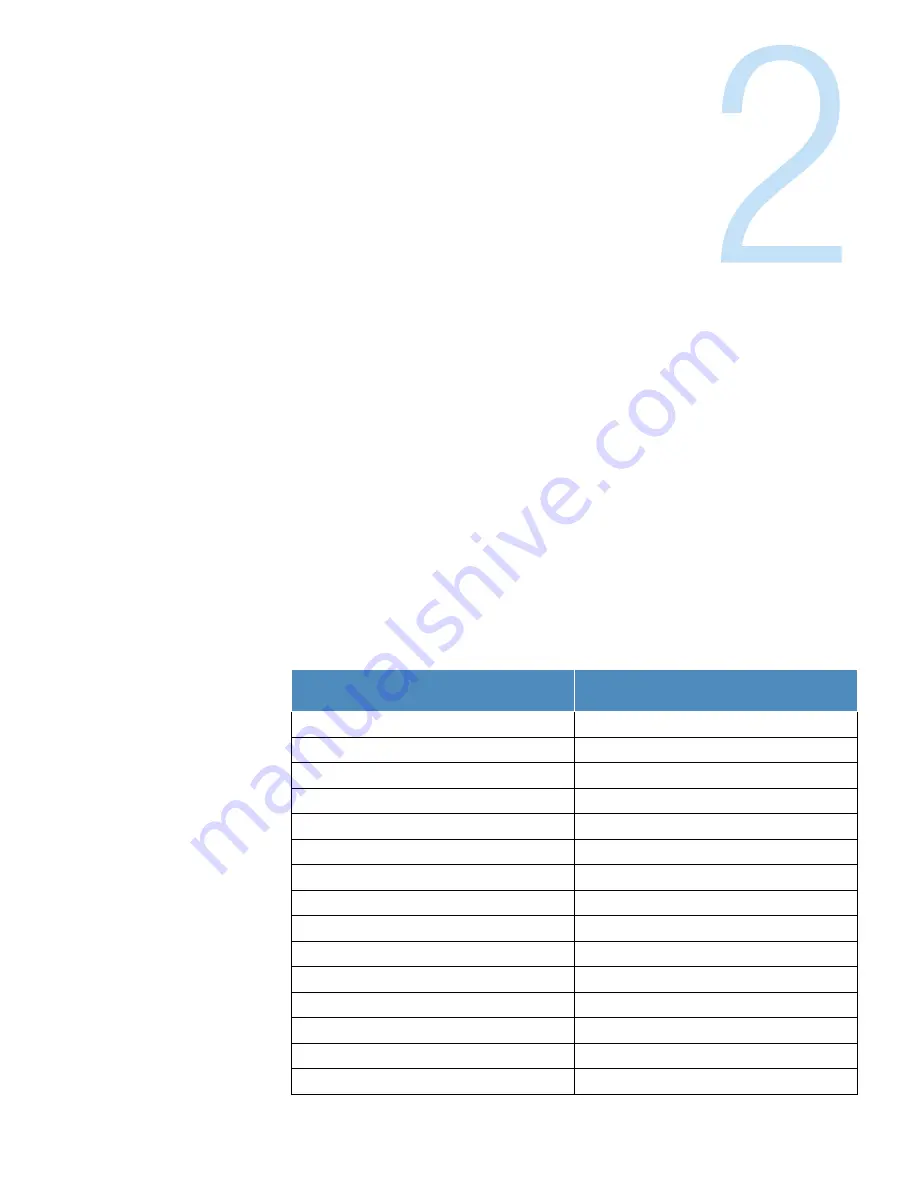
VWR
CO2 Incubator Basic |
11
Delivery
Packaging
The CO
2
incubator Helix is delivered in a stable packaging box. All packaging materials can be
separated and are reusable:
Packaging carton: Recycled paper
Foam elements: Styrofoam (CFC-free)
Pallet: Untreated wood
Packaging film: Polyethylene
Packaging ribbons: Polypropylene
Components standard equipment
Delivery
CO
2
incubator with single glass door and with
continuous shelves (standard version)
Shelf 3
Shelf support post
4
Shelf support rail
6
Insert for pressure compensation opening
1
Plug for pipe channel
1
Power supply cable
1
Connector, potential-free contact
1
Spare caps, set
1
CO
2
connecting hose set
1
Immersion water pump
1
Open-end wrench, 24 mm
1
Allen wrench 2 mm for blower wheel
1
Allen wrench 3 mm for blower wheel cover
1
Operating instructions
1
Pump for water draining
1
Summary of Contents for CO2 Incubator Basic
Page 1: ...VWR CO2 Incubator Basic 50150229 Revision 0 December 2015 ...
Page 54: ... Shut down 52 CO2 Incubator Basic VWR Chapter 8 ...
Page 62: ... Cleaning and disinfection 60 CO2 Incubator Basic VWR Chapter 9 ...
Page 74: ... Parts and accessories 72 CO2 Incubator Basic VWR Chapter 11 ...
Page 78: ... Technical data 76 CO2 Incubator Basic VWR Chapter 12 ...
Page 83: ...VWR CO2 Incubator Basic 81 Certificate of decontamination ...
Page 84: ... Certificate of decontamination 82 CO2 Incubator Basic VWR Chapter 15 ...
Page 85: ......
Page 86: ......