Molten slag drops from the bottom of workpiece. This may be caused by:
The cutting speed is too low.
The electrode and nozzle of the torch are burned.
The cutting current is too high.
3.6 Cutting parameters table
Select proper current according to the cutting parameters table, workpiece material, cutting
thickness and cutting speed, etc. The figure in the below table is an approximation.
(
)
Table 3-1: Cutting speed
in when cutting current is 40A
(
)
m/m
9
8
7
6
5
4
3
2
1
0.1
0.4
0.4
0.4
1.5
1.5
1.5
1.5
8
8
8
8
0.75
0.75
Cutting thickness mm
(
)
Mild steel
Galvanized steel
Stainless steel
Aluminum
Brass
Red copper
0.12
0.15
0.15
0.15
25
20
15
10
5
0.1
0.1
0.1
0.1
0.3
0.3
0.3
0.2
0.5
0.5
0.5
0.3
1.9
1.9
1.9
0.8
0.5
0.5
Cutting thickness mm
(
)
Mild steel
Galvanized steel
Stainless steel
Aluminum
Brass
Red copper
Table 3-2: Cutting speed
in when cutting current is 60A
(
)
m/m
13
The workpiece is not cut fully. This may be caused by:
The cutting current is too low.
The cutting speed is too high.
The electrode and nozzle of the torch are burned.
The workpiece is too thick.
Molten slag drops from the bottom of workpiece. This may be caused by:
The cutting speed is too low.
The electrode and nozzle of the torch are burned.
The cutting current is too high.
3.6 Cutting parameters table
Select proper current according to the cutting parameters table, workpiece material, cutting
thickness and cutting speed, etc. The figure in the below table is an approximation.
(
)
Table 3-1: Cutting speed
in when cutting current is 40A
(
)
m/m
9
8
7
6
5
4
3
2
1
0.1
0.4
0.4
0.4
1.5
1.5
1.5
1.5
8
8
8
8
0.75
0.75
Cutting thickness mm
(
)
Mild steel
Galvanized steel
Stainless steel
Aluminum
Brass
Red copper
0.12
0.15
0.15
0.15
25
20
15
10
5
0.1
0.1
0.1
0.1
0.3
0.3
0.3
0.2
0.5
0.5
0.5
0.3
1.9
1.9
1.9
0.8
0.5
0.5
Cutting thickness mm
(
)
Mild steel
Galvanized steel
Stainless steel
Aluminum
Brass
Red copper
Table 3-2: Cutting speed
in when cutting current is 60A
(
)
m/m
Cutting speed (m/min) when cutting current is 80 A:
14
3.7 Replacement of electrode and nozzle
When the phenomena below occur, the electrode and nozzle should be replaced. Otherwise,
there will be strong arc in the nozzle, which will break down the electrode and the nozzle, or even
burn the torch. Nozzles of different models are different, so ensure the nozzle is of the same
model when replacing it.
Electrode wear 1.5mm
>
Distortion of the nozzle
Cutting speed declining, arc with green flame
Difficult in arc ignition
Irregular cut
0.25
0.5
0.5
0.5
25
20
15
5
0.1
0.3
0.3
0.3
3.3
2.9
3.3
2
0.7
0.7
10
1.1
0.95
1.1
0.6
30
35
40
0.1
0.1
0.1
0.1
0.1
0.38
0.65
0.65
0.65
0.15
0.1
Cutting thickness mm
(
)
Mild steel
Galvanized steel
Stainless steel
Aluminum
Brass
Red copper
Table 3-4: Cutting speed
in when cutting current is 100A
(
)
m/m
0.25
0.5
0.5
0.5
25
20
15
5
0.1
0.3
0.3
0.3
3.3
2.9
3.3
2
0.7
0.7
10
1.1
0.95
1.1
0.6
30
35
40
0.1
0.1
0.1
0.1
0.1
0.38
0.65
0.65
0.65
0.15
Cutting thickness mm
(
)
Mild steel
Galvanized steel
Stainless steel
Aluminum
Brass
Red copper
Table 3-3: Cutting speed
in when cutting current is 80A
(
)
m/m
copyrighted
document
- all
rights
reserved
by
FBC